【小径工具の寿命UP】工具折損を防ぐ切削油の最適な使い方と注意点
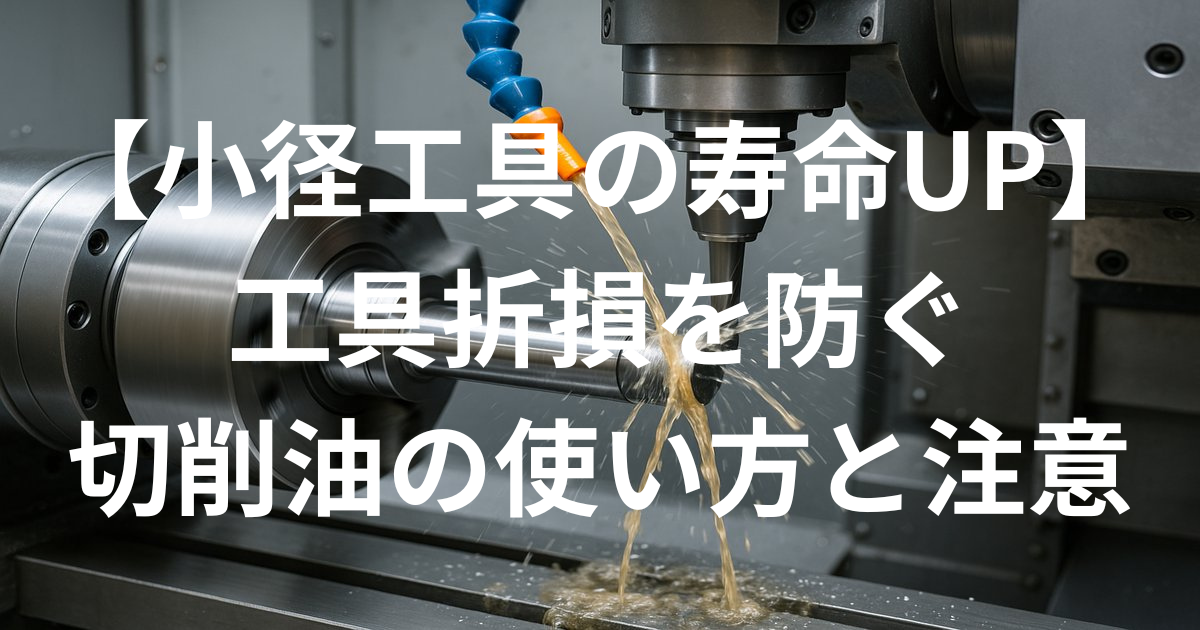
金型の微細な冷却穴、精密電子部品のコネクタ、医療機器のインプラント部品など、現代の製品製造において、小径工具(小径ドリル、小径エンドミルなど)を用いた微細加工の重要性はますます高まっています。しかし、その一方で、小径工具の加工は、現場担当者にとって最も神経を使い、トラブルが発生しやすい領域の一つでもあります。「ちょっとしたことで、すぐにドリルが折れてしまう…」「切りくずが詰まって加工が安定しない」「工具の摩耗が早すぎてコストがかさむ」といった悩みは、小径工具を扱う多くの現場で共通して聞かれる声ではないでしょうか。
これらの深刻なトラブル、特に小径工具の「折損」という最悪の事態を防ぎ、その性能を最大限に引き出すための、極めて重要な鍵を握っているのが切削油の管理と活用法です。小径工具加工では、その物理的な脆弱さゆえに、切削油が果たすべき役割が通常サイズの工具とは比較にならないほど重要になります。
この記事では、折損しやすくデリケートな小径工具を用いた加工を成功に導くため、切削油の選定、供給方法、そして管理に至るまで、その最適な使い方と注意点を徹底的に解説します。適切な切削油を「戦略的に」活用することで、工具寿命を延ばし、高精度な加工を安定して実現するための秘訣をお届けします。
1. 小径工具加工における切削油の重要性と課題
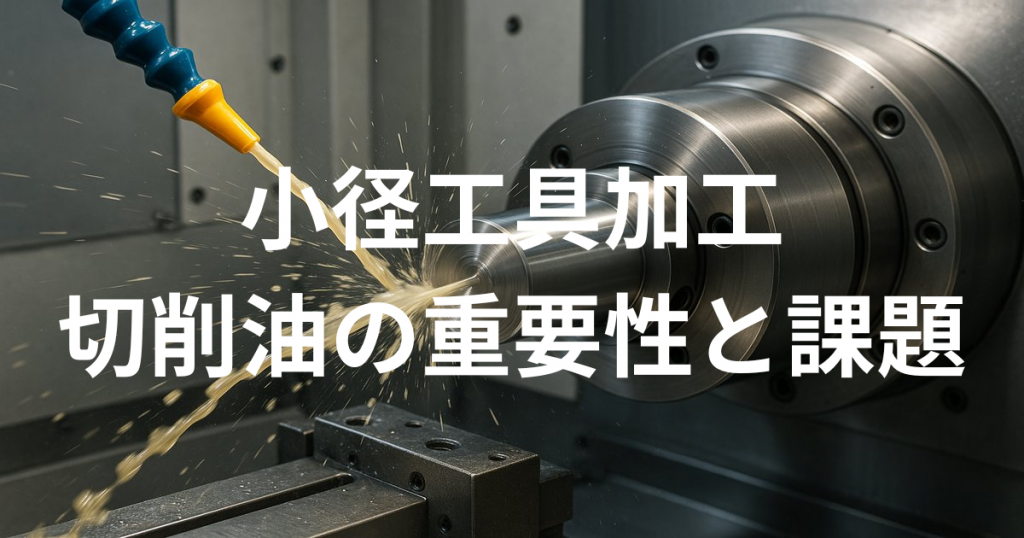
小径工具を用いた加工(ここでは、概ね直径φ3mm以下の工具を想定)は、通常サイズの工具での加工とは根本的に異なる、特有の難しさと課題を抱えています。これらの課題を理解することが、切削油の重要性を認識する第一歩となります。
課題1:工具の絶対的な「低剛性」と、常に隣り合わせの「折損リスク」
物理的な脆弱性
工具は、径が小さくなればなるほど、その断面積は径の2乗に比例して急激に小さくなり、物理的な強度が著しく低下します。また、工具の突き出し長さ(L)と直径(D)の比(L/D比)が大きくなる傾向があり、工具は非常にたわみやすく、振動しやすい状態に置かれます。
切削油の重要性
このように「折れやすい」という宿命を持つ小径工具にとって、切削油が果たすべき最も重要な役割は、切削抵抗を極限まで低減し、かつ安定させることです。
- 効果的な潤滑
強力な潤滑膜を形成し、工具とワーク間の摩擦を最小限に抑えることで、切削抵抗そのものを低く保ちます。 - 効果的な冷却
加工点で発生する熱を迅速に除去し、工具材料の軟化や、切りくずの溶着による切削抵抗の増大を防ぎます。
わずかな切削抵抗の増大や、加工中の抵抗の急な変動が、即座に工具のたわみ、振動、そして最終的には「折損」という致命的な結果に直結するため、切削油による効果的かつ安定した冷却・潤滑は、小径工具加工のまさに生命線と言えます。
課題2:極めて小さい「切りくず排出スペース」と、「切りくず詰まり」のリスク
物理的な制約
工具径が小さくなるにつれて、切りくずを排出するための溝(ドリルやエンドミルのフルート)の断面積も極めて小さくなります。このため、生成された切りくずが溝の中に詰まってしまう「切りくず詰まり(チップジャミング)」のリスクが、通常サイズの工具に比べて格段に高くなります。
