切削油の管理方法|品質維持と長寿命化の秘訣を徹底解説

機械加工の現場において、切削油は単なる消耗品ではありません。加工精度や工具寿命、生産効率、さらには作業環境に至るまで、その品質と状態は多岐にわたる影響を及ぼします。「切削油がすぐに腐って臭いがひどい」「頻繁に交換が必要でコストがかさむ」「油剤の性能が安定せず加工不良が起きやすい」…こうした悩みは、適切な切削油管理を行うことで大幅に改善できる可能性があります。
切削油を常に最適な状態で使用し、その寿命を最大限に延ばすためには、日々の点検から定期的なメンテナンス、そして適切な品質管理が不可欠です。この記事では、私たちサンワケミカル株式会社が推奨する切削油の管理方法について、具体的な手順やポイントを徹底的に解説します。切削油の管理レベルを向上させ、安定した生産体制とコスト削減を実現するための一助となれば幸いです。
1. 日常管理の重要性と具体的なチェック項目
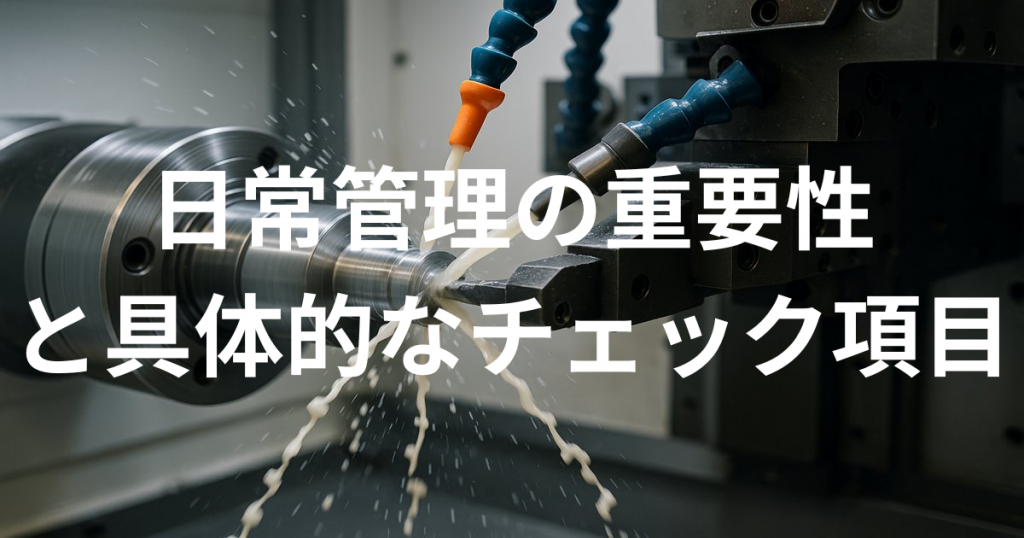
切削油の性能を維持し、トラブルを未然に防ぐためには、日々の地道な管理が最も重要です。なぜなら、日常的なチェックを通じて切削油のわずかな変化を早期に捉えることができれば、大きな問題に発展する前に対処することが可能になるからです。
なぜ日常管理が重要なのか?
- 加工品質の安定化
切削油の状態を良好に保つことで、潤滑性、冷却性などの性能が安定し、寸法精度や面粗度のばらつきを抑えることができます。 - 工具寿命の維持・延長
適切な濃度や清浄度が保たれた切削油は、工具摩耗を抑制し、工具コストの削減に繋がります。 - トラブルの早期発見・予防
異臭、変色、浮遊物、漏れなどの異常を早期に発見することで、腐敗の進行や機械の故障といった深刻なトラブルを未然に防ぐことができます。 - 切削油寿命の延長
こまめな管理によって劣化要因を取り除くことで、切削油の交換頻度を減らし、油剤コストや交換作業の負担を軽減できます。 - 作業環境の維持
腐敗による悪臭や、泡立ちによるタンクからの溢れ、床面の汚染などを防ぎ、安全で快適な作業環境を保つことができます。
具体的な日常チェック項目と確認方法
最低限、以下の項目は毎日始業前などに確認することを推奨します。
- 液面レベル
- 確認方法
クーラントタンクの液面計やゲージを確認します。 - チェックポイント
適正な液量範囲内にあるか? 極端に減っていないか? (液漏れや蒸発過多の可能性) - 重要性
液面が低すぎると、ポンプが空気を吸い込み、泡立ちやキャビテーションの原因となります。また、油剤全体の量が少ないと、温度が上がりやすくなったり、汚れが濃縮されたりします。
- 確認方法
- 外観(色、透明度、浮遊物、浮上油)
- 確認方法
タンク内の切削油を目視で確認します。透明な容器に少量汲み取って観察するとより分かりやすいです。 - チェックポイント
- 色・透明度
新品時と比較して、著しい変色(黒ずみ、白濁など)や透明度の低下はないか? (劣化、異物混入、バクテリア繁殖の可能性) - 浮遊物
切りくずやスラッジ、ゴミなどが浮遊・沈殿していないか? - 浮上油
機械の摺動面油などが大量に浮いていないか? (油圧作動油などの漏れがないか?)
