【自動運転における切削油管理】無人化加工を安定させるためのトラブル防止策
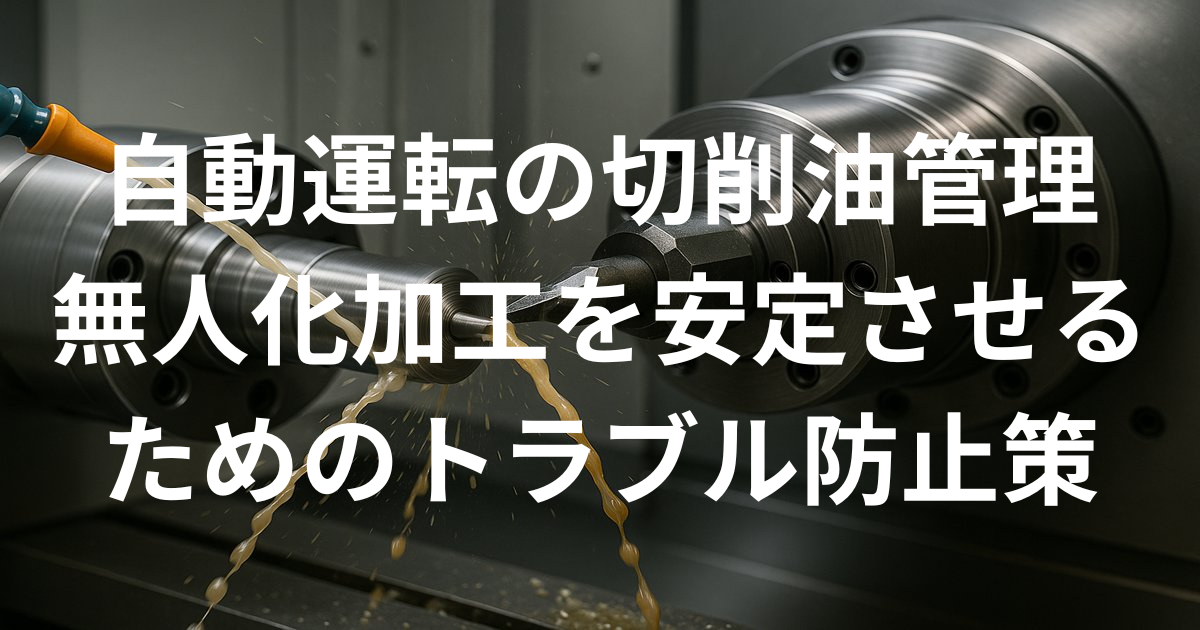
労働力不足への対応、生産性の飛躍的な向上、そして24時間体制での稼働実現へ。マシニングセンタやCNC旋盤における「自動運転」「無人化加工」は、現代の金属加工業が競争力を維持し、発展していくための不可欠なトレンドとなっています。ロボットによるワークの自動着脱、夜間や休日を利用した長時間の連続運転は、もはや特別な光景ではありません。しかし、その華々しい自動化の裏側で、見落としてはならない重要な「要」が存在します。それが切削油の管理です。
「夜間運転中にクーラントが漏れて、朝来たら工場が水浸しになっていた」「無人加工中にタップが折れ、後続のワークが全て不良品になってしまった」「気づかぬうちに切削油が腐敗し、機械全体が錆びてしまった」…これらは、自動運転の現場で実際に起こりうる、そして一度起これば甚大な被害に繋がりかねない深刻なトラブルです。
この記事では、無人化・自動化された加工を、安全かつ安定して継続させるための「切削油管理」に徹底的に焦点を当てます。自動運転特有のリスクから始まり、そのリスクを回避するための自動管理システム、異常検知機能の活用、そして長期連続運転を支える油剤の品質維持、さらにはリモートでの監視体制に至るまで、無人化加工を成功に導くためのトラブル防止策を網羅的に解説いたします。
1. 自動運転加工における切削油管理の重要性と課題
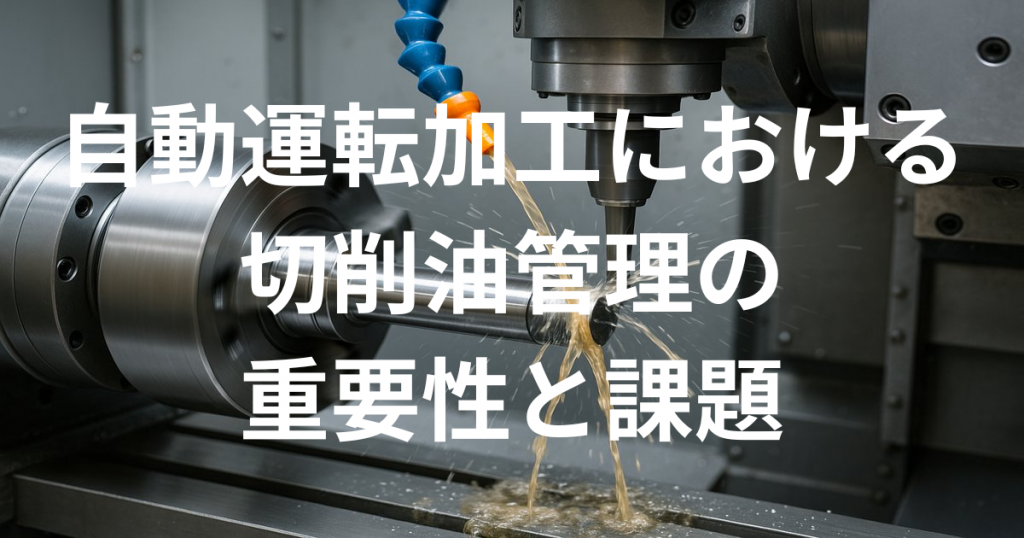
自動運転加工における切削油管理の核心は、「作業者がいない」という前提に立ち、トラブルの「未然防止」と「早期自律検知」の体制を構築することです。人の目と手による即時対応が期待できないため、切削油の異常は放置され、生産停止や機械故障といった甚大な被害に直結するリスクを常に内包しています。
通常の有人運転であれば、作業者が異音、異臭、加工面の変化、クーラントの異常な減り具合といった「いつもと違う」変化に気づき、機械を停止させたり、上司に報告したりといった初期対応が可能です。しかし、作業者が常駐しない自動運転、特に夜間や休日の無人運転においては、この「人間の五感による監視」と「迅速な判断・対応」というセーフティネットが存在しません。
なぜリスクが格段に高まるのか
発見の遅れが被害を拡大させる