切削油の重要性
切りくずが詰まると、(1)切削抵抗が急増し、工具折損の直接的な原因となる、(2)排出されずに再切削されることで工具に過大な負荷がかかる、(3)加工面に傷をつける、といった深刻な問題を引き起こします。 したがって、切削油には、この狭い空間から微細な切りくずをスムーズかつ強制的に洗い流し、排出するという、極めて重要な役割が求められます。切削油の高い洗浄性と、それを加工点まで確実に届ける供給技術が、この課題を克服する鍵となります。
これらの課題、「低剛性」と「切りくず排出の困難さ」は、小径工具加工において常に考慮しなければならない二大要素です。そして、その両方を解決するために、切削油の選定と使い方が決定的に重要になるのです。
2. 工具径と切削油の粘度と供給量の関係
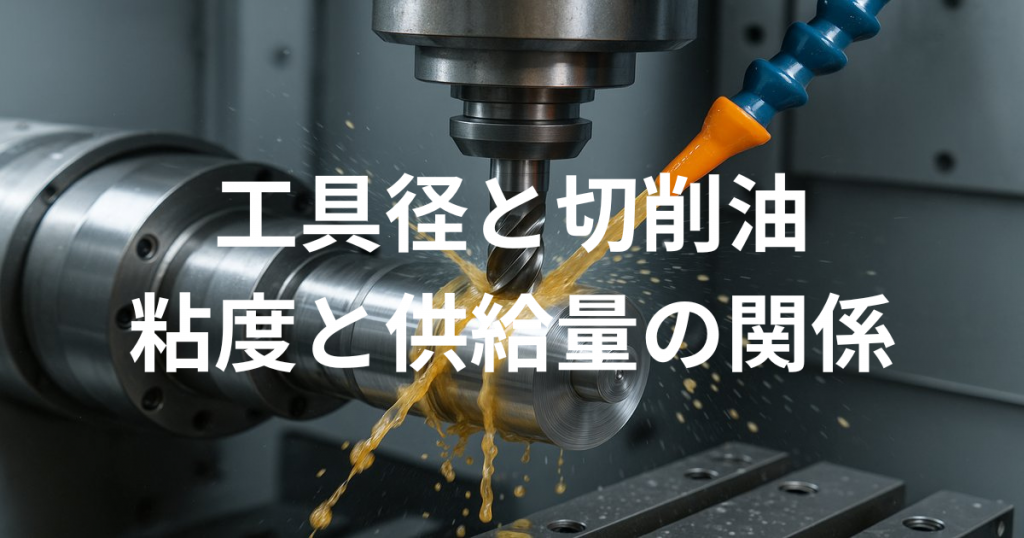
小径工具加工を成功させるためには、「どの切削油を選ぶか」そして「それをどれくらい供給するか」という二つの要素について、通常サイズの工具とは異なる、より繊細なアプローチが求められます。特に、切削油の「粘度」と「供給量」は、工具径との関係でその最適値が大きく変わってきます。
工具径が小さくなるほど「低粘度」の切削油が有利になる理由
浸透性の向上(毛細管現象)
工具径が小さくなると、工具と加工穴の壁面とのクリアランス(隙間)も極めて狭くなります。粘度が高い(ネトネトした)切削油は、この微細な隙間に入り込みにくく、肝心な刃先まで到達できない可能性があります。一方、粘度が低い(サラサラした)切削油は、表面張力の影響も受けにくく、毛細管現象によって微細な隙間にもスムーズに浸透していくことができます。これにより、刃先を確実に潤滑・冷却し、その効果を最大限に発揮させることができます。
洗浄性(切りくず排出性)の向上
低粘度の切削油は、流動性が高いため、工具の狭いフルート(溝)に詰まりがちな微細な切りくずを、効果的に洗い流し、外部へ排出する能力(洗浄性)に優れています。
冷却効果の向上
一般的に、低粘度の液体の方が熱伝達性に優れる傾向があり、加工点で発生した熱を迅速に奪い去る効果が期待できます。
粘度選定のバランス
もちろん、単に粘度が低ければ良いというわけではありません。潤滑性能は、ある程度の粘度によって形成される「油膜の厚さ」や「油膜強度」にも依存します。したがって、加工内容や切削条件(切削速度、負荷など)、被削材の種類に応じて、刃先への浸透性と、必要とされる潤滑性能を両立できる、最適な粘度範囲の切削油を選定することが重要です。サンワケミカルでは、極めて低粘度でありながら高い潤滑性能を発揮する、微細加工専用の切削油も開発・提供しております。
供給量:「量より質」の考え方と確実な供給の重要性
「クーラントバリア」の問題
通常サイズの工具と同じ感覚で、大量の切削油を単純に加工点にかけ流す(フラッド供給)と、特に工具が高速で回転している場合、工具の周囲に切削油の「壁」や「ドーム」のようなものが形成されてしまい(クーラントバリア現象)、かえって切削油が刃先に到達するのを妨げてしまうことがあります。また、大量の液体の表面張力が、デリケートな小径工具の挙動に悪影響を与える可能性も指摘されています。
「いかに確実に刃先に届けるか」が重要