- 色・透明度
- 重要性
外観の変化は、劣化、汚染、腐敗のサインであることが多いです。特に浮上油は、切削油の性能を低下させ、バクテリアの栄養源となり腐敗を促進するため、早期の除去が必要です。
- 確認方法
- 臭い
- 確認方法
タンクに鼻を近づけて臭いを確認します。 - チェックポイント
腐敗臭(ドブのような臭い、硫黄臭など)やカビ臭はしないか? いつもと違う刺激臭はないか? - 重要性
異臭、特に腐敗臭は、バクテリアが大量に繁殖しているサインです。放置すると急速に劣化が進行し、作業環境も悪化します。
- 確認方法
- 機械周辺の漏れ
- 確認方法
クーラントタンク周り、配管、ポンプ、機械本体などを目視で確認します。 - チェックポイント
切削油が漏れている箇所はないか? - 重要性
漏れは切削油の無駄遣いになるだけでなく、床面を汚し、転倒などの事故の原因にもなります。また、漏れ箇所から異物が混入する可能性もあります。
- 確認方法
毎週行うチェック項目(推奨)
日常点検に加え、週に一度程度、以下の項目もチェックすると、より精密な管理が可能です。
- 濃度(水溶性)
屈折計などで測定し、推奨範囲内にあるか確認します。(詳細は切削油の品質を維持するためのポイントを参照) - pH(水溶性)
pH試験紙などで測定し、極端な低下がないか確認します。(詳細は切削油の品質を維持するためのポイントを参照) - フィルターの状態
フィルターの詰まり具合や破損がないか確認します。
異常を発見した場合の初期対応
日常点検で異常を発見した場合は、以下の手順で対応しましょう。
- 記録と報告
発見した異常の内容、日時、機械名を記録し、上司や担当者に速やかに報告します。 - 原因の簡易調査
明らかな原因(例:配管の緩みによる漏れ)が特定できれば対応します。 - 応急処置
- 浮上油が多い場合
オイルスキマーを作動させる、ひしゃくなどで可能な範囲で除去する。 - 液面低下
原因を確認しつつ、必要に応じて補充する(濃度管理に注意)。 - 漏れ
可能であれば応急的な補修を行うか、機械を停止して修理を手配する。
- 浮上油が多い場合
- 専門家への相談
原因が不明な場合や、腐敗臭、著しい変色など、劣化が疑われる場合は、切削油メーカー(サンワケミカル株式会社など)に相談し、適切な対処法の指示を仰ぎましょう。
2. 定期的なメンテナンス(清掃、交換)のタイミングと手順
のタイミングと手順-1024x538.png)
日常管理を徹底していても、切削油は徐々に劣化・汚染していきます。そのため、定期的なタンクの清掃と切削油の交換は、良好な状態を維持するために不可欠なメンテナンスです。
クーラントタンク清掃の重要性と頻度
クーラントタンクの底には、日常のフィルターでは除去しきれない微細な切りくずや砥粒、沈殿したスラッジ(油、金属粉、バクテリアの死骸などが混ざったもの)が溜まっていきます。これらは、以下のような問題を引き起こします。
- バクテリアの温床
スラッジはバクテリアの格好の住処となり、腐敗や悪臭の原因となります。 - 切削油性能の低下
スラッジが撹拌されて油剤中に混入すると、潤滑性や冷却性を低下させます。 - フィルターやポンプの詰まり
堆積したスラッジがポンプに吸い込まれると、故障の原因となります。 - 加工不良
微細な異物が加工面に傷をつけたり、工具の切れ味を悪化させたりします。
タンク清掃の適切な頻度は、機械の使用状況、加工内容、切削油の種類、日常管理のレベルによって大きく異なります。一般的には半年から1年に1回が目安とされますが、これはあくまで目安です。日常点検でタンク底のスラッジ堆積状況を確認し、汚れが目立つようであれば早めに清掃を実施することが重要です。耐腐敗性に優れた切削油を使用したり、高性能なフィルターを導入したりすることで、清掃間隔を延長できる場合もあります。
