【切削油の長寿命化】切削油の寿命を2倍に!交換時期の判断と寿命を延ばすテクニック

機械加工の現場において、切削油の交換は定期的に発生するものの、そのタイミングや管理方法に頭を悩ませている担当者様は少なくないでしょう。「まだ使えるかもしれないのにもったいない」「交換時期がよく分からず、気づけば油剤がひどく劣化していた」といった声はよく耳にします。切削油の交換には、新しい油剤の購入費用はもちろんのこと、交換作業にかかる人件費、機械を停止させることによるダウンタイム、そして使用済み油剤の適正な廃液処理費用など、目に見えるコストと見えないコストの両方が発生します。
もし、これらの切削油の寿命を、現在の「2倍」に延ばすことができたら、どのようなメリットがあるでしょうか? これは、単に油剤関連の直接的なコストを大幅に削減できるだけでなく、産業廃棄物となる廃油の量を減らすことによる環境負荷の低減にも大きく貢献します。この記事では、切削油の寿命を最大限に引き出し、交換頻度を効果的に減らすための具体的な管理方法やメンテナンスのポイント、そして「いつ交換すべきか」という適切な交換時期の見極め方までを、網羅的かつ徹底的に解説していきます。日々の着実な取り組みを通じて、切削油の長寿命化、コスト削減、そして地球環境への貢献という、三方良しの実現を目指しましょう。
1. 切削油の寿命を左右する要因とは?

切削油がその「寿命を迎える」とは、具体的にどのような状態を指すのでしょうか。それは、切削油が本来持つべき重要な性能(潤滑作用、冷却作用、防錆作用、洗浄作用など)が著しく低下し、もはや加工に対して期待される役割を十分に果たせなくなった状態のことです。この寿命を縮めてしまう主な要因を正確に理解することが、効果的な長寿命化策を講じるための第一歩となります。
切削油寿命の様々な要因
- 不純物の混入と蓄積
これが劣化の最大の引き金 切削油は、使用しているうちに様々な種類の不純物が混入し、徐々に汚染されていきます。これらの不純物が、油剤の劣化を加速させる最大の原因となります。
- 切りくず、砥粒、機械の摩耗粉(固形異物)
これら加工中に発生する金属や砥石の微粒子は、クーラントタンク内に蓄積すると、フィルターの早期目詰まりを引き起こし、ポンプの摩耗や故障の原因となります。また、これらの粒子が加工点に再循環すると、加工面にスクラッチ傷をつけたり、工具の摩耗を不必要に促進させたりします。さらに重要なのは、これらの金属微粒子(特に銅や鉄など)が、切削油の酸化反応を促進する触媒として作用し、油剤の化学的な劣化を早めてしまうことです。 - 微生物(バクテリア、カビ、酵母)
空気中や希釈水、作業者の手などからクーラントタンクに混入した微生物は、切削油に含まれる有機成分(鉱物油、脂肪酸、一部の添加剤など)や、機械から漏れ出た混入油を栄養源として、適度な温度(一般的に20~40℃程度)と水分(特に水溶性切削油の場合)の条件下で急速に増殖します。微生物が増殖すると、(1)不快な腐敗臭(ドブのような臭い、硫化水素臭など)やカビ臭を発生させ作業環境を悪化させる、(2)代謝物として有機酸を生成し切削油のpHを低下させ、防錆性能を著しく損なう、(3)切削油の有効成分(乳化剤、防錆剤、潤滑剤など)を分解し性能を低下させる、(4)ネバネバした粘性物質(バイオフィルムやスライム)を形成しフィルターや配管を詰まらせる、といった深刻な問題を引き起こし、油剤を急速に使用不能な状態へと追いやります。 - 混入油(浮上油、トランプオイル)
工作機械の摺動面潤滑油、油圧作動油、スピンドルオイル、あるいは他の機械から飛散してきた油などが、シール不良やメンテナンス不足、開放されたタンクなどを通じてクーラントタンク内に漏れ出し混入します。これらの混入油は、切削油本来の性能(特に水溶性切削油の冷却性や洗浄性)を著しく低下させるだけでなく、微生物にとって格好の栄養源となり、その異常繁殖とそれに伴う腐敗を著しく促進します。また、液面に油膜を形成することで酸素の供給を遮断し、悪臭を放つ嫌気性菌の増殖を助長することもあります。 - その他の異物(ゴミ、ホコリなど)
工場内のホコリ、空気中の砂塵、機械の塗装片、シール材やホースの劣化による破片、作業者が誤って落としたタバコの吸い殻やウエス片なども、物理的な汚染源となり、フィルターの目詰まりや油剤性能の低下の原因となります。
- 切りくず、砥粒、機械の摩耗粉(固形異物)
- 不適切な日常の液管理
気づかぬうちに劣化を加速 日々の切削油の管理方法が不適切であると、上記のような不純物の影響をさらに増幅させ、劣化を早めてしまうことになります。
- 濃度管理の不良(水溶性切削油の場合)
- 濃度が低すぎる状態での継続使用
