【高速加工成功の秘訣】高効率と高品質を両立する切削油の活用方法
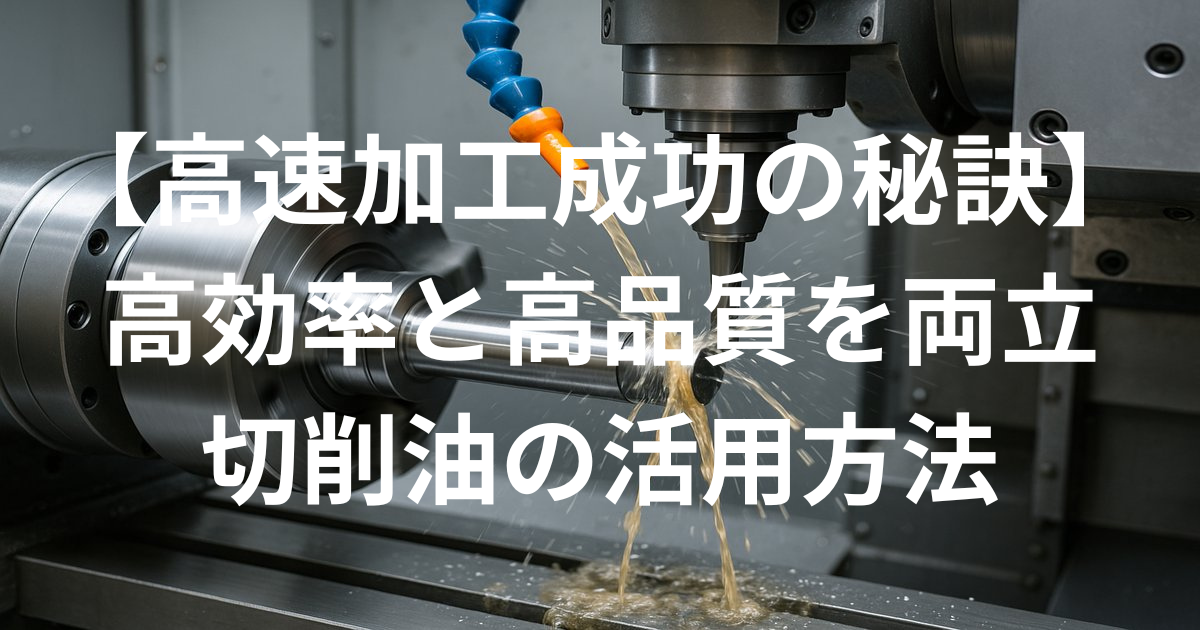
生産性向上の切り札として、多くの金属加工現場で導入が進む「高速加工」。切削速度を大幅に引き上げることで、加工時間を劇的に短縮し、製造コストの削減に大きく貢献するこの技術は、現代のものづくりに不可欠な存在となっています。しかし、その一方で、「工具の摩耗が異常に早くて、かえってコストがかかる」「加工面の品質が安定しない」「大量に発生するオイルミストで作業環境が悪い」といった、高速加工特有の新たな課題に直面している現場担当者様も少なくないのではないでしょうか。
実は、これらの課題を克服し、高速加工のメリットである「高効率」と、製品に求められる「高品質」を両立させるための成功鍵を握っているのが、切削油の戦略的な活用です。高速加工という極めて過酷な環境下では、切削油に求められる役割も通常とは異なり、その選定、供給方法、そして管理のすべてにおいて、より高度なノウハウが必要となります。
この記事では、高速加工のポテンシャルを最大限に引き出すための切削油活用法に徹底的に焦点を当てます。高速加工における切削油の特殊な役割と課題から始まり、その過酷な環境に対応できる最適な油剤の選び方、効果を最大化する供給方法、そして加工精度と品質を安定させるための熱対策と管理のポイントまで、現場ですぐに役立つ実践的な情報を網羅的に解説いたします。切削油を「高速加工のパートナー」として正しく使いこなし、皆様の生産性を新たな次元へと引き上げるための一助となれば幸いです。
1. 高速加工における切削油の役割と課題(冷却、潤滑、ミスト対策)
-1024x538.png)
高速加工における切削油の最重要課題は、「高発熱」「潤滑膜の維持」「オイルミスト」という三つの大きな壁を克服することです。これを解決するため、切削油は、卓越した冷却性能、高速下でも破断しない潤滑性能、そして作業環境を守る低ミスト性という、三位一体の高度な役割を同時に果たす必要があります。
高速加工は、単に切削速度が速いだけでなく、それに伴い加工点で起こる物理現象も通常とは大きく異なります。この特有の環境下で、切削油が担うべき役割とその重要性、そして直面する課題を理解することが、適切な対策を講じるための第一歩となります。
高発熱との戦い:卓越した「冷却作用」の重要性
なぜ、より多くの熱が発生するのか
切削速度が上がると、単位時間あたりに除去される金属の体積が増加し、それに伴って発生する熱量も飛躍的に増大します。特に高速加工では、切りくずがワークから引きちぎられる際の「せん断変形」による熱の割合が大きくなり、その熱の多くが高温の切りくずとして排出されますが、工具の切れ刃やワークの加工表面にも極めて大きな熱負荷がかかります。
冷却不足が招く深刻な問題
この膨大な熱を効果的に除去できなければ、
- 工具の熱的損傷
工具の切れ刃が高温になりすぎて硬度が低下(軟化)し、塑性変形を起こしたり、酸化摩耗や拡散摩耗といった熱化学的な摩耗が急速に進行したりして、工具寿命が著しく短くなります。 - ワークの加工精度低下
ワークピースが熱膨張し、加工中と加工後で寸法が変化する「熱変位」が大きくなり、精密な寸法精度を維持できなくなります。 - 加工面の品質劣化
高温により、加工面に焼けや変色が生じたり、加工変質層が形成されたりします。
切削油に求められる役割
したがって、高速加工における切削油には、この莫大な熱量を迅速に、かつ効率的に奪い去る、極めて高い「冷却性能」が第一に求められます。
高速回転下での挑戦:「潤滑性能」の維持
なぜ、潤滑が難しくなるのか
高速加工では、工具とワーク、そして切りくずが接触する時間が極めて短くなります。また、高速で回転する工具やワークの遠心力、そしてその周囲に発生する空気の層(エアバリア)によって、供給された切削油が加工点に到達する前に吹き飛ばされてしまい、潤滑油膜を安定して形成することが非常に困難になります。
潤滑不足が招く問題
たとえ接触時間が短くても、潤滑が不十分だと、