切削油の交換時期の判断基準
切削油の交換時期も、一律に決めるのは困難です。以下のようなサインが見られたら、交換を検討する必要があります。
- 強い腐敗臭
殺菌剤などを使用しても改善されない、我慢できないほどの強い臭いが発生している。 - 著しい変色・白濁
油剤が黒褐色や灰色に著しく変色したり、白濁して透明感が失われたりしている。 - pHや濃度の異常
pHが推奨範囲から大きく外れ、調整してもすぐに戻ってしまう。濃度管理が困難になっている。 - 加工不良の頻発
原因不明の寸法不良や面粗度不良が多発するようになった。 - 皮膚トラブルの発生
作業者の手荒れなどの皮膚トラブルが増加している。 - メーカー推奨期間の経過
特に推奨期間が定められている油剤の場合。 - 定期分析結果
細菌数や劣化度合いなどを分析し、基準値を超えている場合。
これらのサインは、単独ではなく複合的に現れることが多いです。日常管理の記録と合わせて、総合的に判断することが重要です。迷った場合は、切削油メーカーにサンプルを送って分析してもらうのも有効な手段です。
タンク清掃と切削油交換の手順
安全かつ確実に行うために、以下の手順を参考にしてください。
- 準備
新しい切削油、清掃用具(ヘラ、ブラシ、ウエス、掃除機、高圧洗浄機など)、必要に応じてタンク洗浄剤・殺菌剤、保護具(手袋、ゴーグル、マスク)を準備します。 - 旧液の抜き取り
ポンプやドレンから古い切削油を完全に抜き取ります。抜き取った廃液は、法令(廃棄物処理法など)に従って、許可を持つ専門業者に委託するなど、適切に処理してください。決して下水などに流してはいけません。 - 切りくず・スラッジ除去
タンク内に残った切りくずやスラッジを、ヘラや専用の掃除機などを使って物理的に除去します。 - タンク内洗浄
- 水洗い
まず水でタンク内壁や配管内部を洗い流します。高圧洗浄機を使うと効果的です。 - 洗浄剤・殺菌剤の使用(推奨)
汚れやバクテリアがひどい場合は、切削油メーカー推奨のタンククリーナー(洗浄剤と殺菌剤が一体になったものが多い)を使用します。クリーナーを適量タンクに入れ、水を張って数時間循環させた後、廃液を抜き取ります。(使用方法は製品の指示に従ってください) - 注意点
洗浄剤・殺菌剤の成分がタンク内に残留すると、新しい切削油の性能に悪影響を与える可能性があるため、使用後は念入りにすすぎを行うことが重要です。
- 水洗い
- すすぎ・乾燥
洗浄剤を使用した場合は特に、タンク内をきれいな水で十分にすすぎます。その後、ウエスで水分を拭き取るか、自然乾燥させます。 - 新液の準備と注入
- 正しい希釈
水溶性切削油の場合は、メーカー指定の推奨濃度になるように、必ず水に原液を少しずつ攪拌しながら加えて希釈します。(原液に水を加えると、うまく乳化・溶解しない場合があります) - 注入
準備した新しい切削油をタンクに注入します。
- 正しい希釈
- 試運転と記録
ポンプを作動させ、漏れがないか、正常に循環するかを確認します。交換日、交換量、使用した油剤名などを管理記録に残します。
3. 切削油の品質を維持するためのポイント(pH、濃度、異物管理)
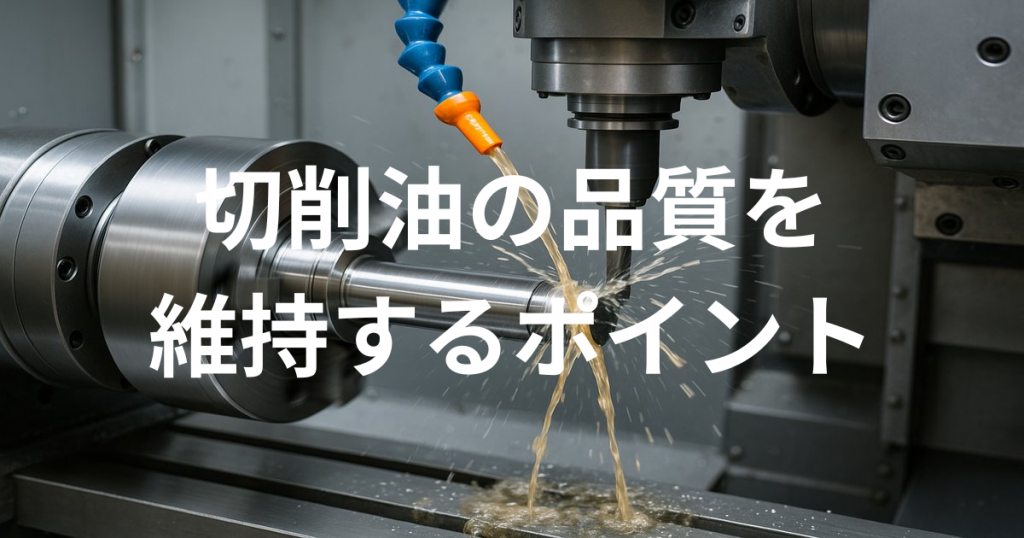
切削油の性能を最大限に引き出し、長持ちさせるためには、その品質を常に良好な状態に保つことが重要です。特に重要な管理項目として、「pH」「濃度」「異物」の3つが挙げられます。
pH管理?なぜ重要?どう管理する?