自動運転中に切削油に関連するトラブル、例えばクーラントの供給停止、液漏れ、大幅な濃度異常、フィルターの完全目詰まり、急激な腐敗などが発生しても、それを検知する仕組みがなければ、次に誰かが確認するまで問題は放置され続けます。
- クーラント供給停止
ドライ状態で加工が続き、工具の焼付き、折損、ワークの不良、最悪の場合は火災に至る可能性があります。 - 液漏れ
大量の切削油が床に流出し、環境汚染や清掃コストの増大、転倒事故のリスクを生みます。 - 濃度低下
防錆性能が失われ、長時間にわたり機械やワークが錆の脅威にさらされます。 - 切りくず詰まり
排出されなかった切りくずが原因で工具が折損し、それに気づかずに後続のワークも次々と不良品として加工されてしまいます。
予兆なき突然の停止
切削油の状態は、時間をかけて徐々に劣化・汚染されていきます。有人運転であれば、その過程での微細な変化に気づき、予防的な対策を講じることができます。しかし、自動運転では、これらの予兆が見過ごされ、ある日突然、許容限界を超えて重大なトラブルとして表面化し、生産ライン全体を長時間停止させてしまうリスクが高まります。
なぜ高度な管理が不可欠なのか
これらのリスクを回避し、無人運転を「ただ動かす」だけでなく、「安定して動かし続ける」ためには、従来の切削油管理のレベルを一段も二段も引き上げる必要があります。具体的には、
- 人に代わって状態を監視する「センサー」
- 異常を検知し、知らせ、行動する「システム」
- そもそも劣化しにくく、トラブルを起こしにくい「高性能な切削油」
- 自動化システムを支える「計画的なメンテナンス」 といった、より高度で自律的な管理体制の構築が不可欠となるのです。
まとめると、自動運転加工における切削油管理は、単なる品質維持活動ではなく、生産ライン全体の安定稼働と無人化の成否を左右する、極めて重要なリスクマネジメントの一環なのです。
2. 無人運転に対応した切削油の自動管理システム
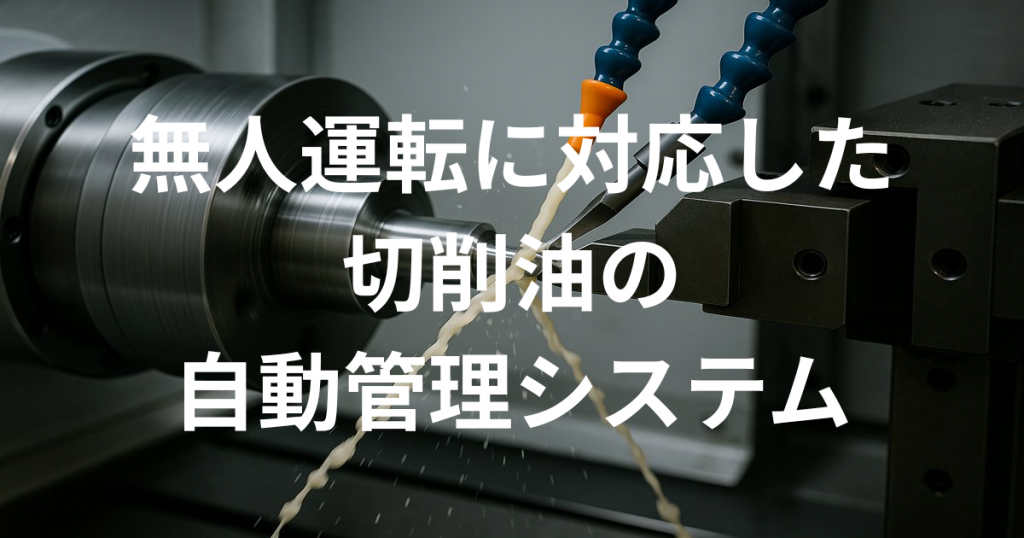
無人運転を支える切削油管理の基本は、これまで人手に頼ってきた濃度・pH・液量の管理を「自動化」することです。各種自動管理装置や集中管理システムを導入することで、省力化と同時に、人為的ミスを排除した高レベルな品質安定化を実現します。
作業者が常駐しない環境で、切削油のコンディションを常に最適に保つためには、人に代わって管理を行うシステムが必要不可欠です。ここでは、その代表的なシステムを紹介します。
自動濃度管理装置(自動希釈供給装置)
仕組みと効果