小径工具加工における切削油供給の要点は、「とにかく量をかける」ことではなく、「必要な量の切削油を、いかにして確実に、かつ安定して刃先に届け続けるか」という点にあります。この課題を解決するために、次項で解説するような、特殊な供給方法が有効となります。
つまり、小径工具加工では、「浸透性と洗浄性に優れた低粘度の油剤を、最も効果的な方法で、ピンポイントに刃先へ供給する」という考え方が、成功への基本戦略となるのです。
3. ミストクーラント、内部給油など最適な供給方法
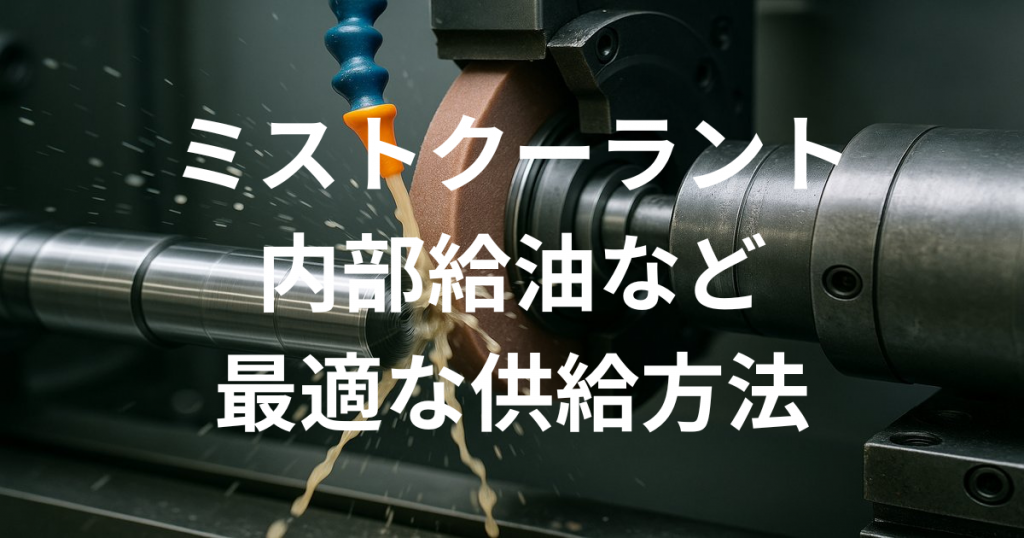
前項で述べた「切削油をいかに確実に刃先に届けるか」という課題を解決するため、小径工具加工では、一般的なかけ流し(フラッド供給)方式に代わり、あるいはそれを補完する形で、いくつかの特殊な供給方法が効果的に用いられます。ここでは、代表的な供給方法のメリット、デメリット、そして適用事例を紹介します。
ミストクーラント(MQL:Minimum Quantity Lubrication、最小量潤滑)
供給方法
ごく微量(数mL/h~数十mL/h程度)の切削油(MQL専用油)を、圧縮空気と混合して霧(ミスト)状にし、ノズルから加工点に直接吹き付ける方法です。
メリット
- ピンポイント供給
狙った箇所(刃先)に、ピンポイントで潤滑成分を供給できます。 - 使用量の劇的な削減
油剤の使用量が極めて少ないため、環境負荷が低く、廃液処理コストもほとんどかかりません。 - ワークの清浄性
加工後のワークや切りくずがドライに近い状態で取り出せるため、洗浄工程を簡略化または省略できます。 - 高い冷却効果
油剤が気化する際の「気化潜熱」を利用するため、冷却効果も期待できます。
デメリット
- 潤滑能力の限界
供給される油量が絶対的に少ないため、高負荷な加工や潤滑要求の高い加工には不向きです。 - 切りくず排出能力の低さ
液体の流れによる洗浄効果は期待できないため、切りくずは主にエアブローによって排出することになります。 - 専用設備の必要性
MQL装置や、場合によってはMQL対応の工作機械が必要となります。 - ミストの管理
作業環境中に飛散するミストを捕集するための、高性能なミストコレクターが不可欠です。
適用事例
アルミニウム合金や銅合金、樹脂といった比較的加工しやすい材料の軽切削、微細な穴あけやエンドミル加工、高速仕上げ加工などに適しています。
エアブローの併用
供給方法
切削油の供給と同時に、あるいは間欠的に、別のノズルから圧縮空気を加工点に吹き付けます。
メリット
- 強力な切りくず排出
エアの力で、微細で軽い切りくずや、溝の奥に溜まった切りくずを強制的に吹き飛ばします。 - 冷却効果の補助
空気の流れが、ある程度の冷却効果をもたらします。
デメリット
- 切削油の飛散助長
切削油を周囲に飛散させ、オイルミストの発生量を増加させるため、強力なミストコレクターと機械全体を覆うフルカバーが必須です。 - 騒音の発生
高圧のエアを噴射するため、大きな騒音が発生します。
適用事例
ドライ加工やMQLと組み合わせて切りくず排出を補助する場合や、ウェット加工でも特に切りくずが詰まりやすいポケット加工などで限定的に使用されます。
内部給油(オイルホール付き工具、スルークーラント)
供給方法