- pHとは?
水溶液の酸性・アルカリ性の度合いを示す指標です。pH7が中性、それより低いと酸性、高いとアルカリ性になります。 - 重要性
- 防錆性
一般的な水溶性切削油は、pHを弱アルカリ性(通常8.5~9.5程度)に保つことで、鉄系の金属が錆びるのを防いでいます。pHが低下すると防錆性能が著しく低下します。 - 耐腐敗性
多くのバクテリアは中性付近で最も繁殖しやすく、アルカリ性が高い環境では活動が抑制されます。pHを適切に維持することは、腐敗を防ぐ上でも重要です。 - 皮膚への影響
pHが高すぎると、作業者の皮膚への刺激が強くなることがあります。
- 防錆性
- 適切な管理範囲
油剤の種類によって異なりますが、一般的にはpH 8.5~9.5の範囲が目安です。必ず使用している切削油のメーカー推奨値を確認してください。 - 測定方法
- pH試験紙
大まかなpHを手軽に確認できます。試験紙を液に浸し、色の変化を標準色と比較します。 - pHメーター(推奨)
より正確な測定が可能です。電極を液に浸して測定します。定期的な校正が必要です。
- pH試験紙
- 維持・調整方法
- 定期測定
週に1回程度、pHを測定し記録します。 - 低下時の対応
pHが低下傾向にある場合、まず原因を探ります(バクテリア繁殖、二酸化炭素の溶解、酸性物質の混入など)。根本原因への対策(殺菌処理、タンク清掃、換気改善など)が必要です。一時的な対策として、切削油メーカー推奨の**pH調整剤(アルカリ補充剤)**を少量ずつ添加してpHを回復させることも可能ですが、根本解決にはなりません。pH調整剤の過剰添加は油剤のバランスを崩す可能性があるので注意が必要です。 - pHが異常に高い場合
他のアルカリ性物質(洗浄剤など)の混入が疑われます。
- 定期測定
濃度管理:性能バランスの要
- 重要性
水溶性切削油の性能(潤滑性、冷却性、防錆性、耐腐敗性など)は、濃度によってバランスが大きく変わります。- 濃度が低すぎる場合
潤滑性、防錆性、耐腐敗性が低下し、加工不良、発錆、早期腐敗の原因となります。 - 濃度が高すぎる場合
冷却性が低下し、べたつきによる機械周りの汚れ、泡立ち、コスト増に繋がります。皮膚への刺激も強くなることがあります。
- 濃度が低すぎる場合
- 適切な管理範囲
切削油の種類、加工内容、被削材によって異なります。必ずメーカーの推奨濃度範囲を確認し、その範囲内に維持することが重要です。一般的な目安としては、エマルジョンタイプで5~10%、ソリュブルタイプで3~7%、シンセティックタイプで2~5%程度ですが、製品ごとに確認が必要です。 - 測定方法
- 屈折計(糖度計、Brix計)
最も一般的に使用されます。測定器のプリズム面に切削油を1~2滴垂らし、蓋をして覗き込み、明暗の境界線の目盛りを読み取ります。- 注意点
- 屈折率換算係数
屈折計の読み取り値(Brix%)は、実際の濃度とは異なる場合があります。メーカーが提供する換算係数(例:読み取り値 × 1.1 = 実際の濃度)を用いて濃度を算出します。 - 校正
測定前に蒸留水などでゼロ点校正を行います。 - 温度補正
温度変化で屈折率が変わるため、温度補正機能付きの屈折計を使用するか、測定時の液温を考慮します。 - 汚れの影響
混入油や微細な粒子が多いと、測定値が不正確になることがあります。
- 屈折率換算係数
- 注意点
- 滴定法