潤滑性能や冷却性能が不足するだけでなく、油剤中に配合されている防錆剤や殺菌剤・防腐剤の有効濃度も低下してしまいます。これにより、ワークや機械が錆びやすくなったり、微生物が非常に繁殖しやすい状態になったりして、油剤の寿命を著しく縮めます。 - 濃度が高すぎる状態での継続使用
泡立ちやすくなったり、機械周りがベタついたりするだけでなく、一部の添加剤成分が析出してスラッジ化したり、乳化安定性が損なわれたりするなど、性能バランスが崩れて劣化に繋がることがあります。また、単純に原液の無駄遣いにもなります。
- 濃度が低すぎる状態での継続使用
- pH管理の不良(水溶性切削油の場合)
切削油のpH値は、その防錆性能や耐腐敗性と密接に関連しています。水溶性切削油は通常、pH8.5~9.5程度の弱アルカリ性に調整されていますが、微生物の繁殖による酸性物質の生成や、空気中の二酸化炭素の溶解などにより、pHが徐々に低下していきます。pHがこの適正範囲から大きく外れ、特に酸性側に傾くと、防錆性能が著しく低下し、また微生物がさらに繁殖しやすい環境となってしまいます。 - 温度管理の不適切さ
- 高温状態での長時間運転
切削油の温度が高すぎる状態(例えば50℃以上)が長時間続くと、油剤の熱酸化劣化が急速に進行し、粘度上昇、スラッジ生成、添加剤の消耗などを引き起こします。また、微生物の活動も一般的に高温域(40℃近辺まで)で活発になります。 - 急激な温度変化の繰り返し
特に水溶性切削油の場合、急激な温度変化は乳化状態の安定性を損ない、油分の分離などを引き起こす可能性があります。また、低温環境下では一部の添加剤が析出しやすくなることもあります。
- 高温状態での長時間運転
- 濃度管理の不良(水溶性切削油の場合)
- 使用条件や機械側の要因も寿命に影響
上記以外にも、以下のような使用条件や機械側の要因も、切削油の寿命に影響を与えることを理解しておく必要があります。
- 被削材の種類と加工の難易度
例えば、鋳鉄の加工では非常に微細な黒鉛や鉄粉が多く発生しやすく、油剤が物理的に汚れやすい傾向があります。また、ステンレス鋼やチタン合金のような難削材の加工では、高い切削熱と大きな加工負荷がかかるため、油剤への熱的・化学的ストレスが大きくなります。 - 加工方法の種類と負荷
研削加工のように微細な砥粒やスラッジが大量に発生する加工や、高速・高負荷な切削を連続して行う場合は、油剤の汚染進行や劣化が早まる傾向にあります。 - 工作機械の状態とメンテナンス状況
機械の油圧系統や潤滑系統からの油漏れが多い、クーラントタンクのシールが不十分で外部からの汚染物質が混入しやすい、搭載されているフィルターの性能が低い、タンク容量が加工規模に対して小さすぎる、といった機械側の要因も、切削油の汚染を助長し、寿命を縮める原因となります。 - クーラントの供給状態と循環システム
クーラントの流量や圧力が不適切で、加工点での冷却や切りくず排出が十分に行われていない場合、局所的な高温状態や切りくずの滞留が油剤の劣化を間接的に促進することがあります。
- 被削材の種類と加工の難易度
これらの様々な要因が複雑に絡み合い、それぞれの現場で使用されている切削油の実際の寿命を決定づけています。
2. 切削油の交換時期の判断基準:見逃せないサイン

切削油の寿命を最大限に有効活用し、かつ加工トラブルを未然に防ぐためには、その「劣化のサイン」を見逃さず、適切なタイミングで交換することが極めて重要です。早すぎる交換は無駄なコストを生み、逆に遅すぎる交換は加工品質の低下、工具寿命の短縮、さらには機械の故障といったより深刻な問題を引き起こしかねません。以下に、交換時期を判断するための具体的な目安となるサインを挙げます。
五感で確認できる日常的な変化(日常点検の重要性)
日々の操業前点検や作業中の観察を通じて、以下のような切削油の見た目や臭いの変化に気づいたら、それは交換を検討すべき初期のサインかもしれません。
- 外観の明らかな変化
- 著しい変色
新品時や正常時の色調(例えば、乳白色、淡黄色透明、緑色透明など、油剤によって異なります)と比較して、色が明らかに濃く変色している(例えば、黒褐色、濃い茶色、灰色っぽくなっている)、あるいは通常とは異なる異常な色(例えば、鮮やかな緑色に変色したり、赤茶色に濁ったり)を呈している場合。これらは、油剤の酸化劣化の進行、異種油の大量混入、金属イオンの溶出による反応、あるいは特定の微生物の異常繁殖などを示唆しています。 - 著しい濁りや白濁の進行(特に透明または半透明タイプの場合)
油剤の乳化状態が破壊されている(油水分離)、微細な固形異物が大量に浮遊している、あるいは微生物が異常に増殖して液が濁っている可能性があります。エマルションタイプ(乳白色)の油剤であっても、油滴が凝集して分離し始めたり、異常な粘性が出たりしている場合は要注意です。 - 浮遊物や沈殿物の顕著な増加