- 工具摩耗の促進
切れ刃の逃げ面摩耗(フランク摩耗)や、すくい面摩耗(クレータ摩耗)が進行し、工具寿命を縮めます。 - 仕上げ面品位の悪化
加工面のむしれや溶着、引きずり傷の原因となります。 - 切削抵抗の増大
加工動力が上昇し、機械への負荷が増えます。
切削油に求められる役割
高速加工における切削油には、短い接触時間の中でも瞬時に油膜を形成し、かつ高速回転下でも飛散しにくい、優れた「潤滑性能」と「付着性・浸透性」が求められます。
作業環境との共存:「オイルミスト対策」の必要性
なぜ、オイルミストが発生しやすいのか
高速で回転する工具やワークに切削油が衝突すると、油剤は激しくせん断され、微細な液滴となって空気中に飛散します。これが「オイルミスト」です。また、加工点の高温によって油剤の一部が蒸発し、それが冷えて凝縮することでもミスト(油煙)が発生します。高速加工は、この両方のミスト発生メカニズムを助長する、極めて厳しい条件です。
オイルミストがもたらす問題
- 作業者の健康への影響
オイルミストを長期間吸入すると、呼吸器系の疾患を引き起こすリスクがあります。また、皮膚に付着すれば皮膚炎の原因ともなり得ます。 - 作業環境の悪化
工場内の床や壁、設備が油で汚れ、滑りによる転倒事故のリスクが高まります。視界が悪くなることもあります。 - 火災リスク
油性の切削油を使用している場合、空気中に浮遊する高濃度のオイルミストは、引火の危険性を高めます。
切削油に求められる役割
したがって、切削油自体がミストになりにくい性質(低ミスト性)を持つこと、そしてオイルミストの発生を抑制できる適切な供給方法を選択することが、安全でクリーンな作業環境を維持するために不可欠となります。
まとめると、高速加工では、発生する莫大な熱を効果的に除去する「冷却」、高速回転下でも破断しない「潤滑」、そして作業環境を守る「ミスト対策」という、三つの大きな課題に対応できる高性能な切削油とその活用法が、成功の鍵を握っているのです。
2. 高速回転に対応した切削油の選び方(低粘度、耐熱性)
-1024x538.png)
高速加工の成功は、その過酷な環境に適応できる切削油を選び出すことから始まります。選定のポイントは、刃先への確実な到達と高い熱交換効率を実現する「低粘度」と、高温下でも性能を維持し続ける「優れた熱・酸化安定性」です。その上で、加工内容や要求性能に応じて、油性と水溶性のメリット・デメリットを理解し、最適なタイプを選択することが重要になります。
高速回転下で活きる「低粘度」切削油の有効性
高速加工においては、一般的に粘度が低い(サラサラとした)切削油が有利とされます。その理由は、以下の三つの点にあります。
浸透性の向上
高速で回転する工具の周囲には、空気の層(エアバリア)が形成され、外部から供給される切削油が刃先に到達するのを妨げます。低粘度の切削油は、このエアバリアを突破し、工具とワーク間の微細な隙間にも迅速に浸透していく能力に優れています。これにより、最も重要な加工点での確実な冷却と潤滑を実現します。
冷却効果の向上
低粘度の液体は、一般的に流動性が高く、熱伝達性に優れるため、加工点で発生した熱を効率よく奪い去り、運び去ることができます。また、洗浄性も高いため、高温になった切りくずを速やかに加工点から除去し、熱だまりを防ぐ効果も期待できます。
切りくず排出性の向上
高速加工では大量の切りくずが生成されますが、低粘度の切削油は、これらの切りくずをスムーズに洗い流し、再切削や噛み込みによるトラブルを防ぎます。
高温環境下で求められる「耐熱性・酸化安定性」
高速加工の加工点は、時には1000℃を超えるような高温に達することもあります。このような高温環境にさらされる切削油には、熱による劣化に耐える能力が不可欠です。
耐熱性とは
高温にさらされても、油剤の主成分や添加剤が熱分解を起こしにくい性質のことです。熱分解が起こると、スラッジ(油のカス)が生成されたり、潤滑性能や防錆性能が失われたりします。
酸化安定性とは