より正確な濃度測定方法ですが、試薬や器具が必要で手間がかかります。
- 屈折計(糖度計、Brix計)
- 調整方法
- 濃度が低い場合
メーカー推奨濃度の希釈液、または状況に応じて原液を補充します。補充する際は、全体の液量を考慮して計算し、少しずつ加えながら攪拌し、再度濃度を確認します。 - 濃度が高い場合
水分のみが蒸発して濃度が高くなることが多いです。この場合は、希釈水(できればイオン交換水など)を補充します。 - 自動希釈装置
水道水と原液を接続し、設定した濃度で自動的に希釈液を作成・供給する装置です。濃度管理の手間を大幅に削減し、常に安定した濃度を維持するのに役立ちます。
- 濃度が低い場合
異物管理:劣化とトラブルの元を断つ
- 主な異物とその影響
- 切りくず・砥粒
加工精度への悪影響(傷)、フィルターやポンプの詰まり、スラッジの主成分。 - 混入油(浮上油、漏出油)
摺動面油、作動油、防錆油などが混入したもの。切削油本来の性能(特に冷却性、洗浄性)を低下させ、バクテリアの栄養源となり腐敗を促進します。油煙の原因にもなります。 - 微生物(バクテリア・カビ)
切削油の成分を分解して劣化させ、pH低下、腐敗臭、スラッジ生成、フィルター詰まり、アレルギーなどの健康被害を引き起こします。 - その他のゴミ
ウエス片なども腐敗や性能低下の原因となります。
- 切りくず・砥粒
- 混入防止策
- 機械のシール・パッキン点検
油圧系や潤滑系からの作動油・潤滑油漏れを防ぎます。 - タンクカバーの使用
上部からのゴミや切りくずの落下を防ぎます。 - 作業者の教育
タンク内に異物を入れないよう注意喚起します。 - 前工程からの持ち込み防止
洗浄工程などで使用した洗浄剤などが混入しないように注意します。
- 機械のシール・パッキン点検
- 除去方法
- 切りくず
- フィルター
ペーパーフィルター、マグネットセパレーター、サイクロンセパレーターなどを機械やタンクの仕様に合わせて設置し、定期的にメンテナンスします。フィルターの目詰まりは流量低下やオーバーフローの原因となるため、こまめな清掃・交換が必要です。 - タンク清掃
定期的な清掃で、フィルターで除去しきれない微細な切りくずや沈殿物を除去します。
- フィルター
- 混入油
- オイルスキマー
タンク液面に浮上した油を回収する装置です。ベルト式、ディスク式、フロート式など様々なタイプがあります。連続運転またはタイマー運転で使用します。 - 遠心分離機
切削油と混入油の比重差を利用して分離除去します。比較的高価ですが、効果的に油分を除去できます。
- オイルスキマー
- 微生物
- 殺菌剤・防カビ剤の添加
バクテリアやカビの増殖を抑制します。切削油メーカーに相談し、適合する薬剤を適切な用法・用量で使用することが重要です。安易な使用や過剰添加は、耐性菌の発生や人体への影響、油剤性能の低下を招く可能性があるので注意が必要です。 - 耐腐敗性の高い切削油の使用
微生物が繁殖しにくい成分で構成された切削油を選ぶことが、根本的な対策として有効です。サンワケミカル株式会社でも、耐腐敗性を強化した製品をラインナップしています。 - タンク清掃
バクテリアの温床となるスラッジを除去することが重要です。
- 殺菌剤・防カビ剤の添加
- 切りくず
4. トラブルを未然に防ぐための予防策
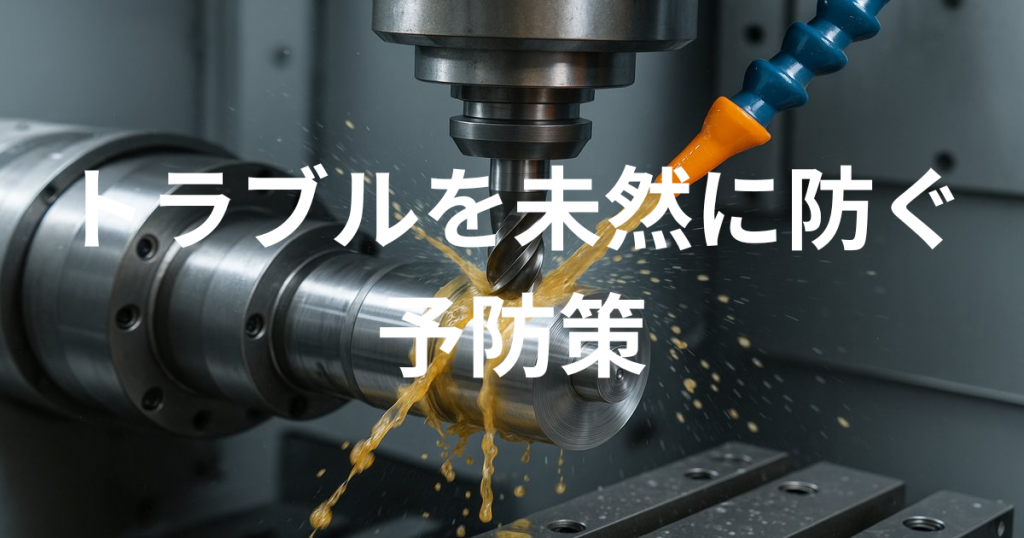