水溶性切削油の濃度をセンサー(例:屈折率センサー、導電率センサーなど)で常時監視し、設定された管理範囲から逸脱した場合に、自動で原液または希釈水を補給して濃度を一定に保つ装置です。
- 省力化
面倒な手作業による濃度測定と補充作業から解放されます。 - 品質安定化
水分の蒸発による濃度上昇や、持ち出しによる濃度低下を自動で補正し、常に最適な濃度を維持することで、潤滑性、冷却性、防錆性といった基本性能を安定させ、加工品質のばらつきを防ぎます。 - 油剤の長寿命化
適切な濃度が維持されることで、耐腐敗性も保たれ、油剤の早期劣化を防ぎます。 - コスト削減
原液の無駄な投入を防ぎ、油剤コストを最適化します。
自動pH調整装置
仕組みと効果
pHセンサーで液のpH値を常時監視し、設定された下限値を下回った場合に、pH調整剤(アルカリビルダー)を自動で少量ずつ添加し、pH値を適正範囲に回復させる装置です。
- 腐敗と錆の防止
pH値を弱アルカリ性に保つことで、バクテリアの活動を抑制し、防錆性能を維持します。これにより、油剤の腐敗による悪臭の発生や、機械・ワークの錆を防ぎます。 - 注意点
あくまで対症療法的な側面が強く、pHが低下する根本原因(微生物の繁殖、スラッジの蓄積など)への対策と併用することが重要です。
自動給油・液面管理装置
仕組みと効果
クーラントタンク内の液面レベルを液面センサーで常時監視し、下限レベルに達した場合に、あらかじめ調整された希釈液を自動で補給するシステムです。
- ポンプ保護と安定供給
液面低下によるポンプのエア吸い込み(キャビテーション)や、それに伴う供給圧力・流量の不安定化を防ぎ、常に安定したクーラント供給を実現します。 - トラブル防止
液漏れなどによる急激な液面低下を早期に検知するきっかけにもなります。
集中管理システム(セントラルクーラントシステム)
仕組みと効果
工場内の複数の工作機械で使用する切削油を、個々の機械のタンクで管理するのではなく、一箇所に設置された大型の集中タンクと高度な浄化・管理装置で一元的に管理し、各機械へ配管を通じて供給・循環させるシステムです。
- 究極の管理効率化
濃度、pH、温度、清浄度といったすべての管理を、一箇所で集中的かつ高度に行うことができます。 - 品質の高度な安定化
大容量タンクで管理するため、液の性状変化が緩やかで、常に高品質な切削油を安定して供給できます。 - メンテナンスの効率化
フィルター交換やタンク清掃といったメンテナンス作業を集約でき、工数を大幅に削減できます。 - コスト削減
油剤の長寿命化、購入・廃液処理の一元化によるコストメリットが期待できます。 - 導入の検討