クーラントタンクの液面や内部に、通常のフィルターでは除去しきれないほどの大量の切りくず、スラッジ(泥状の沈殿物)、カビのような膜状の浮遊物などが目視で容易に確認できる状態。これは、フィルターシステムの能力不足やメンテナンス不良、あるいはタンク内での汚染が著しく進行していることを示しています。 - 浮上油(混入油)の慢性的な多量存在
オイルスキマーなどで定期的に除去作業を行っているにもかかわらず、常にクーラントタンクの液面に厚い油膜(虹色に光る薄い膜ではなく、明らかに層をなしている状態)が形成されている場合。これは、工作機械からの作動油や潤滑油の漏れが深刻である可能性を示唆しており、切削油の性能を著しく低下させ、腐敗を急速に進行させます。
- 著しい変色
- 臭いの明らかな変化
- 我慢できないほどの強い腐敗臭
ドブのような不快な臭い、硫化水素臭(卵が腐ったような臭い)、アンモニア臭など、明らかに異常で刺激的な悪臭が作業場に漂っている場合。これは、嫌気性菌などの腐敗細菌がタンク内で大量に繁殖し、切削油が著しく腐敗している最も分かりやすいサインの一つです。このような状態では、作業者の健康への悪影響も懸念されます。 - カビ臭
カビ特有の土臭いような、あるいは埃っぽいような臭いがする場合。タンク内や配管内部でカビが繁殖している可能性があります。
- 我慢できないほどの強い腐敗臭
- 泡立ちの異常な状態
- 消えにくい持続的な泡が通常よりも多量に発生する
切削油に配合されている消泡剤の効果が失われていたり、油剤の成分バランスが劣化によって崩れていたり、あるいは特定の異物が混入して界面状態が変化していたりする可能性があります。過度な泡立ちは、冷却・潤HAL効果を著しく阻害し、加工不良の原因となります。
- 消えにくい持続的な泡が通常よりも多量に発生する
加工状態や結果に現れる性能低下のサイン
切削油の性能が低下してくると、それは加工結果や工具の状態にも明確な兆候として現れ始めます。
- 加工不良の頻発や悪化傾向
- 寸法精度の悪化やばらつきの増大
これまで安定して出ていた加工寸法が、許容範囲を外れることが多くなったり、加工品ごとの寸法のばらつきが大きくなったりした場合。これは、切削油の潤滑性や冷却性が低下し、加工中の熱変位や加工抵抗が不安定になっていることが原因と考えられます。 - 仕上げ面粗度の悪化
加工面のむしれ、引きずり傷、光沢不足、焼けなどが目立つようになった場合。油剤の潤滑性能の低下や、油剤中に増加した微細な異物が加工面を傷つけている可能性があります。
- 寸法精度の悪化やばらつきの増大
- 工具寿命の著しい低下
「最近になって急に工具の摩耗が早くなった」「以前よりも工具のチッピングや突発的な欠損が増えた」といった場合。切削油の潤滑性、冷却性、あるいは極圧性といった工具保護性能が、劣化により低下していることが強く疑われます。 - 切りくず処理性の明らかな悪化
切りくずが工具やワークに以前よりも絡みつきやすくなった、切りくずの分断性が悪くなり長く繋がるようになった、あるいは切りくずがクーラントの流れでスムーズに排出されにくくなったなど。これは、切削油の洗浄性や粘度が変化している可能性があります。
定期的な液管理データにおける異常値の継続
日常的な点検や、定期的に行う切削油の分析で得られる数値データも、交換時期を客観的に判断するための重要な手がかりとなります。
- 濃度(水溶性切削油)の管理不能状態
推奨濃度範囲を維持するために補給調整を行っても、すぐに濃度が大きく変動してしまい、安定した管理が困難になった場合。 - pH(水溶性切削油)の著しい低下と、調整しても回復しない状態
切削油のpHがメーカー推奨範囲(一般的には8.5~9.5程度)を大きく下回り(例えば7.5以下など)、pH調整剤を添加しても一時的にしか回復しない、あるいは全く回復の兆しが見られない場合。これは、タンク内のバクテリアによる有機酸の生成が非常に活発で、油剤の緩衝能力(pHを一定に保つ能力)を完全に超えてしまっている状態を示唆しており、腐敗が末期的な段階にあると考えられます。 - 細菌数・真菌(カビ)数の異常な増加と抑制不能
定期的な微生物検査(例えば、ディップスライド法など)で、管理基準値を大幅に超える細菌数や真菌数が検出され、殺菌剤や防カビ剤の添加といった対策を講じても、その効果が一時的で、すぐに再び異常なレベルまで増殖してしまう場合。 - その他の専門的な分析値の著しい悪化