これまで述べてきた日常管理や定期メンテナンスを適切に行うことはもちろん重要ですが、それに加えて、トラブルの発生そのものを未然に防ぐための「予防策」を講じることも、切削油管理の重要な側面です。
適切な切削油の選定:すべての基本
トラブルを予防するための最も基本的かつ重要なステップは、使用する加工条件や環境に最適な切削油を選ぶことです。
- 加工条件との適合性
被削材の種類(鉄、アルミ、ステンレス、難削材など)、加工方法(旋削、フライス、研削、タップなど)、加工速度、使用する工具材質などを考慮し、必要な潤滑性、冷却性、極圧性、洗浄性などを満たす油剤を選定します。 - 耐腐敗性
バクテリアが繁殖しやすい環境(例:鋳物加工、油剤温度が上がりやすい、タンク清掃の頻度が低い)では、耐腐敗性に優れた油剤を選ぶことで、腐敗によるトラブルや交換頻度を大幅に減らすことができます。 - 消泡性
高圧クーラントを使用する場合や、空気の巻き込みが多い機械では、泡立ちにくい(消泡性に優れた)油剤を選ぶことが重要です。 - 防錆性
錆びやすい材質(鋳鉄など)を加工する場合や、湿度が高い環境では、防錆性能の高い油剤を選びます。 - 材質適合性
工作機械の塗装、シール材、非鉄金属(銅合金など)に対して影響の少ない油剤を選びます。 - 管理のしやすさ
濃度測定の容易さ、pHの安定性なども考慮に入れると良いでしょう。
最適な切削油の選定は、専門的な知識が必要です。現在の加工でトラブルが多い、どの油剤を選べばよいか分からないといった場合は、ぜひサンワケミカル株式会社にご相談ください。お客様の状況を詳しくお伺いし、最適な製品をご提案いたします。
機械のメンテナンス:切削油への影響を考慮
切削油の劣化や汚染は、切削油自体の問題だけでなく、使用している工作機械の状態にも大きく左右されます。
- 油漏れの防止
機械の摺動面や油圧系統からの作動油・潤滑油の漏れは、切削油への混入油の主な原因です。シールやパッキンの定期的な点検・交換を行い、油漏れを最小限に抑えることが重要です。 - クーラント供給系の点検
ポンプの性能低下や異音、配管の詰まりや漏れは、適切な切削油供給を妨げ、冷却・潤滑不足や泡立ちの原因となります。定期的に点検し、必要に応じて修理・清掃を行います。 - フィルター・分離装置の維持管理
フィルターの目詰まりや破損、オイルスキマーやマグネットセパレーターの不調は、異物除去能力を低下させ、切削油の汚染を加速させます。これらの装置が正常に機能しているか、定期的に確認し、メンテナンスを行うことが大切です。
機械自体のメンテナンスを怠ると、いくら切削油の管理を頑張っても、劣化を早めてしまう可能性があります。機械メーカーの推奨する点検・整備を定期的に実施しましょう。
作業者の意識向上:人的要因によるトラブルを防ぐ
切削油の管理は、設備やシステムだけでなく、それを使用する「人」の意識と行動も非常に重要です。
- 教育と情報共有
なぜ切削油管理が重要なのか、管理を怠るとどのような問題が発生するのかを作業者に理解してもらうための教育を行います。日常点検の方法や異常発見時の報告ルールなどを明確にし、周知徹底します。 - 異物混入の防止
- タンク内にウエスなどを絶対に捨てない、落とさないように指導します。
- 部品や工具をタンク内に落とした場合は、速やかに回収します。
- 適切な使用方法の遵守
- 勝手に水や原液を補充しない(必ず濃度を確認してから行う)。