小径ドリルやエンドミル、あるいはツールホルダーの内部に設けられた微細な油穴(オイルホール)を通じて、工具の先端(切れ刃のすぐ近く)から直接、高圧で切削油を噴射する方式です。
メリット
- 確実な潤滑・冷却
工具がどれだけ深く穴に入り込んでも、あるいは高速で回転していても、遠心力や外部の流れに影響されずに、最も重要な刃先に直接ピンポイントで切削油を供給できます。 - 最高の切りくず排出能力
高圧の噴流が、工具の狭いフルート(溝)に詰まりがちな切りくずを、穴の奥から強制的に、かつ連続的に排出し続けます。 - 加工能率の大幅な向上
これらの効果により、工具折損や切りくず詰まりのリスクが劇的に低減されるため、切削条件(送り速度など)を大幅に向上させ、加工時間を短縮することが可能です。
デメリット
- コスト: オイルホール付きの専用工具や、主軸からクーラントを供給できる「スピンドルスルークーラント」機能を搭載した工作機械が必要となるため、初期投資は高くなります。
- 油剤管理の重要性
微細なオイルホールを詰まらせないために、切削油の「清浄度管理」が極めて重要になります。
適用事例
小径工具を用いた深穴加工や、ステンレス鋼、チタン合金といった難削材の加工、そして高能率・高信頼性が求められる量産加工など、シビアな条件の小径工具加工において、最も確実で効果的なソリューションと言えます。
加工条件や工具形状に合わせた最適な供給方法の選び方
どの供給方法が最適かは、単一の正解があるわけではなく、それぞれの加工が持つ独自の条件や目指すべき目標を総合的に考慮して決定する必要があります。ここでは、最適な供給方法を選び出すために検討すべき、6つの重要なポイントを解説します。
1. 加工の目的と要求品質
まず、その加工における最優先事項は何かを明確にします。最高の寸法精度と表面粗さを追求するのか、サイクルタイムを短縮して生産コストを優先するのか、あるいはオイルミストの発生を抑えて作業環境を重視するのか。この優先順位によって、選択すべき供給方法は大きく変わってきます。
2. 被削材の種類
加工する材料の特性を考慮します。例えば、アルミニウム合金のように切りくずが排出されやすく、比較的加工しやすい材料であればMQLも選択肢になりますが、ステンレス鋼のように粘り強く、切りくずが長く繋がりやすい材料では、ウェット供給による強力な切りくず排出能力が求められます。
3. 加工形状
穴の深さ(L/D比)、溝の幅や深さ、そして切りくずが排出されやすい「開放形状」か、排出が困難な「閉じた形状(ポケット)」かなどを評価します。L/D比が5を超えるような深穴や、深いポケット加工では、内部給油(スルークーラント)方式が極めて有効になります。
4. 使用する工具
使用する小径工具自体が、特殊な供給方法に対応しているかを確認します。内部給油(オイルホール)に対応した工具でなければスルークーラントは利用できません。また、工具の剛性が低い場合は、切削抵抗を極限まで下げる潤滑重視の供給方法が求められます。
5. 工作機械の仕様
お使いの工作機械が、スピンドルスルークーラント機能やMQL装置といった、特殊な供給方法に対応できる設備を備えているか、あるいは後付けが可能かどうかを確認します。機械の仕様が、選択できる供給方法の幅を決定づけます。
6. コストと生産性のバランス