切削油メーカー(サンワケミカルなど)に定期的な油剤分析を依頼している場合、例えば全酸価(油剤の酸化劣化の指標)、腐食性試験の結果、潤滑性評価試験(ファレックス試験、シェル四球試験など)の結果などが、メーカーが定める交換推奨基準値を大幅に超えて悪化している場合。
これらのサインは、単独で現れることもあれば、複数が同時に現れることもあります。「これくらいならまだ大丈夫だろう」と安易に判断せず、これらのサインを総合的に評価し、加工品質への影響、機械への負担、そして作業環境への配慮といった観点から、適切な交換時期を判断することが重要です。判断に迷う場合は、早めに切削油メーカーに相談し、専門家のアドバイスを求めることをお勧めします。
3. 切削油の寿命を2倍に延ばすための日常管理
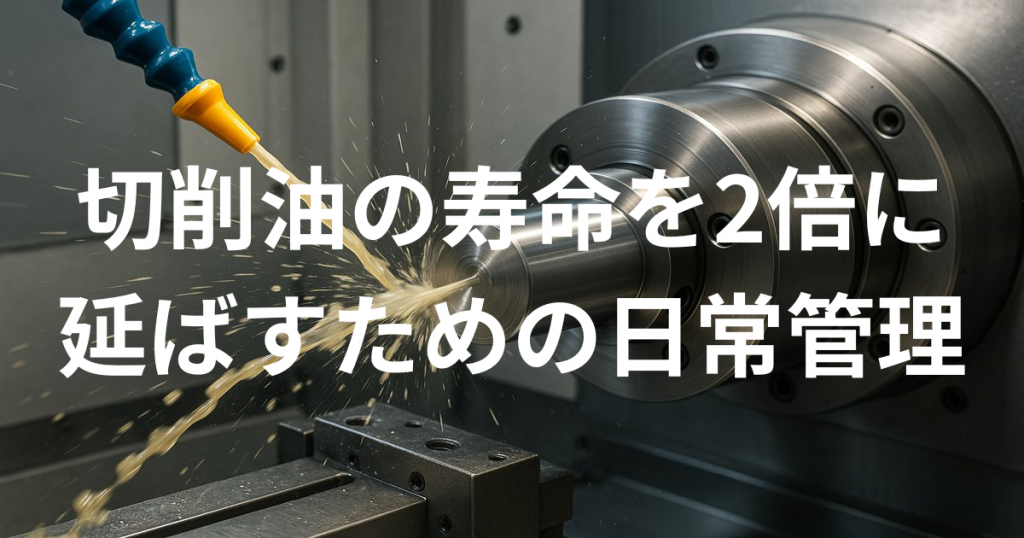
切削油の寿命を延ばし、「2倍」という目標を達成するためには、特別な高価な装置を導入したり、複雑な技術を駆使したりすることだけが全てではありません。むしろ、日々の地道な基本的な管理作業を「徹底して」行うことこそが、最も確実で効果的な長寿命化への道筋となります。ここでは、その具体的な日常管理のポイントを改めて確認しましょう。
適切な濃度管理の徹底(水溶性切削油):品質維持の生命線
- なぜ重要か再確認
繰り返しになりますが、水溶性切削油の「濃度」は、その油剤が持つべき潤滑性、冷却性、防錆性、耐腐敗性といった全ての基本性能のバランスを決定づける最も重要な管理項目です。濃度がメーカー推奨範囲から外れた状態で使用を続けることは、性能不足による加工トラブルを引き起こすだけでなく、油剤の早期劣化を招き、寿命を著しく縮める最大の要因となります。 - 具体的な実践方法
- 定期的な濃度測定の習慣化
最低でも週に1回、理想的には毎日始業前に、校正された屈折計(Brix計)を使用して濃度を測定します。測定時には、必ず使用している切削油の換算係数(ファクター)を用いて、Brix値から実際の濃度(%)に正しく換算することが重要です。 - 正確な記録と変動傾向の把握
測定した濃度値は、日付とともに必ず記録し、その変動傾向(上昇傾向か、低下傾向か、安定しているか)を把握します。これにより、補充のタイミングや量の予測、あるいは異常の早期発見に繋がります。 - 適切な補充作業の実施
- 濃度が低い場合
メーカー推奨濃度になるように、原液またはあらかじめ濃いめに調整した希釈液を補充します。補充する際は、現在のタンク液量と濃度、目標濃度から必要な補充量を計算し、少量ずつ攪拌しながら加え、再度濃度を確認するという手順を丁寧に行います。 - 濃度が高い場合(主に水分蒸発による)
清浄な希釈水(できればイオン交換水や純水)を補充して調整します。
- 濃度が低い場合
- 自動濃度管理(希釈)装置の活用検討
特にクーラントの使用量が多い工場や、厳密な濃度管理が求められる場合には、自動で濃度を監視し、原液や水を補給する装置の導入も有効です。初期投資はかかりますが、長期的に見れば、管理の手間削減、原液の無駄遣い防止、そして常に安定した濃度維持による油剤寿命の延長効果が期待できます。
- 定期的な濃度測定の習慣化
適切なpH管理の徹底(水溶性切削油):腐敗と錆を防ぐ砦
- なぜ重要か再確認
水溶性切削油のpH値は、主に防錆性能と耐腐敗性に大きく関わっています。多くの水溶性切削油は、pHを8.5~9.5程度の弱アルカリ性に保つことで、鉄系金属の錆を防ぎ、またバクテリアなどの微生物の活動を抑制するように設計されています。pHがこの適正範囲から低下すると、これらの重要な性能が著しく損なわれます。 - 具体的な実践方法
- 定期的なpH測定の習慣化
週に1回程度を目安に、pH試験紙またはより正確なpHメーターを使用して測定し、記録します。 - 適正pH範囲の維持
使用している切削油のメーカーが推奨するpH範囲を確実に維持します。 - pH低下時の原因究明と対策
pHが低下傾向を示した場合、その原因を特定することが重要です。主な原因としては、(1)バクテリアの増殖による有機酸の生成、(2)空気中の二酸化炭素の溶解、(3)他の酸性物質の混入などが考えられます。根本的な原因への対策(例えば、タンク内のスラッジ除去、浮上油の除去、殺菌処理の検討など)をまず行い、その上でpH調整剤(アルカリビルダー)の使用を検討します。pH調整剤の使用は、必ずメーカーに相談し、推奨される製品を適切な用法・用量で、慎重に行う必要があります。安易な添加は、油剤の成分バランスを崩す可能性があるためです。
- 定期的なpH測定の習慣化
異物混入を防ぐための作業者の意識向上と具体的な対策の実践
「切削油タンクはゴミ箱ではない」という基本的な意識を、作業現場の全員が共有し、実践することが、異物による油剤汚染を防ぐ上で非常に重要です。
