【経費削減】切削油コストを30%カット!経費を効果的に削減し無駄をなくす管理・運用術

工場の運営において、コスト削減は常に重要な経営課題です。様々な経費の中で、意外と見過ごされがちなのが「切削油」にかかるコストではないでしょうか。「切削油なんて、加工に必要なものだから仕方ない」「コスト削減と言っても、具体的に何をすればいいか分からない」…そう考えている現場担当者や管理者の方も多いかもしれません。
しかし、切削油にかかるコストは、購入費用だけではありません。交換や補充の手間、廃液処理費用、そして不適切な管理による加工不良や工具寿命の低下といった「間接的なコスト」も含めると、決して無視できない金額になります。裏を返せば、切削油の管理・運用方法を見直すことで、大幅なコスト削減を実現できる可能性があるのです。
この記事では、「切削油コストを30%カット!」という高い目標を掲げ、その達成に向けた具体的な方法を多角的に解説します。日々の運用改善から、適切な製品選び、管理体制の効率化まで、無駄を徹底的に排除し、経費削減に繋げるための実践的なヒントが満載です。もちろん、30%という数字はあくまで目標値であり、削減効果は工場の状況によって異なりますが、本記事で紹介する方法を一つでも実践することで、着実なコストダウンが期待できるはずです。
1. 切削油の消費量を減らすための運用方法
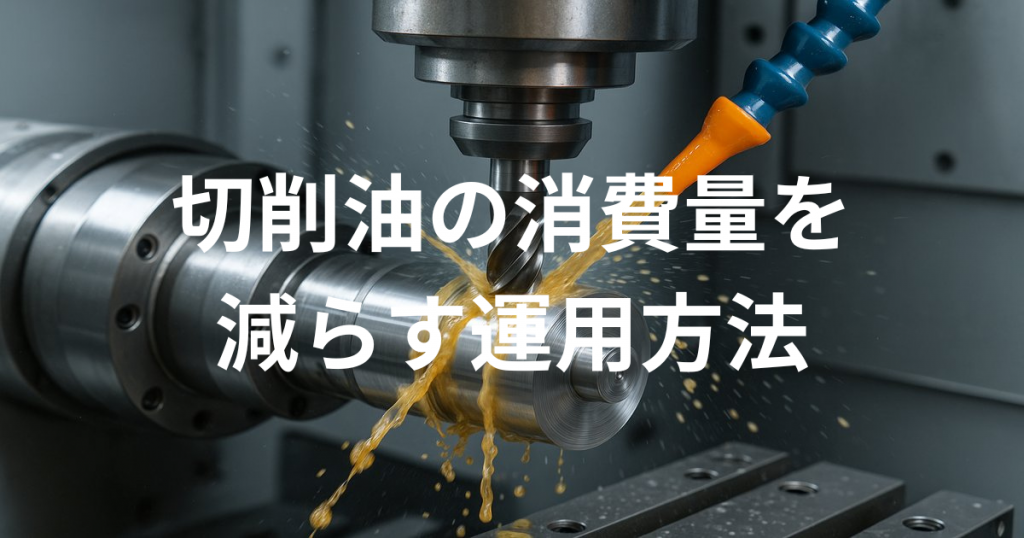
まず取り組むべきは、日々の切削油の「消費量」そのものを減らすことです。無駄な使用や損失をなくすための具体的な運用改善策を見ていきましょう。
1. 適正濃度の厳守と無駄な補充の削減
水溶性切削油の濃度管理は、品質維持だけでなくコスト削減にも直結します。
- 適正濃度の厳守
- 濃度が低い場合
性能不足を補うために、必要以上に頻繁な補充や早めの交換が必要になり、結果的に消費量が増加します。また、防錆力低下による機械・ワークの錆や、耐腐敗性低下による早期交換は、追加コストを発生させます。 - 濃度が高い場合
必要以上の原液を使用することになり、単純に購入コストが増加します。また、ベタつきによる清掃の手間や、泡立ちによるトラブル対応も間接的なコスト増に繋がります。 - 対策
必ずメーカー推奨の濃度範囲を守り、定期的な濃度測定と正確な補充(水または原液/希釈液)を行うことが基本です。
- 濃度が低い場合
- 自動濃度管理装置の導入
- 手作業による濃度測定・補充は、手間がかかるだけでなく、担当者によるバラつきやヒューマンエラーが発生しやすい側面があります。自動濃度管理装置は、センサーで濃度を常時監視し、必要に応じて水や原液を自動で供給するため、常に最適な濃度を維持できます。
- メリット
無駄な原液消費の削減、補充作業の省力化、濃度安定による品質向上・油剤寿命延長。 - デメリット