専用装置などの初期投資と、それによって得られる工具寿命の延長、加工時間短縮による生産性向上、油剤コストの削減といった長期的なメリットを比較検討します。例えば、内部給油システムの導入は高価ですが、工具折損による損失や加工停止時間を大幅に削減できるため、トータルコストでは有利になるケースが多くあります。
これらのポイントを一つひとつ丁寧に検討し、自社の状況に最も合致した供給方法を選択することが、小径工具加工の成功への近道です。例えば、比較的浅い穴の軽切削であれば一般的な注油方式でも対応可能かもしれませんが、L/D比が5を超えるような深穴加工では、内部給油方式の導入を積極的に検討すべきです。また、ドライ加工が可能な材質であれば、MQLとエアブローの組み合わせも有効な選択肢となります。れば、MQLとエアブローの組み合わせも有効な選択肢となります。
4. 小径工具の折損を防ぐための切削油選定のポイント
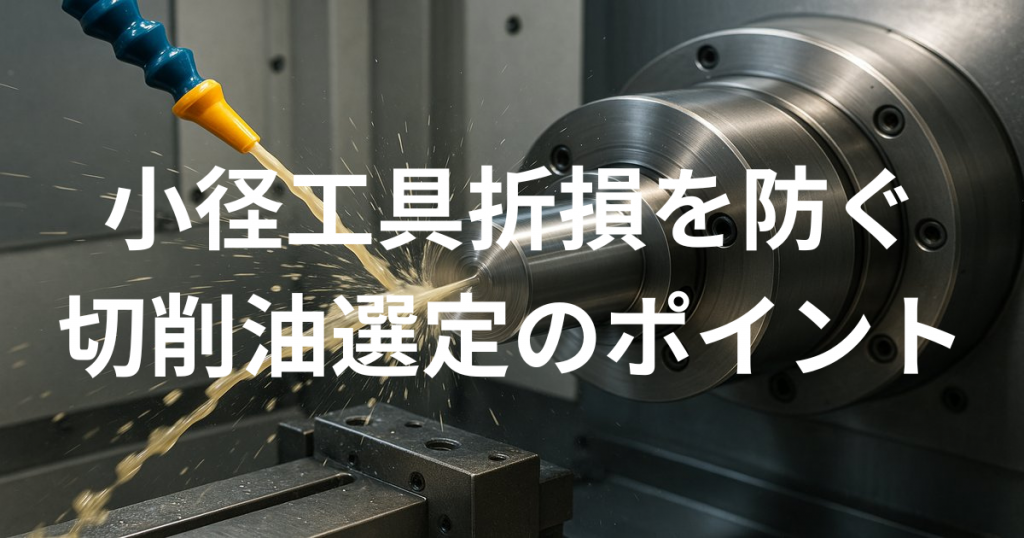
小径工具加工における最大の悪夢である「工具折損」は、その原因の多くが切削抵抗の急激な増大にあります。そして、この切削抵抗を低く、かつ安定してコントロールするために、切削油の「潤滑性能」が決定的に重要な役割を果たします。ここでは、小径工具の折損を未然に防ぐという観点から、切削油の選定における重要なポイントを解説します。
潤滑性能に優れた油性切削油や、極圧(EP)添加剤を含む切削油の有効性
潤滑性能の追求が最優先
小径工具は物理的に非常に折れやすいため、切削抵抗を可能な限り低減させることが、折損を防ぐための最も直接的で効果的なアプローチです。そのため、切削油の選定においては、高い潤滑性が最優先されるべき性能となります。
油性切削油の優位性
一般的に、油性切削油は水溶性切削油に比べて、潤滑油膜の形成能力やその強度に優れています。特に、小径工具を用いた難削材の加工や、厳しい条件下での微細加工においては、高い潤滑性を持つ油性切削油が、折損リスクを低減する上で非常に有効な選択肢となります。
極圧(EP)添加剤の重要性
タップ加工と同様に、小径工具の切れ刃先端は、極めて高い接触圧力と温度にさらされます。硫黄系、リン系などの極圧添加剤は、このような過酷な条件下で金属表面と化学反応し、通常の潤滑膜が破れても金属同士の直接接触(凝着や溶着)を防ぐ特殊な反応膜(極圧膜)を形成します。この極圧膜が、切れ刃を保護し、切削抵抗の急増を防ぎ、工具折損を回避する上で極めて重要な役割を果たします。
水溶性切削油を使用する場合の選定ポイント
マシニングセンタでの汎用性や、火災リスク、作業環境への配慮から水溶性切削油を使用する場合は、潤滑性能を可能な限り高めたタイプを選定する必要があります。
- 鉱物油の含有率が高く、潤滑性に優れるエマルション型。
- 油性向上剤(エステル、特殊ポリマーなど)や極圧添加剤を特殊配合し、潤滑性能を大幅に強化した高潤滑タイプのソリュブル型やシンセティック型。 これらの水溶性切削油を使用する際は、メーカー推奨範囲内で濃度を高めに管理することで、潤滑成分の有効濃度を高め、性能を引き出す工夫も重要です。サンワケミカルでは、水溶性でありながら高い潤滑性を発揮し、小径工具加工にも優れた性能を示す特殊な切削油も開発・提供しております。
工具材種(超硬、ハイスなど)との化学的な適合性
超硬工具