- 作業者への教育・啓発
異物(切りくず、機械油、ゴミ、食品カスなど)が切削油に混入すると、どのような悪影響(油剤劣化、機械トラブル、加工不良)があるのかを具体的に教育し、混入防止の重要性を理解してもらいます。 - 具体的な混入防止対策
- クーラントタンクへのカバー設置
機械の停止時や非稼働時には、クーラントタンクの開口部にカバーをかけ、上方からのホコリ、ゴミ、落下物などの侵入を物理的に防ぎます。 - 機械周辺の清掃(5S活動の徹底)
工作機械の周辺やクーラントタンクの周りを常に清潔に保ち、床に落ちた切りくずやゴミが風や人の移動によってタンク内に混入する機会を減らします。 - 作業場内での飲食ルールの徹底
機械周辺での飲食を原則禁止とし、食品カスや飲料の残りなどがタンクに混入するのを防ぎます。 - 適切なウエスや工具の管理
使用済みのウエスや、点検・調整に使用した工具類をタンク内に誤って落とさないように、置き場所などをルール化し、注意喚起します。 - 混入油(浮上油)対策の徹底
工作機械の油圧系統や潤滑系統からの作動油・潤滑油の漏れは、発見次第速やかに修理します。タンクに浮上した油は、オイルスキマーなどを用いてこまめに除去します(詳細は次項で解説)。
- クーラントタンクへのカバー設置
定期的な液面レベルのチェックと適切な補充作業の実施
- なぜ重要か
クーラントタンク内の液量が規定レベルよりも少ない状態で運転を続けると、(1)全体の液量が少ないため油剤の温度が上昇しやすく、熱劣化を早める、(2)汚れや劣化成分が濃縮されやすい、(3)ポンプが空気を吸い込みやすくなり、泡立ちやキャビテーション(ポンプ損傷)の原因となる、といった問題が発生します。 - 具体的な実践方法
毎日始業前などに液面計やゲージで液面レベルを確認し、規定の範囲内に維持するように補充を行います。補充する際は、前述の濃度管理を必ず行い、適切な濃度の液を補充するようにします。水の蒸発が多い場合は清浄な水を、液全体の持ち出しが多い場合は調整済みの希釈液を補充するのが基本です。
これらの日常管理は、一見地味で手間がかかるように感じるかもしれませんが、その効果は絶大です。まさに「塵も積もれば山となる」の言葉通り、日々の小さな積み重ねが、切削油の寿命を大幅に延ばし、結果として大きなコスト削減と環境負荷低減に繋がるのです。
4. 切削油の定期的なメンテナンスと延命対策
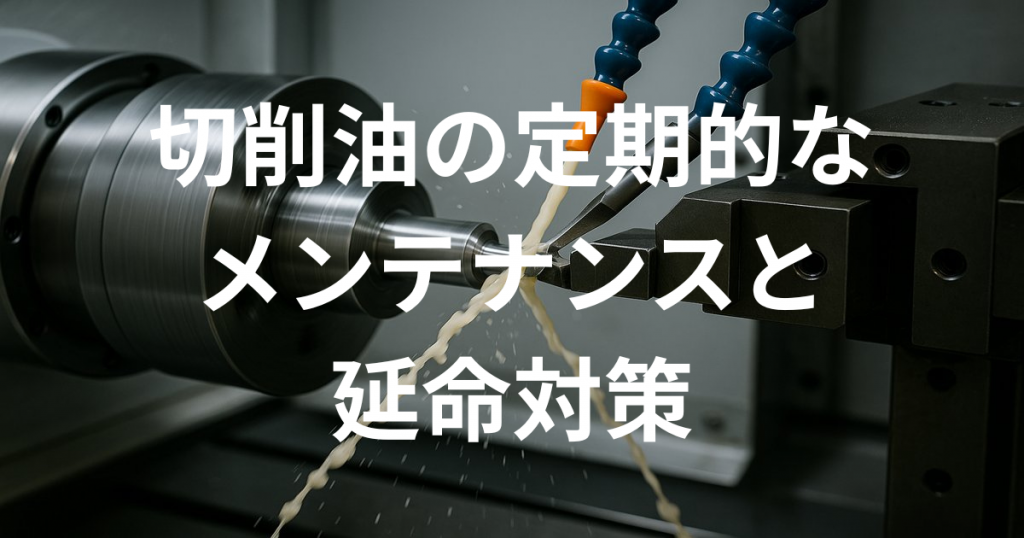
日々のきめ細やかな管理に加えて、計画的かつ定期的なメンテナンスと、より積極的な延命対策を講じることで、切削油の寿命をさらに飛躍的に延ばすことが可能です。これらは、いわば切削油の健康診断と治療にあたるものであり、問題が深刻化する前に対処するための重要な手段となります。
フィルターの定期的な交換や清掃:油剤の血液をきれいに保つ
- その重要性
切削油循環システムに設置されたフィルターは、油剤中に混入する固形異物(切りくず、砥粒、機械の摩耗粉、外部からのゴミなど)を除去し、油剤の清浄度を維持するための最重要防衛ラインです。フィルターが目詰まりした状態で使用を続けると、(1)異物除去能力が著しく低下し油剤の汚染が急速に進行する、(2)クーラントの流量が低下し加工点への供給不足による冷却・潤滑不良を招く、(3)フィルターエレメントが破損し捕捉した異物が下流へ再流出する、といった深刻な問題を引き起こします。 - 具体的な手順と適切な頻度
- 差圧管理による交換・清掃時期の判断(推奨)
多くのフィルターシステムには、フィルターの入口側と出口側の圧力差(差圧)を測定する差圧計や差圧スイッチが設置されています。この差圧が、あらかじめ設定された上限値(フィルターメーカーの推奨値や、過去の運用経験から設定した値)に達したら、フィルターが目詰まりしていると判断し、速やかに交換または清掃を行います。これが最も合理的で確実なメンテナンス時期の判断方法です。 - 定期的なスケジュールに基づく交換・清掃
差圧管理が難しい場合や、より予防的な観点からは、過去の運用実績やメーカーの推奨に基づき、「〇ヶ月ごと」「機械の〇〇時間運転ごと」といった形で、定期的な交換・清掃スケジュールを設定し、実施します。ただし、加工負荷の変動などにより最適なタイミングとずれが生じる可能性もあるため、あくまで目安として、可能であれば差圧管理と併用するのが理想的です。 - フィルターの種類に応じた対応
- カートリッジフィルター、バッグフィルター
これらは基本的に消耗品であり、目詰まりしたら新しいものと交換します。 - ストレーナー、一部のメッシュフィルター
網やエレメントを取り外し、付着した異物を洗浄することで再利用可能なタイプもあります。 - マグネットセパレーター