大規模な設備投資が必要となるため、工場の規模やレイアウト、使用する油剤の種類などを総合的に考慮して、導入を検討します。
これらの自動管理システムは、無人運転下での切削油のコンディションを常に最適に保つための基盤技術です。省力化だけでなく、品質の安定化とトラブルの未然防止に大きく貢献します。
3. 異常発生時の自動検知とアラート機能
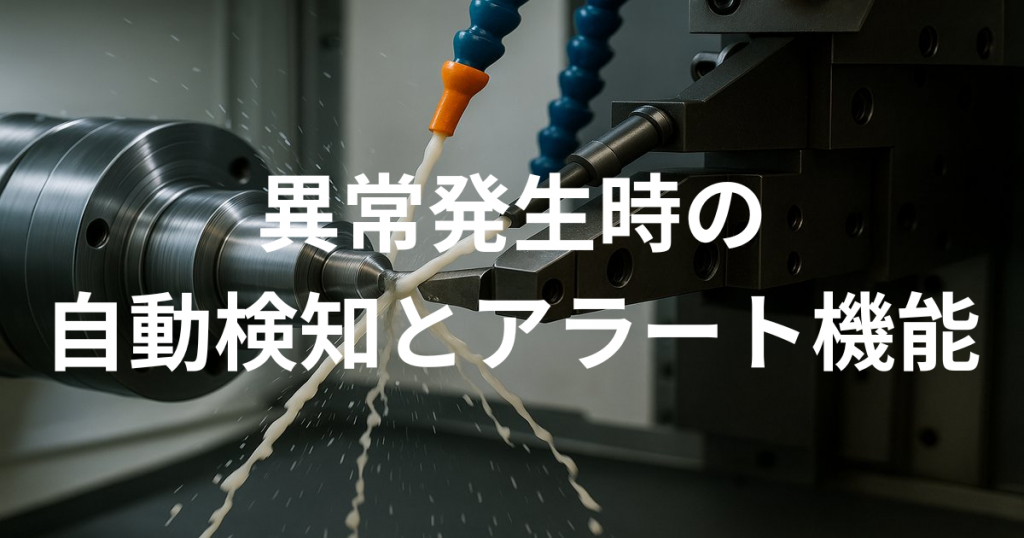
自動運転における安全管理の核心は、万が一の異常をシステムが自ら「検知」し、人間に「通知(アラート)」し、そして被害拡大を防ぐために自ら「停止」するという自律的な機能の実装です。これが、無人運転時の致命的な損害を防ぐための最後の砦となります。
どれほど優れた自動管理システムを導入しても、予期せぬトラブルが発生する可能性はゼロではありません。重要なのは、その異常をいかに早く検知し、いかに被害を最小限に食い止めるかです。
異常発生を自動で検知するセンサー技術
監視すべき主な項目
人の五感に代わり、各種センサーが24時間体制で切削油とその周辺システムを監視します。
- 濃度異常
屈折率センサー、導電率センサー、超音波センサーなどで、設定範囲からの逸脱を検知。 - pH異常
pHセンサーで、急激な低下(腐敗の兆候)などを検知。 - 液面低下
液面レベルセンサーで、急激な液量減少(漏洩の可能性)や下限レベル到達を検知。 - 温度異常
温度センサーで、液温の異常な上昇(冷却装置の不調など)や低下(冬季のヒーター不調など)を検知。 - ポンプ異常
流量センサー、圧力センサー、モーターの電流センサーなどで、ポンプの吐出量低下、圧力異常、過負荷(詰まりの兆候)などを検知。 - フィルター差圧異常
フィルターの入口と出口の圧力差を測定する差圧センサーで、フィルターの目詰まりを検知。
アラート機能と自動停止機能(インターロック)の重要性
アラート(警報)機能
検知した異常を、即座に人間に知らせる機能です。
- 通知方法
工場内のパトライト(積層信号灯)や警報ブザーを鳴らす、管理室の監視PCにポップアップ表示する、担当者のスマートフォンやタブレットにEメールやメッセージを送信するなど、多様な方法があります。 - 重要性
異常の発生をリアルタイムで把握し、迅速な対応を可能にするための第一歩です。
自動停止機能(インターロック)
特定のアラートが発生した際に、二次被害を防ぐために、関連する機器やマシニングセンタ本体の運転を安全に自動停止させる機能です。これは、無人運転における最も重要な安全機能と言えます。