現在の小径工具の主流である超硬合金は、化学的に比較的安定していますが、切削油に含まれる一部の添加剤(例えば、特定の条件下での活性硫黄など)や、極端なpH条件下では、結合材であるコバルトが溶出するなどの影響を受ける可能性がゼロではありません。基本的には大きな問題になることは少ないですが、特殊な油剤を使用する場合は、適合性を確認することが望ましいです。
ハイス(高速度鋼)工具
小径のタップや特殊なエンドミルなどでは、ハイスも依然として使用されます。ハイスは超硬に比べて耐熱性が低いため、潤滑性だけでなく、冷却性も重要な要素となります。潤滑性と冷却性のバランスが取れた切削油(例えば、エマルション型水溶性切削油など)の選定が求められます。
コーティング工具
TiN、TiCN、TiAlN、DLC(ダイヤモンドライクカーボン)など、様々なコーティングが施された小径工具が広く使用されています。切削油は、これらのコーティングの性能(例えば、低摩擦性や耐酸化性)を阻害せず、むしろその性能を補完し、相乗効果を発揮できるものであることが理想です。例えば、DLCコーティングは、油とのなじみが悪い場合があるため、専用の切削油が推奨されることもあります。
ワーク材質(被削材)との相性も踏まえた総合的な油種選定
最終的には、ワーク材質との相性も考慮しなければなりません。
- 非鉄金属(銅合金、アルミニウム合金など)
硫黄系の活性型極圧添加剤は、銅合金を著しく変色させる原因となります。アルミニウム合金に対しては、アルカリ性の強い水溶性切削油が腐食を引き起こす可能性があります。これらの材料には、それぞれに対応した、化学的に不活性な、あるいは専用の腐食防止剤が配合された切削油を選定する必要があります。 - 難削材(ステンレス鋼、チタン合金など)
これらの材料は、加工硬化性が高く、熱伝導率が低く、工具との親和性(凝着しやすさ)が高いため、極めて高い潤滑性と極圧性が要求されます。難削材加工専用に設計された高性能な切削油の選定が、工具折損を防ぎ、加工を成功させるための鍵となります。
工具折損を防ぐための切削油選定は、単に「潤滑性が高ければ良い」という単純な話ではなく、「工具径」「工具材質」「ワーク材質」「加工方法」「供給方法」といった多くの要因を総合的に考慮し、最適なバランスの油剤を見つけ出す、高度な技術的判断が求められる作業です。判断に迷われる場合は、ぜひ私たちサンワケミカルのような切削油の専門家にご相談ください。
5. 微細加工における切削油管理の注意点
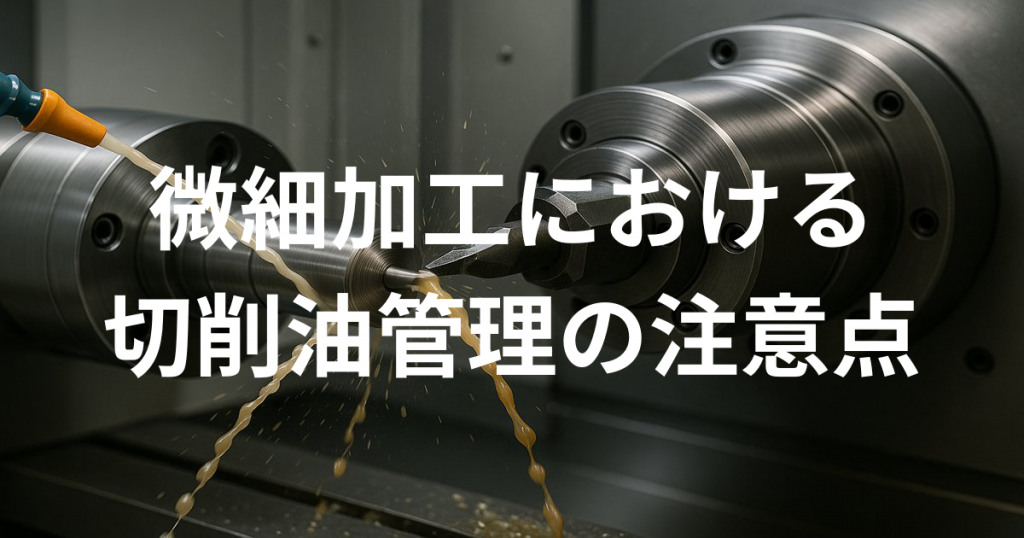
小径工具加工の中でも、特に工具径がφ1mmを下回り、時には数十μm(マイクロメートル)といった領域にまで及ぶ「微細加工(マイクロマシニング)」の世界では、切削油の管理に対する要求レベルが、一般的な機械加工とは比較にならないほど厳しくなります。ここでは、微細加工を成功させるために不可欠な、より高度な切削油管理の注意点について解説します。
高度な「清浄度管理」:μm単位の異物が致命傷に
なぜ、より重要になるのか
一般的な加工では問題にならないような数μmレベルの微細な異物(金属粉、外部からのホコリ、油剤の劣化物など)ですら、微細加工においては、使用する工具径に対して相対的に非常に大きな存在となります。このような微細な異物が、工具とワークの間にわずかでも噛み込まれると、
- 即座に工具の切れ刃をチッピングさせ、工具折損に直結する。