初期導入コストがかかります。しかし、長期的な原液削減効果や省力化効果を考慮すると、特に使用量の多い工場では十分に投資回収が見込める場合があります。費用対効果を試算し、導入を検討する価値はあります。
2. クーラント液の飛散防止対策
加工中に飛散するクーラントミストや飛沫は、油剤の損失だけでなく、作業環境の悪化や清掃コストの増加にも繋がります。
- カバーの設置
工作機械の加工エリア開口部や、クーラントタンクに適切なカバーを設置することで、外部への飛散を物理的に抑制します。特に高速加工や高圧クーラントを使用する場合は効果的です。 - 適切なノズル調整
- 流量・圧力の最適化
必要以上に高い圧力や流量で供給すると、飛散量が増加します。加工内容に合わせて、必要最小限の流量・圧力に調整します。 - ノズルの向き・形状
加工点に的確にクーラントが当たるように、ノズルの向きや角度を調整します。シャワーノズルやフラットノズルなど、飛散しにくい形状のノズルを選ぶことも有効です。
- 流量・圧力の最適化
- 高圧クーラントの適正使用
深穴加工や難削材加工には有効ですが、飛散量も多くなります。本当に必要な場合に限定して使用するなど、運用を見直します。
3. 持ち出し量の削減
加工されたワークや排出される切りくずに付着して、機械外に持ち出されるクーラント液も無視できません。
- 適切なドレンバック(液切り)
- 加工終了後、ワークや治具からクーラントが自然にタンクへ戻るように、機械内の滞留時間や搬送経路の傾斜などを考慮します。
- 自動化ラインでは、液切り工程を設けることも有効です。
- ワークからの持ち出し削減
- 加工後に圧縮エアブローでワーク表面のクーラントを吹き飛ばす(ただし、ミスト飛散には注意が必要)。
- ワーク形状によっては、遠心力を利用した脱水機(スピンドライヤー)を使用することも考えられます。
- 切りくずからの持ち出し削減
- 切りくずコンベアの設計や速度を調整し、液切り効果を高めます。
- 切りくずの種類や量によっては、ブリケッティングマシン(圧縮固形化装置)や遠心脱水機で油分を回収することも、油剤コスト削減と廃棄物処理コスト削減の両面に効果があります。
これらの地道な改善を積み重ねることで、日々のクーラント消費量を着実に減らすことができます。
2. 切削油の寿命を延ばすための管理方法

切削油の交換頻度を減らすこと、つまり「寿命を延ばす」ことも、トータルコスト削減において非常に重要です。交換には、新しい油剤の費用だけでなく、交換作業の手間、そして古い油剤の廃液処理費用がかかります。
1. 定期的なメンテナンスの徹底
切削油の劣化や腐敗を防ぎ、寿命を延ばすためには、適切なメンテナンスが不可欠です。
- フィルター交換・清掃
- 重要性
フィルターは、切りくずやスラッジなどの固形異物を除去し、油剤の清浄度を保つための重要な装置です。フィルターが目詰まりすると、異物除去能力が低下し、油剤の汚染が進行します。また、流量低下によるクーラント供給不足も引き起こします。 - 手順