磁石に吸着した鉄系の切りくずや摩耗粉を、定期的に手動または自動で掻き取り、除去・清掃します。
- カートリッジフィルター、バッグフィルター
- 差圧管理による交換・清掃時期の判断(推奨)
クーラントタンクの徹底的な清掃:悪玉菌の巣窟をリセットする
これらの定期的なメンテナンスと積極的な延命対策は、確かに初期投資や一定の手間・時間を要するものもあります。しかし、それによって得られる切削油の寿命延長効果、そしてそれに伴うトータルコストの削減効果は、多くの場合、その投資や手間を十分に上回るものとなるはずです。
- その重要性
日常のフィルター管理だけでは除去しきれない微細なスラッジ(油、金属粉、微生物の死骸などが混じり合った泥状の沈殿物)や、タンクの壁面・底面、配管内部などに形成されたバイオフィルム(微生物が分泌する粘性物質で形成された膜)は、まさに微生物の温床(巣窟)となります。これらを放置すると、いくら新しい切削油を補充しても、すぐに微生物が再繁殖し、悪臭の発生、pHの低下、油剤の急速な腐敗といった問題が繰り返されることになります。定期的なタンク清掃は、これらの汚染源を物理的にリセットし、新しい切削油が長持ちするためのクリーンな環境を作り出すために不可欠です。 - 具体的な手順と適切な頻度
- 清掃頻度の目安
一般的には、半年に1回から1年に1回程度が目安とされますが、これはあくまで一般的な数値です。実際の頻度は、使用している切削油の種類(耐腐敗性)、機械の使用状況、微生物の汚染度合い、フィルターシステムの性能などによって大きく異なります。日常点検でタンク内の汚れ具合(スラッジの堆積量、壁面のぬめりなど)を観察し、汚れが目立つようであれば早めに計画・実施することが重要です。 - 清掃手順の例
- 古い切削油の抜き取り
ポンプやドレンから、タンク内の古い切削油を完全に抜き取ります。抜き取った廃液は、法令に従い適切に処理します。(詳細は別記事「切削油の廃棄方法」をご参照ください) - タンク内の固形物・スラッジの物理的除去
タンク内に残った大きな切りくずや、底に溜まったヘドロ状のスラッジを、ヘラ、ブラシ、専用のバキュームクリーナーなどを使って、できる限り物理的に除去します。 - タンク内壁および付属部品の洗浄・殺菌(推奨)
汚れや微生物の汚染がひどい場合は、切削油メーカー推奨のタンククリーナー(システムクリーナー)を使用します。これらは多くの場合、洗浄剤と殺菌剤・防カビ剤が一体となった製品です。タンククリーナーを規定の濃度で水に希釈し、タンクに入れて数時間から一昼夜程度循環させた後、その洗浄液を抜き取ります。(注意:タンククリーナーの使用方法、循環時間、廃液処理方法については、必ず製品の取扱説明書やメーカーの指示に従ってください。) - 徹底的なすすぎ洗い
洗浄剤や殺菌剤の成分がタンク内に残留すると、新しい切削油の性能に悪影響を与える可能性があるため、洗浄後はきれいな水でタンク内を十分すぎるほど念入りにすすぎ洗いします。 - 乾燥と新液の準備・注入
タンク内を乾燥させた後、新しい切削油をメーカー推奨の正しい手順と濃度で希釈・調整し、タンクに注入します。
- 古い切削油の抜き取り
- 清掃頻度の目安
オイルスキマーや遠心分離機などの導入による不純物除去能力の強化
日常管理で浮上油の除去が追いつかない場合や、微細な異物による汚染が著しい場合には、これらの専用装置の導入が効果的です。
- オイルスキマー
クーラントタンクの液面に浮上した混入油(機械の潤滑油や作動油など)を、ベルト式、ディスク式、フロート式などのメカニズムで連続的または間欠的に回収・除去する装置です。混入油は微生物の主要な栄養源であり、また切削油本来の性能を低下させるため、その効果的な除去は油剤の寿命延長と性能維持に大きく貢献します。 - 遠心分離機(クーラントセパレーター、サイクロンセパレーター)
遠心力を利用して、切削油よりも比重の重い微細な固形粒子(微細な切りくず、砥粒、スラッジなど)を効率的に分離・除去します。フィルターでは捕捉しきれないμmオーダーの微粒子除去にも効果があり、特に研削加工や鋳物加工などで発生するスラッジ除去に有効です。フィルターの負荷軽減にも繋がり、より高いレベルでの清浄度維持が可能になります。
殺菌剤や防腐剤の適切な使用による微生物の抑制(専門家相談の上で)
- その目的と位置づけ: バクテリアやカビといった微生物の異常な繁殖が確認され、それが悪臭やpH低下、油剤劣化の直接的な原因となっている場合に、その増殖を抑制し、油剤の延命を図るために使用されます。
- 極めて重要な注意点