- 加工面に深いスクラッチ傷をつけ、製品品質を致命的に損なう。
- 工具内部の微細なオイルホール(内部給油の場合)を完全に詰まらせ、潤滑・冷却不良を引き起こす。 といった、深刻なトラブルの原因となります。
求められる管理レベルと対策
- 超精密ろ過システムの導入
サブミクロン(1μm未満)レベルの超微細粒子まで除去可能な、高性能な精密フィルターシステム(例えば、絶対ろ過精度1μm以下のカートリッジフィルター、あるいはさらに高性能なメンブレンフィルターなど)の導入が不可欠となります。 - 多段ろ過の採用
粗い粒子を除去するプレフィルターと、微細な粒子を除去するメインフィルターを組み合わせる「多段ろ過」方式により、効率的に高い清浄度を達成し、かつメインフィルターの寿命を延ばします。 - リアルタイム清浄度モニタリング
パーティクルカウンターなどのセンサーを用いて、切削油中の異物のサイズと数をリアルタイムで監視し、清浄度レベル(例えば、NAS等級やISO等級で厳密に管理)を常に目標範囲内に維持します。 - クリーンな環境の維持
クーラントタンクの密閉化、クリーンエアによるタンク内圧の陽圧化、油剤交換・補充時のクリーンな手順の徹底など、外部からの新たな汚染物質の混入を徹底的に防止する取り組みが必要です。
厳密な「温度管理」:μm単位の熱変位を制御する
なぜ、より重要になるのか
微細加工でターゲットとする加工精度は、多くの場合、μmオーダーあるいはそれ以下の極めて厳しい公差が設定されています。このような状況下では、ワークピース、工具、そして工作機械本体のわずかな温度変化によって引き起こされる熱変位(熱膨張・収縮)が、最終的な加工精度に支配的な影響を与えます。
求められる管理レベルと対策
- 高精度クーラントチラーの活用
切削油の温度を、例えば室温に対して±0.1℃といった極めて高い精度で厳密にコントロールできる高性能なチラーを導入し、加工系全体の熱的安定性を確保します。 - 機械全体の恒温管理
究極の精度を求める場合は、微細加工機自体を、温度と湿度が厳密に管理された恒温室内に設置することが望まれます。
微量給油(MQL)という特殊な選択肢
MQLの適用拡大
微細加工の領域では、ウェット供給(かけ流し)による大量の切削油が持つ液体の表面張力や粘性抵抗、あるいは液圧そのものが、デリケートな微細工具の挙動に悪影響を及ぼすことがあります。また、加工後の微細な構造物からの洗浄が困難であるといった課題もあります。 このような背景から、微細加工においては、ごく微量の切削油を圧縮空気とともにミスト状にして加工点に供給する「微量給油(MQL)」が、標準的な冷却・潤滑方法として積極的に採用されるケースが増えています。
MQLにおける注意点
- MQL専用油剤の選定
MQLで使用される切削油には、(1)ごく微量でも高い潤滑性を発揮する能力、(2)ミスト化しやすく、かつ作業環境への飛散が少ない低ミスト性、(3)加工後の残留物が少ない、あるいは洗浄が容易であること、(4)環境負荷を考慮した高い生分解性、といった特殊な性能が求められます。汎用の切削油を流用するのではなく、必ずMQL専用に設計された油剤を選定する必要があります。 - ミストの供給制御
ミストの粒子径、油剤の吐出量、エアの圧力と流量といった供給条件を、加工内容に合わせて精密にコントロールすることが、安定した加工を実現する上で極めて重要になります。