定期的にフィルターの状態を確認し、目詰まりや破損があれば速やかに清掃または交換します。圧力計が付いている場合は、差圧の上昇を目安にするのも良いでしょう。フィルターの種類(ペーパー、マグネット、サイクロンなど)に応じて、適切なメンテナンスを行います。
- 重要性
- スラッジ除去(タンク清掃)
- 重要性
タンク底部に蓄積したスラッジは、バクテリアの温床となり、腐敗や悪臭の最大の原因です。また、攪拌されて油剤中に混入すると性能を低下させます。 - 手順
半年から1年に1回程度(使用状況による)を目安に、定期的なタンク清掃を実施します。古い液を抜き取り、タンク内のスラッジを物理的に除去し、必要に応じてタンククリーナー(洗浄・殺菌剤)を使用して洗浄・殺菌します。徹底した清掃が、次の油剤の寿命を大きく左右します。(詳細は切削油管理の記事をご参照ください)
- 重要性
- 殺菌処理
- 重要性
バクテリアの繁殖が確認された場合、一時的な対策として殺菌剤や防カビ剤の添加が考えられます。 - 注意点
ただし、これは対症療法であり、根本的な解決(スラッジ除去、適切な油剤選定)ではありません。また、薬剤の選定や使用量を誤ると、油剤性能の低下、耐性菌の発生、人体への影響などのリスクがあります。殺菌剤の使用は、必ず切削油メーカー(サンワケミカル株式会社など)に相談の上、適切な製品を正しい用法・用量で使用してください。
- 重要性
2. 適切な品質管理の継続
日々の品質管理も、劣化を遅らせる上で重要です。
- 濃度管理
適正な濃度範囲を維持することは、油剤の性能バランス(潤滑、冷却、防錆、防腐など)を保つ基本です。濃度が低すぎると耐腐敗性や防錆性が低下し、寿命が短くなります。 - pH管理
水溶性切削油のpHを適正範囲(通常8.5~9.5程度)に保つことは、防錆効果と耐腐敗性の維持に繋がります。pHが低下し始めたら、バクテリア繁殖などの原因を調査し、対策を講じます。pH調整剤の使用は、原因対策と合わせて慎重に行います。
3. 劣化要因の排除
切削油の劣化を早める要因を、可能な限り取り除く努力も必要です。
- 不適切な添加剤の使用禁止
「性能を上げたい」「泡を消したい」といった理由で、メーカー指定以外の添加剤を自己判断で加えることは絶対に避けてください。油剤の成分バランスが崩れ、予期せぬ分離、性能低下、劣化促進などを引き起こす可能性があります。添加剤が必要な場合は、必ずメーカーに相談してください。 - 異物混入の防止
- 混入油(浮上油)
機械からの作動油・潤滑油漏れは、油剤性能を低下させ、バクテリアの栄養源となります。オイルスキマーで定期的に除去するとともに、漏れ箇所の特定・修理を行います。 - その他の異物
ゴミなどをタンクに入れないよう、作業者の意識向上とルールの徹底を図ります。