- 設定例
- クーラント液面が下限値を下回った場合
ポンプを停止させ、焼き付きを防ぐ。 - クーラント供給圧力が異常低下した場合
機械の運転を停止させ、ドライ加工による工具破損や火災を防ぐ。 - フィルター差圧が上限値に達した場合
ポンプを停止させるか、機械に警告を出し、運転継続の可否を判断させる。
- クーラント液面が下限値を下回った場合
- 必須性
このインターロック機構がなければ、異常が発生しても機械は運転を続けてしまい、工具、ワーク、そして機械本体に甚大なダメージを与えかねません。導入するシステムには、確実にこの安全機能が組み込まれていることを確認し、また定期的にその機能が正常に作動するかをテストすることが不可欠です。
自動運転加工では、異常の自動検知とアラート、そして安全な自動停止機能は、単なる便利機能ではなく、高価な機械設備と生産計画を守るための必須の安全装置と位置づけるべきです。
4. 長期連続運転を支える切削油の品質維持
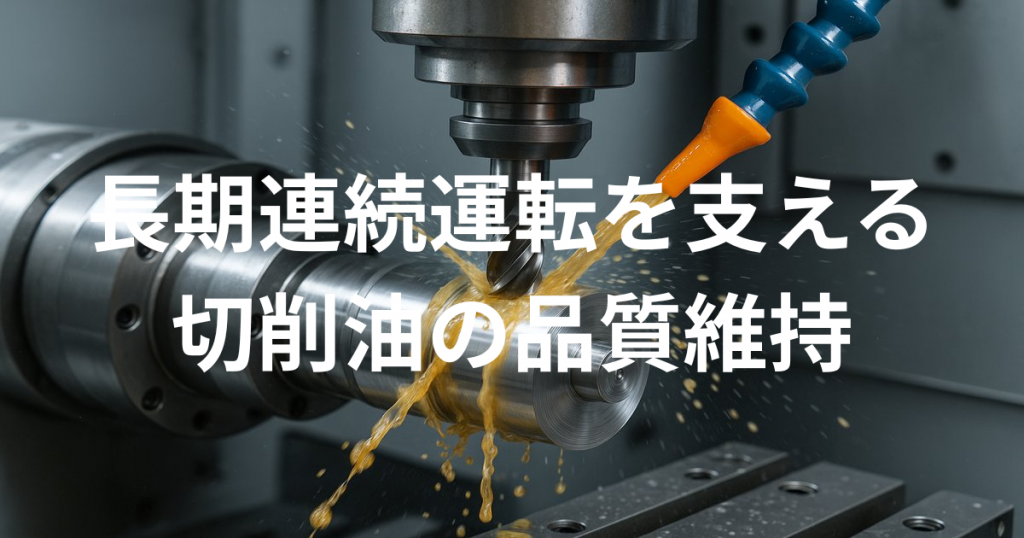
24時間365日の長期連続運転を安定して乗り切るためには、切削油の「劣化」と「汚染」の進行を極限まで抑制することが不可欠です。これには、高性能な浄化装置を導入して外部・内部からの汚染要因を徹底的に排除する「守りの管理」と、そもそも劣化しにくい「長寿命タイプの切削油」を選定するという「攻めの選定」、この二つのアプローチが鍵となります。
無人運転を長時間継続するためには、切削油自体のコンディションが、その間ずっと高いレベルで維持されなければなりません。そのための具体的な対策を紹介します。
高性能フィルターの導入による徹底した清浄度維持
なぜ重要か
長時間運転中は、切りくずや摩耗粉が絶え間なく発生し、油剤中に蓄積していきます。これが加工品質の低下や機械トラブルの原因となるため、連続的かつ効率的な除去が必要です。
対策
- 長時間運転対応フィルター
捕捉容量が大きく、メンテナンスインターバルの長いフィルターシステム(例:自動逆洗機能付きフィルター、大容量カートリッジフィルターなど)を選定します。 - 多段ろ過システム
粗い粒子を除去するマグネットセパレーターなどと、微細な粒子を除去する精密フィルターを組み合わせることで、効率的に高い清浄度を維持し、メインフィルターの寿命を延ばします。
定期的な殺菌処理による微生物コントロール
なぜ重要か
自動運転中は、タンク内の液温が微生物の繁殖に適した温度に保たれやすく、気づかぬうちに腐敗が進行することがあります。