- 他の液体(洗浄剤など)を混入させない。
- 異常の早期報告
「臭いがおかしい」「色が変だ」「泡が多い」など、些細なことでも異常に気づいたらすぐに報告する習慣をつけます。
作業者一人ひとりが切削油管理の重要性を理解し、ルールを守って作業することが、トラブルを未然に防ぎ、安定した生産を維持するために不可欠です。
5. 管理記録の重要性と活用方法
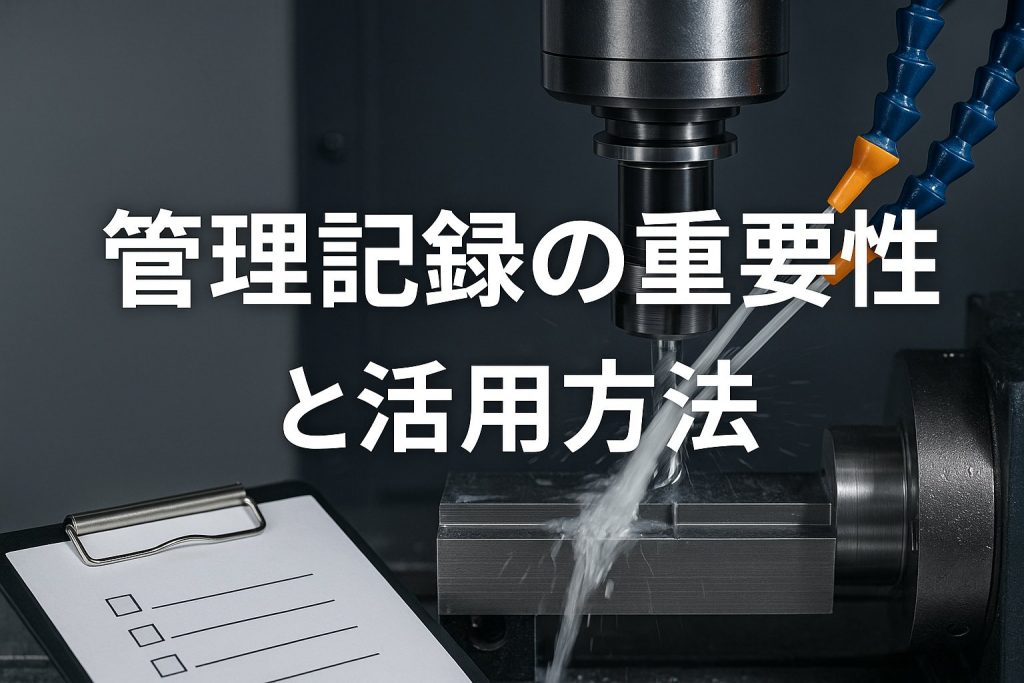
日々の点検や定期的なメンテナンス、品質管理の状況を記録に残すことは、効果的な切削油管理を行う上で非常に重要です。記録は、現状を正確に把握し、問題の原因究明や将来の改善に繋げるための貴重な財産となります。
なぜ管理記録が必要なのか? その目的とメリット
- 現状の正確な把握
日々の測定値(濃度、pHなど)や観察結果を記録することで、切削油の状態の変化を客観的に捉えることができます。「なんとなくいつもと違う」といった感覚的な判断だけでなく、数値に基づいた管理が可能になります。 - 問題発生時の原因究明
加工不良や腐敗などのトラブルが発生した際に、過去の記録(濃度やpHの推移、メンテナンス履歴など)を遡ることで、原因を特定する手がかりを得やすくなります。 - メンテナンス計画の最適化
記録データを分析することで、使用状況に応じた適切なタンク清掃や交換のタイミングを判断しやすくなり、無駄なメンテナンスや、逆にメンテナンス不足によるトラブルを防ぐことができます。 - 改善効果の測定
新しい切削油を導入したり、管理方法を変更したりした場合に、変更前後の記録を比較することで、その効果(寿命延長、品質安定化など)を定量的に評価できます。 - 担当者間の情報共有
担当者が複数いる場合や、担当者が変更になった場合でも、記録があれば切削油の管理状況をスムーズに引き継ぎ、一貫した管理を継続できます。 - コスト管理
切削油の使用量、補充量、交換頻度、廃液処理費用などを記録することで、切削油関連のコストを正確に把握し、コスト削減策の検討に役立てることができます。 - 環境・安全管理
廃液処理の記録などは、法令遵守の観点からも重要です。
記録すべき項目(具体例)
どのような項目を記録するかは、管理レベルや目的によって異なりますが、一般的に以下のような項目が挙げられます。
- 基本情報
- 記録日
- 対象機械名(またはクーラントタンク名)
- 担当者名
- 使用している切削油の製品名
- 日常点検結果
- 液面レベル(正常、低下、過多など)
- 外観(色、透明度、浮遊物、浮上油の有無・程度)
- 臭い(正常、腐敗臭、カビ臭など)
- 機械周りの漏れの有無
- 定期測定値
- 濃度(屈折計読み取り値と換算後の濃度)
- pH
- (必要に応じて)電気伝導度、液温、細菌数など
- 補充・調整記録
- 補充日
- 補充した種類(水、原液、希釈液)
- 補充量
- 補充後の濃度
- メンテナンス履歴
- タンク清掃実施日
- フィルター交換日
- 殺菌剤・防カビ剤・消泡剤などの添加日と添加量
- 交換記録
- 交換日
- 交換量
- 廃液処理方法・処理日
- トラブル記録
- トラブル発生日
- トラブル内容(加工不良、異臭、皮膚トラブルなど)
- 原因調査結果
- 対応内容とその結果
これらの項目を記録するフォーマット(チェックシートや管理台帳)を作成し、現場で記入しやすいように工夫しましょう。最近では、タブレット端末や専用の管理ソフトウェアを活用する企業も増えています。