- 混入油(浮上油)
4. 長寿命タイプの切削油の検討
油剤そのものを見直すことも有効です。サンワケミカル株式会社では、耐腐敗性や酸化安定性を高め、従来品よりも寿命を延ばすことを目指して開発された長寿命タイプの切削油もご用意しています。初期コストは多少高くても、交換頻度の削減や廃液処理コストの低減により、トータルコストでメリットが出る場合があります。
3. 適切な切削油を選び、無駄を削減する
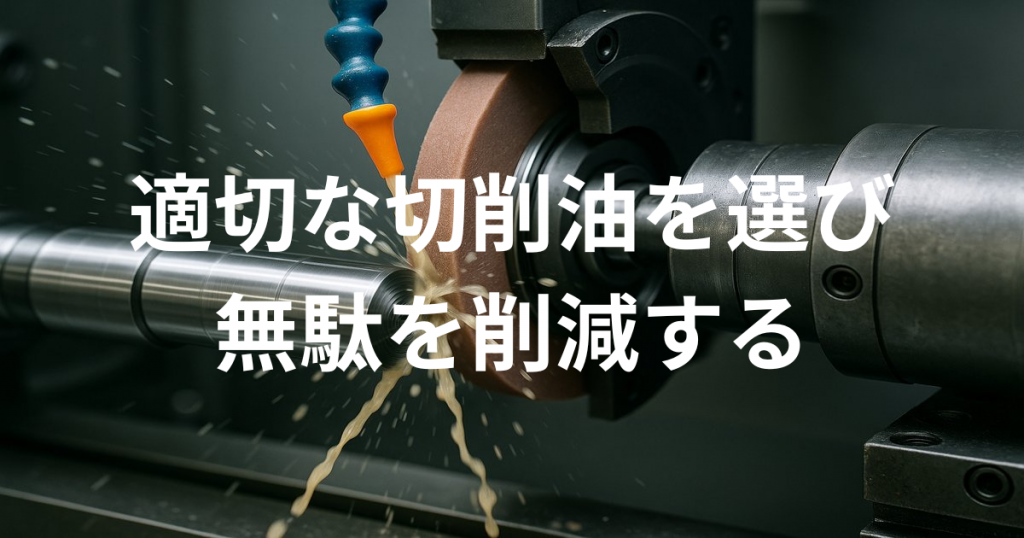
切削油のコストは、単価だけでなく、使用量、寿命、管理の手間などを総合的に考える必要があります。「価格が安いから」という理由だけで選んでしまうと、かえってトータルコストが高くつくことも少なくありません。
1. 現在使用している切削油の再評価
まずは、現在使用している切削油が本当に自社の加工や管理状況に最適なのか、客観的に評価してみましょう。
- 性能
要求される加工精度や工具寿命を満たしていますか? 特定のトラブル(錆、泡立ち、腐敗など)が頻発していませんか? - 寿命
交換頻度は適切ですか? もっと寿命の長い油剤に変えられないでしょうか? - 管理性
濃度やpHの管理はしやすいですか? 特殊なメンテナンスが必要ではありませんか? - コスト
現在の購入価格は妥当ですか? 交換頻度や廃液処理費用まで含めたトータルコストはどうでしょうか? - 汎用性
他の機械で使用している油剤と共通化できませんか?
惰性で同じ油剤を使い続けているケースも多いため、一度立ち止まって見直すことが重要です。
2. 最適な製品選びのポイント
新しい切削油を選定する際には、以下の点を考慮しましょう。
- 過剰スペックを選ばない
もちろん高性能な油剤は魅力的ですが、自社の加工に必要以上のスペック(例えば、特殊合金用ではないのに極めて高潤滑な油剤など)は、単なるコスト増に繋がります。加工内容に対して十分な性能を持ち、かつコストパフォーマンスに優れた製品を選びましょう。 - 汎用性の高い製品を選ぶ
もし複数の機械や異なる加工で同じ油剤を使用できれば、在庫管理が簡素化され、発注の手間が省けます。また、購入ロットをまとめることで単価交渉が有利になる可能性もあります。ただし、全ての加工で要求性能を満たせるか、慎重な確認が必要です。サンワケミカル株式会社では、幅広い加工に対応できる汎用性の高い製品もラインナップしています。 - 長寿命・管理性を考慮する
前述の通り、初期コストだけでなく、交換頻度や管理の手間まで含めたトータルコストで評価することが重要です。耐腐敗性が高く、濃度やpHが安定しやすい油剤は、管理の手間とコストを削減します。 - 環境・安全性を考慮する
PRTR法、消防法などの法規制への対応や、ミストの発生しにくさ、皮膚への刺激性なども、長期的な運用コストやリスク管理の観点から重要な選定要素です。