微細加工は、切削油の管理という観点からも、一般的な機械加工の延長線上にはない、特別な配慮と高度な技術が要求される領域です。サンワケミカルでは、このような最先端の微細加工分野の要求に応えるべく、超精密ろ過に対応した高清浄度な切削油や、高性能なMQL専用油剤の研究開発にも力を入れており、お客様の高度な技術的課題の解決をサポートしています。
まとめ
本記事では、破損のリスクが常に伴う、デリケートで難しい「小径工具」を用いた切削加工において、その工具の寿命を延ばし、トラブルなく安定した高精度加工を実現するための、切削油の効果的な管理と活用法について、多角的な視点から詳しく解説してまいりました。
小径工具加工における切削油は、単なる補助的な役割に留まらず、
- 低剛性な工具を折損から守るための、極めて重要な「潤滑」
- 熱容量の小さい工具を熱的損傷から守るための、的確な「冷却」
- 狭いスペースから切りくずを排出し、詰まりによる破損を防ぐ「切りくず排出」 という、加工の成否そのものを左右する、決定的に重要な役割を担っています。
この記事でご紹介した、小径工具の特性に合わせた「低粘度・高潤滑」な切削油の選定、MQLや内部給油といった「最適な供給方法」の適用、そして潤滑性能を最大化するための「添加剤」の考慮、さらには微細加工に求められる「高度な清浄度・温度管理」といったポイントを実践することで、小径工具が持つ本来の性能を最大限に引き出し、これまで困難であった高精度な加工と、生産性の向上を両立させることが可能となるはずです。
もし、現在お悩みの小径工具の折損問題や、微細加工における品質課題など、切削油に関わることで解決の糸口を探しておられるのであれば、ぜひ一度、私たちサンワケミカル株式会社の専門スタッフにご相談ください。私たちは、お客様の具体的な加工内容、使用工具、工作機械、そして目指すべき品質レベルを詳細にお伺いした上で、長年の経験と最新の技術情報に基づいた最適な切削油製品のご提案と、その効果を最大限に引き出すためのトータルな活用ソリューションをご提供させていただきます。
皆様の微細で高精度なものづくりを、高性能な切削油を通じて、これからも力強くサポートしてまいります。
サンワケミカル株式会社は、長年の経験と技術に基づき、多種多様な切削油剤を開発・製造しております。お客様の加工条件やニーズに合わせた最適な製品をご提案いたしますので、切削油に関するご相談は、ぜひお気軽にお問い合わせください。
もし、この記事で紹介した対策を試しても問題が解決しない場合や、お使いの切削油に関するより詳細な情報、お客様の特定の加工に最適な油剤の選定についてご相談がありましたら、どうぞお気軽に私たちサンワケミカル株式会社までお問い合わせください。経験豊富な専門スタッフが、お客様の状況を詳しくお伺いし、最適なソリューションをご提案いたします。
サンワケミカル株式会社HP:http://sanwachemical.co.jp/
サンワケミカル株式会社お問い合わせ:http://sanwachemical.co.jp/contact/
サンワケミカル株式会社公式X:https://x.com/sanwachemical
今後も、金属加工の現場で役立つ情報を発信してまいりますので、サンワケミカル株式会社公式ブログにご期待ください。