対策
- 計画的な殺菌剤・防カビ剤の添加
定期的な微生物検査(ディップスライドなど)の結果に基づき、繁殖が確認された場合に、計画的に適切な薬剤を添加します。これにより、腐敗の進行を抑制し、pHの安定化にも繋がります。ただし、薬剤の選定と使用方法は、必ず切削油メーカーに相談の上、適切に行う必要があります。
異物除去の徹底(特に混入油対策)
なぜ重要か
機械からの潤滑油や作動油の漏れ(混入油)は、切削油の性能を低下させ、微生物の栄養源となり、腐敗を加速させる最大の要因の一つです。
対策
- オイルスキマーの連続運転
浮上油を除去するオイルスキマーを、タイマーなどで定期的に、あるいは連続的に作動させ、混入油がタンク内に長時間滞留しないようにします。 - 機械のメンテナンス
シール部品の点検・交換などを計画的に行い、そもそも油が漏れにくい状態を維持します。
長寿命タイプの切削油の選定
なぜ重要か
これまでの対策は「劣化を防ぐ」アプローチですが、そもそも「劣化しにくい」油剤を選ぶことも非常に重要です。
選定ポイント
- 優れた耐腐敗性
微生物の増殖を抑制する効果の高い殺菌剤・防カビ剤が配合されているか、あるいは微生物が利用しにくい成分で構成されている製品を選びます。 - 高い酸化安定性
長時間運転による熱負荷に耐え、酸化劣化しにくいベースオイルや酸化防止剤が使用されている製品を選びます。 - 実績と信頼性
長期間にわたる安定稼働の実績が豊富な油剤を選ぶことも、重要な判断材料です。
サンワケミカルでは、このような長期連続運転や自動化ラインの厳しい要求に応えるべく開発された、高性能な長寿命タイプの切削油を各種ラインナップしております。お客様の運転状況に最適な製品をご提案することで、安定生産とコスト削減に貢献します。
長期連続運転を支えるには、高性能フィルターや殺菌処理といった「守りの管理」と、長寿命タイプの油剤を選ぶという「攻めの選定」を組み合わせることが、切削油の品質を長期間維持するための最も効果的な戦略です。
5. 定期的なメンテナンスと遠隔監視の重要性
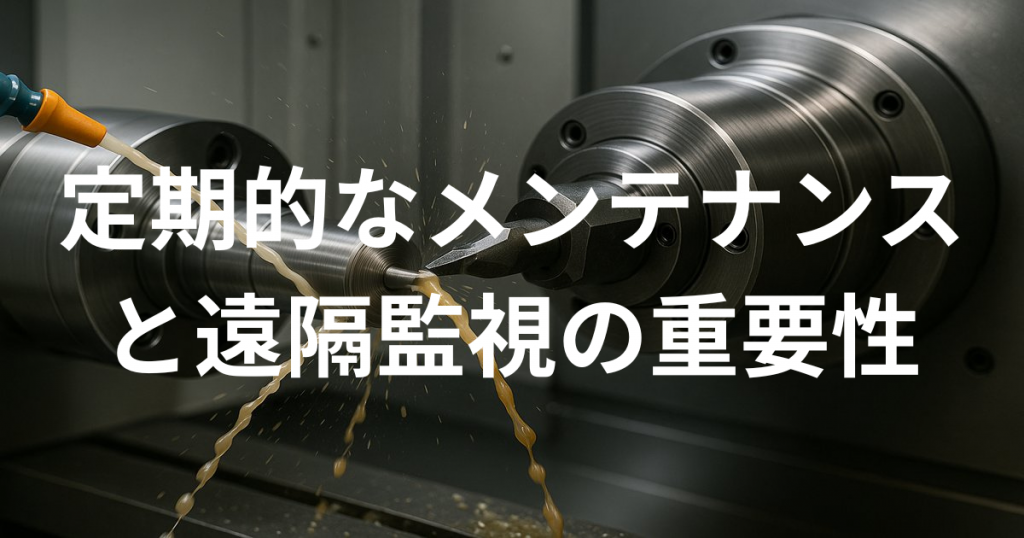
究極の自動化システムを構築したとしても、定期的な「人的メンテナンス」と、データを活用した「遠隔監視」を省略することはできません。 これらは、自動化システムの信頼性を担保し、予期せぬトラブルを未然に防ぎ、そしてシステム全体の継続的な改善を促すために不可欠な活動です。