3. 最適な製品を見つける方法
- サンプルテストの実施
候補となる油剤が見つかったら、まずはサンプルを入手し、実際の機械で試用してみることを強くお勧めします。加工性能(精度、工具寿命)、泡立ち、臭い、濃度・pHの安定性などを、一定期間評価します。 - メーカーへの相談
自社の加工条件(被削材、機械、工具、加工方法)、現在抱えている問題点、コスト削減目標などを具体的に伝え、切削油メーカー(サンワケミカル株式会社など)に最適な製品の提案を求めましょう。専門的な知識に基づいたアドバイスが得られます。必要であれば、油剤の分析サービスなどを活用するのも良いでしょう。複数のメーカーから提案を受け、比較検討することも有効です。
適切な製品選びは、コスト削減の大きな一歩となります。
4. 集中管理システムの導入による効率化
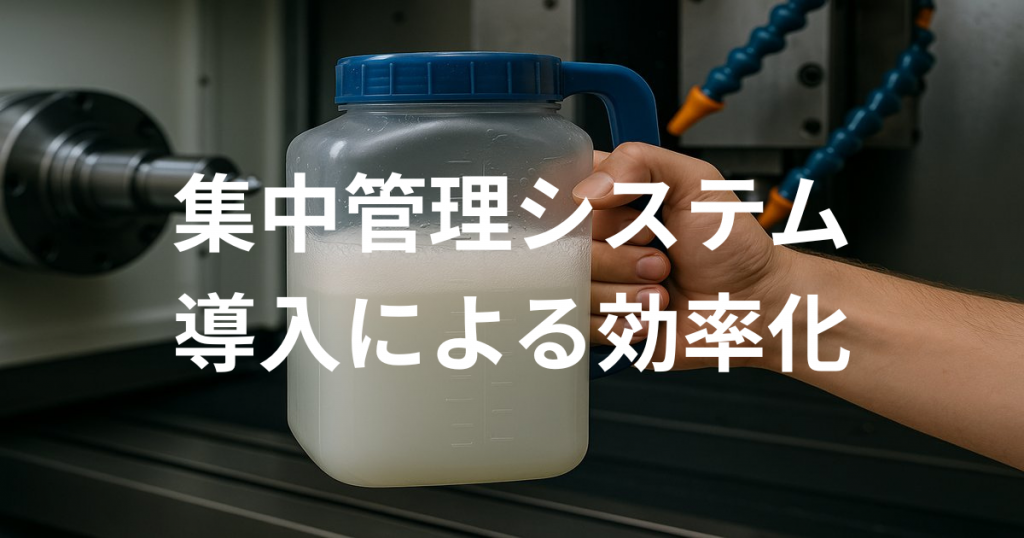
複数の工作機械を使用している工場では、「集中クーラントシステム」の導入が、コスト削減と管理効率化の有効な手段となる場合があります。
集中管理システムとは?
個々の工作機械にクーラントタンクを設置するのではなく、工場内の一箇所に大型のクーラントタンクと浄化装置(フィルター、温度調整装置、濃度・pH調整装置など)を設置し、そこから配管を通じて各機械へクリーンなクーラントを供給・循環させるシステムです。
導入によるメリット
- 品質の安定化と長寿命化
大容量タンクで管理するため、液温や濃度、pHなどの変動が少なく、常に安定した品質のクーラントを供給できます。高性能な浄化装置を組み込むことで、異物や劣化要因を効率的に除去でき、油剤の寿命を大幅に延ばすことが可能です。 - 使用量・購入量の削減
油剤寿命が延びるため、交換頻度が減り、結果的に年間の油剤購入量を削減できます。 - メンテナンスの効率化
フィルター交換やタンク清掃、濃度・pH管理といったメンテナンス作業を、集中タンクで一元的に行えるため、各機械を個別に管理する手間が大幅に削減されます。 - 廃液処理コストの削減
交換頻度が減ることで、廃液の排出量とそれに伴う処理コストを削減できます。 - 自動化による省人化
センサーによる自動監視や、濃度・pHの自動調整機能を組み込むことで、管理に関わる人手を削減できます。 - 省スペース化
各機械周りのクーラントタンクが不要になるため、工場内のスペースを有効活用できます。
導入時の注意点と費用対効果
- 高い初期投資
大型タンク、配管工事、ポンプ、浄化装置など、導入には相応の初期投資が必要です。 - システムダウン時のリスク
万が一システムが停止した場合、接続されている全ての機械が影響を受ける可能性があります。バックアップ体制なども考慮する必要があります。 - 油種の統一
原則として、システム内で使用するクーラントは1種類に統一する必要があります。多種多様な材質や加工を行っており、それぞれに専用の油剤が必要な工場では導入が困難な場合があります。 - 費用対効果の検討