殺菌剤や防腐剤の使用は、あくまで対症療法的な手段であり、前述したタンク清掃や浮上油除去、適切な濃度・pH管理といった根本的な汚染源対策や予防管理と必ず併用する必要があります。薬剤だけに頼った管理は、効果が一時的であったり、耐性菌を発生させたり、あるいは油剤の成分バランスを崩して別のトラブルを引き起こしたりするリスクがあります。 薬剤の選定(使用している切削油との適合性、対象となる微生物の種類など)、添加する量、添加するタイミングや頻度については、必ず事前に切削油メーカー(サンワケミカルなど)に相談し、専門家のアドバイスと指示のもとで、適切な製品を正しい用法・用量で使用してください。 安易な自己判断での購入や使用は、絶対に避けるべきです。
5. 切削油の長寿命化によるコストメリットと環境負荷低減
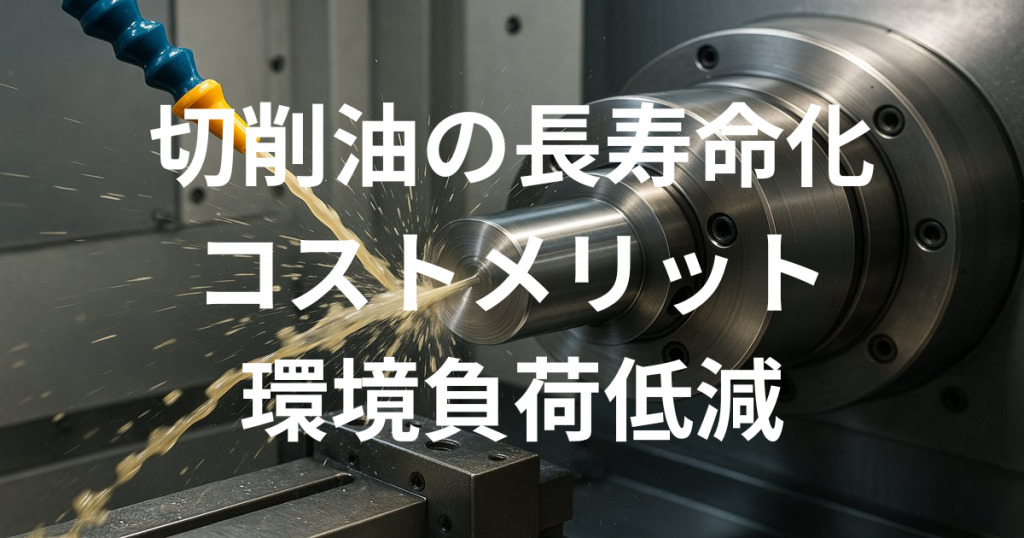
切削油の寿命を延ばすための日々の努力と計画的なメンテナンスは、単に「交換の手間が少し減る」というレベルの話ではありません。それは、企業の収益性向上と、地球環境保護という、現代企業にとって不可避な二つの大きなテーマに直接的に貢献する、非常に意義深い取り組みなのです。
目に見える直接的なコスト削減効果
切削油の寿命が延び、交換頻度が例えば半分になれば、以下のような直接的なコストが大幅に削減されます。
- 切削油(新油)購入費用の大幅な削減
最も分かりやすいメリットです。年間の切削油の購入量が減るため、その分の費用がそのまま利益改善に繋がります。特に、複数の工作機械で大量の切削油を使用している工場にとっては、その削減効果は莫大なものになる可能性があります。 - 廃液処理費用の劇的な削減
使用済み切削油(廃油)は、産業廃棄物として法律に基づいた適正な処理が義務付けられており、その処理には専門業者への委託費用が発生します。交換回数が減れば、排出される廃油の量も当然減少し、高額になりがちなこの廃液処理費用を大幅に抑制できます。 - 交換作業にかかる人件費・工数および機械ダウンタイムの削減
切削油の交換作業には、(1)古い油剤の抜き取り、(2)タンク内の徹底的な清掃、(3)新しい油剤の希釈・調整と注入、そして(4)交換後の試運転と調整といった一連の工程があり、これには多くの作業時間と人手が必要です。さらに、その間は工作機械を停止させる必要があるため、生産機会の損失(ダウンタイム)も発生します。切削油の寿命が延びれば、これらの交換作業にかかる直接的な人件費や工数、そして間接的な機会損失コストを大幅に削減でき、その分のリソースを他のより生産的な業務に振り向けることが可能になります。
目に見えにくい間接的なコスト削減効果(品質向上・トラブル減少による)
さらに、常に良好な状態で管理された長寿命の切削油を使用し続けることは、以下のような間接的なコスト削減効果ももたらします。
- 工具寿命の延長による工具費と交換手間の削減
適切な性能を維持した切削油は、工具の摩耗を効果的に抑制します。これにより、高価な切削工具の交換頻度が減り、工具費そのものの削減と、工具交換作業にかかる手間や時間の削減に繋がります。 - 加工不良率の低減による不良品コストと手直し工数の削減
安定した潤滑性能や冷却性能は、寸法精度や面粗度の安定化に貢献し、加工不良の発生率を低減させます。これにより、不良品の廃棄コストや、手直し作業にかかる人件費・時間を削減できます。 - 機械トラブルの減少によるメンテナンス費用と突発的な生産停止リスクの低減
清浄で適切な状態に保たれた切削油は、クーラントポンプの摩耗や故障、フィルターの異常な早期目詰まり、配管の詰まりといった機械トラブルの発生リスクを低減させます。これにより、突発的な機械修理にかかる費用や、それに伴う生産ラインの停止といった大きな損失を防ぐことができます。
これらのコストメリットを具体的に数値化して試算し、長寿命化への取り組みがもたらす経済的な効果を社内で共有することは、さらなる改善活動へのモチベーション向上にも繋がります。
環境負荷低減への確かな貢献
切削油の長寿命化は、企業の経済活動におけるコスト削減という直接的なメリットだけでなく、地球環境の保全という、より大きな視点からも非常に重要な貢献を果たします。
- 産業廃棄物(廃油)の排出量削減
これが最も直接的で分かりやすい環境貢献です。切削油の交換頻度が減ることで、産業廃棄物として処理される廃油の量が物理的に削減されます。これにより、最終処分場の逼迫問題の緩和や、万が一の不適切な処理による環境汚染リスクそのものを低減することに繋がります。 - 限りある石油資源の有効活用
多くの切削油の基油(ベースオイル)は、原油から精製される鉱物油です。切削油の使用量を減らし、その寿命を延ばすことは、有限である石油資源の消費量を抑制し、その有効活用に貢献します。 - CO2(二酸化炭素)排出量の削減(間接的な効果)