自動化システムは万能ではありません。その性能を維持し、真に信頼できるものにするためには、人間の知見と経験に基づいた関与が依然として重要です。
自動管理システムに頼るだけでなく、定期的な人的点検とメンテナンスの必要性
なぜ人の目が必要か
- センサーでは検知できない異常の発見
センサーは設定された項目しか監視できません。例えば、通常とは異なる種類の浮遊物、タンク壁面のぬめり(バイオフィルムの兆候)、微細な配管からの滲み、ポンプの異音といった「五感で感じる異常の予兆」は、熟練した人間の目や耳でしか発見できないことがあります。 - センサー自体の点検・校正
センサーも経時的に劣化したり、汚れたりして、その指示値が不正確になることがあります。定期的に手動での測定値と比較し、必要に応じて清掃や校正、交換を行う必要があります。 - 物理的なメンテナンス
フィルターエレメントの交換、タンクの徹底的な清掃、ポンプのオーバーホールといった物理的なメンテナンスは、システムだけでは完結しません。これらを計画的に実施することが、システム全体の長寿命化に繋がります。
データと現場の照合
遠隔監視システムから得られるデータと、実際の現場での観察結果を定期的に照らし合わせることで、「データ上は正常だが、現場では異変が起きている」といったシステムの限界や改善点を発見することができます。
遠隔地から切削油の状態を監視できるシステムの導入と活用
遠隔監視システムのメリット
- リアルタイムでの状態把握
スマートフォンやタブレット、オフィスのPCなど、工場から離れた場所にいても、切削油管理システムの稼働状況(濃度、温度、液面、アラート履歴など)をリアルタイムで確認できます。 - 迅速な初動対応
夜間や休日にアラートが発生した場合でも、まず遠隔から状況を確認し、緊急性の高さを判断したり、現場に向かう担当者に具体的な指示を出したりすることが可能になります。 - データ蓄積と傾向分析
長期間の運転データを蓄積・分析することで、油剤の劣化傾向や、特定の時期にトラブルが発生しやすいといったパターンを把握し、より精度の高い予防保全計画の立案に役立てることができます。
成功する自動運転加工は、優れた自動化システムと、それを賢く使いこなし、維持管理する人間の知見との最適な融合によって成り立っています。遠隔監視と定期的な人的チェックはその最良の実践例です。
まとめ
本記事では、省人化・自動化が進む現代の機械加工現場において、その安定した生産を根幹から支える「自動運転加工における切削油管理」の重要なポイントについて、多角的な視点から詳しく解説してまいりました。