導入コスト(設備費、工事費)と、長期的なランニングコスト削減効果(油剤費、メンテナンス人件費、廃液処理費、品質向上による間接効果など)を詳細に試算し、投資回収期間を評価することが重要です。
簡易的な集中管理システム
大規模な集中管理システムはハードルが高いと感じる場合でも、より簡易的な方法で効率化を図ることも可能です。
- 移動式クーラント浄化装置
カート式の浄化装置(フィルター、オイルスキマー、殺菌装置などを搭載)を各機械のタンクに移動させて、定期的にクーラントを浄化する方法。 - 小型タンクの連結
近接する複数の機械のタンクを配管で連結し、共通のフィルターやオイルスキマーで管理する方法。
自社の規模や状況に合わせて、導入可能な効率化策を検討してみましょう。集中管理システムの導入や効率化について、サンワケミカル株式会社でもご相談を承っております。
5. コスト削減効果を測定・評価する方法
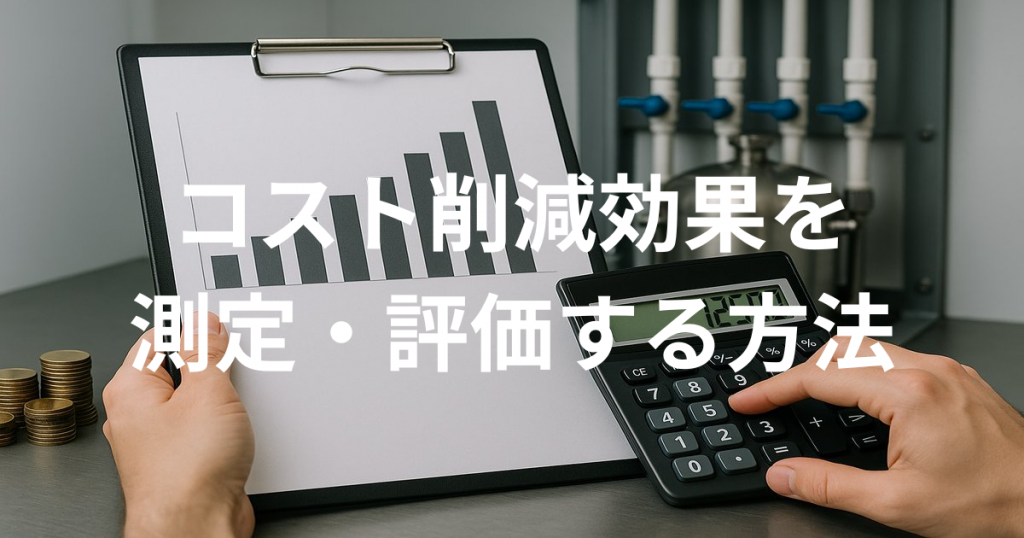
コスト削減活動は、「やりっぱなし」では意味がありません。目標を設定し、実施した対策の効果を定量的に測定・評価し、次の改善に繋げる「PDCAサイクル」を回すことが重要です。
1. コスト削減目標の設定と現状コストの把握
- 目標設定
まずは、具体的で測定可能な目標を設定します。例:「切削油購入コストを年間〇〇円削減する」「クーラント交換頻度を平均〇ヶ月に延長する」「廃液処理費用を〇%削減する」。タイトルにある「30%カット」も一つの目標例ですが、自社の実情に合わせて現実的な目標を設定しましょう。 - 現状コストの把握
目標設定のため、そして改善効果を測るためには、現状のコストを正確に把握する必要があります。過去1年間程度のデータを集計し、以下の項目などを洗い出します。- 直接コスト
- 切削油 購入量(L/年)と 購入金額(円/年)
- 交換回数(回/年)、交換量(L/回)
- 廃液処理量(L/年)、廃液処理費用(円/年)
- 補充用原液・水の消費量
- フィルターなどの消耗品費用
- メンテナンス(清掃、交換)にかかる人件費
- 間接コスト(推定含む)
- 切削油トラブル(腐敗、泡立ちなど)による機械停止時間
- 加工不良率(切削油が原因と疑われるもの)
- 工具交換頻度(目標寿命との比較)
- 直接コスト
2. 効果測定のための指標(KPI)設定
設定した目標に合わせて、コスト削減効果を測るための具体的な指標(KPI:Key Performance Indicator)を設定します。上記で洗い出した項目の中から、重点的に改善したい項目や測定しやすい項目を選びます。
- 例
- 切削油購入量(L/月)
- 単位生産量あたりの切削油コスト(円/個)
- クーラント交換間隔(月)
- 平均工具寿命(加工個数)