新しい切削油を製造するプロセス、工場へ輸送するプロセス、そして使用済みの廃油を収集・運搬し、焼却などの処理を行うプロセスでは、それぞれエネルギーが消費され、CO2が排出されます。切削油の寿命を延ばし、交換サイクルを長くすることは、これらのプロセス全体の活動量を減らすことになり、結果としてCO2排出量の削減にも間接的に貢献します。
企業の持続可能な生産活動(サステナビリティ)への貢献
近年、環境問題(Environment)、社会(Social)、企業統治(Governance)を重視する「ESG経営」や、国連が提唱する「持続可能な開発目標(SDGs)」への関心が世界的に高まっています。このような背景の中、企業が事業活動において環境負荷の低減に積極的に取り組むことは、単なる法令遵守や社会貢献という枠を超え、企業価値そのものを高め、投資家や消費者からの信頼を得て、長期的な成長を確実にするための重要な経営戦略と位置づけられています。 切削油の長寿命化という具体的な取り組みは、まさにこの「経済的なメリットの追求」と「環境負荷の低減」という二つの目標を同時に達成できる、実践的かつ効果的なアクションプランの一つです。それは、企業の持続可能な生産活動を支え、より良い未来を築くための確かな一歩となるでしょう。
サンワケミカル株式会社では、単に高性能な切削油製品を提供するだけでなく、お客様の工場における切削油の管理状況を詳細に分析し、具体的な長寿命化策をご提案することで、コスト削減と環境負荷低減の両立を積極的にサポートさせていただいております。「うちの工場でももっと寿命を延ばせるだろうか?」「具体的なメリットを試算してみたい」といったご要望がございましたら、ぜひお気軽にご相談ください。
まとめ
本記事では、切削油の寿命を最大限に延ばし、交換頻度を効果的に減らすための具体的な管理方法やメンテナンスのポイント、そしてその交換時期を見極めるための判断基準について、多角的に詳しく解説してまいりました。「寿命を2倍に」という目標も、決して夢物語ではなく、日々の着実な取り組みによって十分に達成可能なものであることをご理解いただけたかと思います。
切削油の寿命は、日常的な濃度管理やpH管理の徹底、異物混入の防止といった基本的な「日常管理」の質に大きく左右されます。さらに、フィルターの定期的な交換や清掃、クーラントタンクの計画的な清掃、そしてオイルスキマーや遠心分離機といった専用装置の活用を含む「定期的なメンテナンスと延命対策」を組み合わせることで、その効果を飛躍的に高めることができます。 そして、交換時期の判断においては、日々の点検で気づく外観や臭いの変化、加工状態の悪化といった現場での「生きた情報」と、濃度やpH、微生物数といった「客観的なデータ」の両方から総合的に見極めることが重要です。
これらの適切な管理とメンテナンスを着実に実践することは、単に切削油の寿命を延ばすという直接的な効果だけでなく、切削油の購入費用や高額な廃液処理費用の大幅な削減、工具寿命の延長による工具費の削減、加工品質の安定化による不良品コストの低減、そして機械のダウンタイム削減による生産性の向上といった、多くの経済的なメリットをもたらします。 さらに、産業廃棄物となる廃油の排出量を削減することで、限りある資源の有効活用と地球環境負荷の低減にも大きく貢献できる、企業にとって非常に意義のある取り組みです。
ぜひ、本記事でご紹介した内容を日々の現場管理にお役立ていただき、コスト削減と環境負荷低減を両立させる、より効率的で持続可能な生産活動を実現してください。
サンワケミカル株式会社は、長年の経験と技術に基づき、多種多様な切削油剤を開発・製造しております。お客様の加工条件やニーズに合わせた最適な製品をご提案いたしますので、切削油に関するご相談は、ぜひお気軽にお問い合わせください。
もし、この記事で紹介した対策を試しても問題が解決しない場合や、お使いの切削油に関するより詳細な情報、お客様の特定の加工に最適な油剤の選定についてご相談がありましたら、どうぞお気軽に私たちサンワケミカル株式会社までお問い合わせください。経験豊富な専門スタッフが、お客様の状況を詳しくお伺いし、最適なソリューションをご提案いたします。
サンワケミカル株式会社HP:http://sanwachemical.co.jp/
サンワケミカル株式会社お問い合わせ:http://sanwachemical.co.jp/contact/
サンワケミカル株式会社公式X:https://x.com/sanwachemical
今後も、金属加工の現場で役立つ情報を発信してまいりますので、サンワケミカル株式会社公式ブログにご期待ください。