管理記録の活用方法
記録は、ただ残すだけでは意味がありません。定期的に見返し、分析することで、管理レベルの向上に繋げることができます。
- 傾向分析
濃度やpHの測定値をグラフ化すると、変化の傾向(徐々に低下している、急激に変動したなど)が視覚的に分かり、異常の予兆を捉えやすくなります。 - トラブル原因の推定
トラブル発生時に、関連する記録(発生前の濃度変化、メンテナンス履歴など)を照らし合わせることで、原因の絞り込みに役立ちます。 - メンテナンス周期の最適化
過去の記録から、特定の機械や油剤での劣化速度やスラッジ蓄積のペースを把握し、画一的ではない、実態に合ったメンテナンス(清掃・交換)周期を設定できます。 - 油剤性能の比較
異なる種類の切削油を試した場合、それぞれの管理記録(寿命、トラブル発生頻度、補充量など)を比較することで、自社の加工や管理体制により適した油剤を客観的に評価できます。 - 改善活動の効果測定
管理方法の変更や改善策を実施した後、関連する記録データ(例:腐敗発生までの期間、濃度安定性)がどのように変化したかを確認し、改善活動の効果を評価します。
管理記録は、切削油管理におけるPDCAサイクル(Plan-Do-Check-Act)を回すための重要なツールです。ぜひ積極的に記録・活用し、継続的な改善に取り組んでください。
まとめ
本記事では、切削油を長持ちさせ、常に最適な状態で使用するための管理方法について、日常管理、定期的なメンテナンス(清掃・交換)、品質維持のポイント(pH、濃度、異物管理)、トラブルの予防策、そして管理記録の重要性と活用方法に至るまで、網羅的に解説しました。
日々の地道な点検と記録、定期的なタンク清掃と適切なタイミングでの交換、そしてpH・濃度・異物といった品質項目への注意を怠らないこと。これらの適切な管理を継続的に行うことで、切削油の寿命を最大限に延ばし、腐敗や性能低下によるトラブルを防ぎ、結果として安定した加工品質の維持、工具寿命の延長、そしてコスト削減に繋げることが可能です。
切削油管理は、決して難しいことばかりではありません。まずはできることから始め、日々の管理を習慣化することが大切です。この記事が、皆様の現場における切削油管理の改善の一助となれば幸いです。
サンワケミカル株式会社は、長年の経験と技術に基づき、多種多様な切削油剤を開発・製造しております。お客様の加工条件やニーズに合わせた最適な製品をご提案いたしますので、切削油に関するご相談は、ぜひお気軽にお問い合わせください。
もし、この記事で紹介した対策を試しても問題が解決しない場合や、お使いの切削油に関するより詳細な情報、お客様の特定の加工に最適な油剤の選定についてご相談がありましたら、どうぞお気軽に私たちサンワケミカル株式会社までお問い合わせください。経験豊富な専門スタッフが、お客様の状況を詳しくお伺いし、最適なソリューションをご提案いたします。
サンワケミカル株式会社HP:http://sanwachemical.co.jp/
サンワケミカル株式会社お問い合わせ:http://sanwachemical.co.jp/contact/
サンワケミカル株式会社公式X:https://x.com/sanwachemical
今後も、金属加工の現場で役立つ情報を発信してまいりますので、サンワケミカル株式会社公式ブログにご期待ください。