- 特定の加工不良の発生率(%)
- メンテナンス工数(時間/月)
3. 定期的な測定・評価と改善サイクルの実践
- 定期測定
設定したKPIを、定期的(例:毎月、四半期ごと)に測定し、記録します。 - 効果評価
測定結果を目標値や改善前の数値と比較し、実施したコスト削減策の効果を評価します。「どの対策がどれだけ効果があったか」「目標達成度はどうか」などを分析します。 - 改善サイクルの実践(PDCA)
- Plan(計画)
評価結果に基づき、現状の課題を特定し、次の改善策を計画します。 - Do(実行)
計画した改善策を実行します。 - Check(評価)
一定期間後に再びKPIを測定し、改善策の効果を評価します。 - Act(改善)
評価結果を踏まえ、計画を修正したり、さらなる改善策を検討したりします。 このPDCAサイクルを継続的に回していくことが、持続的なコスト削減を実現する鍵となります。効果測定の結果は関係者間で共有し、モチベーション向上やさらなるアイデア創出に繋げましょう。
- Plan(計画)
まとめ
本記事では、切削油にかかるコストを大幅に削減するための具体的な方法として、「消費量を減らす運用」「寿命を延ばす管理」「適切な製品選び」「集中管理システムの活用」「効果測定と評価」という5つのアプローチを解説しました。
「30%カット」という目標は決して簡単ではありませんが、日々の運用方法の見直し、適切なメンテナンスの実施、コスト意識を持った製品選定、そして管理体制の効率化といった多角的な視点からの地道な取り組みを積み重ねることで、着実なコスト削減は十分に可能です。
まずは自社の状況を把握し、取り組みやすいところから始めてみてはいかがでしょうか。この記事が、皆様のコスト削減活動の一助となれば幸いです。
サンワケミカル株式会社は、長年の経験と技術に基づき、多種多様な切削油剤を開発・製造しております。お客様の加工条件やニーズに合わせた最適な製品をご提案いたしますので、切削油に関するご相談は、ぜひお気軽にお問い合わせください。
もし、この記事で紹介した対策を試しても問題が解決しない場合や、お使いの切削油に関するより詳細な情報、お客様の特定の加工に最適な油剤の選定についてご相談がありましたら、どうぞお気軽に私たちサンワケミカル株式会社までお問い合わせください。経験豊富な専門スタッフが、お客様の状況を詳しくお伺いし、最適なソリューションをご提案いたします。
サンワケミカル株式会社HP:http://sanwachemical.co.jp/
サンワケミカル株式会社お問い合わせ:http://sanwachemical.co.jp/contact/
サンワケミカル株式会社公式X:https://x.com/sanwachemical
今後も、金属加工の現場で役立つ情報を発信してまいりますので、サンワケミカル株式会社公式ブログにご期待ください。