無人化された環境下では、切削油の管理は単なる液管理業務ではなく、生産ライン全体の稼働率と安全性を左右する極めて重要なリスクマネジメントとなります。その核心は、
- 自動管理システム(濃度、pH、液面)を導入し、人為的ミスを排除しつつ、常に油剤のコンディションを最適に保つこと。
- センサーによる異常検知とアラート、そして自動停止機能を確実に実装し、万が一のトラブル被害を最小限に食い止めること。
- 長寿命タイプの切削油の選定や、高性能な浄化装置の活用により、長期連続運転に耐えうる品質を維持すること。
- そして、これら自動化システムを過信せず、定期的な人的メンテナンスと遠隔監視によって、システムの信頼性を担保し、継続的な改善を図っていくこと。 にあります。
これらの対策を戦略的に組み合わせ、自社の運用に合わせた最適な管理体制を構築することで、無人運転時に発生しがちな切削油関連のトラブルを未然に防ぎ、マシニングセンタが持つ本来の生産性を最大限に引き出すことが可能となります。
もし、貴社の自動化ラインにおける切削油管理の高度化や、現在発生しているトラブルの解決、あるいはこれから導入する自動化システムに最適な切削油の選定などでお困りのことがございましたら、ぜひ一度、私たちサンワケミカル株式会社にご相談ください。長年の経験と豊富な実績に基づき、お客様の安定生産と効率向上に貢献する、トータルなソリューションをご提案させていただきます。
サンワケミカル株式会社は、長年の経験と技術に基づき、多種多様な切削油剤を開発・製造しております。お客様の加工条件やニーズに合わせた最適な製品をご提案いたしますので、切削油に関するご相談は、ぜひお気軽にお問い合わせください。
もし、この記事で紹介した対策を試しても問題が解決しない場合や、お使いの切削油に関するより詳細な情報、お客様の特定の加工に最適な油剤の選定についてご相談がありましたら、どうぞお気軽に私たちサンワケミカル株式会社までお問い合わせください。経験豊富な専門スタッフが、お客様の状況を詳しくお伺いし、最適なソリューションをご提案いたします。
サンワケミカル株式会社HP:http://sanwachemical.co.jp/
サンワケミカル株式会社お問い合わせ:http://sanwachemical.co.jp/contact/
サンワケミカル株式会社公式X:https://x.com/sanwachemical
今後も、金属加工の現場で役立つ情報を発信してまいりますので、サンワケミカル株式会社公式ブログにご期待ください。