切削油は、高温下で空気中の酸素と反応し、酸化して劣化します。酸化が進行すると、油剤の粘度が上昇したり、酸性物質が生成されて機械を腐食させたり、スラッジが発生したりします。優れた酸化安定性とは、この酸化反応が起こりにくい性質を指します。
選び方のポイント
- ベースオイルの選定
化学的に安定した合成油(例:PAO、エステルなど)をベースとした切削油は、一般的に鉱物油よりも優れた耐熱性・酸化安定性を示します。 - 添加剤の配合
高性能な酸化防止剤や熱安定化剤が効果的に配合されている製品を選びます。
油性切削油と水溶性切削油のメリット・デメリットと選定ポイント
高速加工において、油性と水溶性のどちらを選ぶかは、加工の目的や条件によって異なります。
油性切削油
- メリット
- 優れた潤滑性・極圧性
境界潤滑状態になりやすい高速加工において、強力な油膜で工具を保護し、優れた仕上げ面を得るのに有利です。
- 優れた潤滑性・極圧性
- デメリット
- 冷却性能の低さ
水に比べて冷却能力が劣るため、大量の熱が発生する加工では、熱対策が課題となります。 - 引火・発煙のリスク
高温になると発煙しやすく、引火の危険性が高まります。 - コストと環境負荷
一般的に高価であり、作業環境のベタつきや廃油処理の観点でも不利な場合があります。
- 冷却性能の低さ
- 選定ポイント
潤滑性が最優先される難削材の高速仕上げ加工や、特定の工具(CBN工具など)で推奨される場合に、極めて低粘度で、かつ引火点が高く、酸化安定性に優れた専用の油性切削油を選定します。
水溶性切削油
- メリット
- 卓越した冷却性能
水を主成分とするため、極めて高い冷却能力を発揮し、高速加工での発熱を効果的に抑制します。 - 高い安全性
引火の危険性がほとんどありません。 - 洗浄性と汎用性
洗浄性が高く、切りくず排出に有利です。また、多くの加工に適用できます。
- 卓越した冷却性能
- デメリット
- 潤滑性の課題
油性に比べて潤滑性能が劣るため、添加剤技術でこれを補う必要があります。 - 腐敗管理
微生物が繁殖しやすいため、濃度管理やpH管理といった日常の液管理が重要になります。
- 潤滑性の課題
- 選定ポイント
高速加工では、冷却性を最優先し、ソリュブル型やシンセティック型が第一選択となります。その上で、潤滑性を高めるための特殊な添加剤が配合された高性能な製品や、高速回転・高圧供給でも泡立ちにくい低泡性に優れた製品を選ぶことが極めて重要です。
高速加工用の切削油選定は、まず低粘度と高い耐熱性という基本特性を押さえることが前提となります。その上で、潤滑性を最優先するなら油性、冷却性と汎用性を重視するなら水溶性という視点で、自社の加工に最適な油剤を見極めることが成功の鍵です。サンワケミカルでは、これらの要求に応える多様な高速加工用切削油をラインナップしており、専門的な知見から最適な製品選定をサポートします。
3. 高速加工に最適な切削油の供給方法(高圧、内部給油)
-1024x538.png)
高速加工で切削油の効果を最大限に引き出す供給方法は、遠心力に打ち勝って加工点に油剤を叩きつける「高圧クーラントシステム」と、刃先に直接油剤を供給する「工具内部給油(スルークーラント)」の活用が極めて有効です。これらを戦略的に組み合わせることで、冷却・潤滑・切りくず排出の全てを高いレベルで実現できます。
高性能な切削油を選定しても、それが最も重要な加工点に確実に届かなければ意味がありません。特に、高速で回転する工具は、その周囲に強力な遠心力と空気の流れ(エアバリア)を発生させ、外部から供給される切削油を弾き飛ばしてしまいます。この課題を克服し、切削油の効果を最大限に発揮させるための供給方法が不可欠です。
高圧クーラントシステムの有効性
なぜ高圧供給が必要か
通常のクーラント供給圧(0.2~0.5MPa程度)では、高速回転する工具のエアバリアを突破できず、切削油が刃先に到達する前に飛散してしまいます。高圧クーラントシステム(1MPa~7MPa、あるいはそれ以上)は、高い圧力で切削油を噴射することで、このエアバリアを突き破り、加工点に強制的に油剤を送り込むことができます。
高圧クーラントがもたらす効果
- 冷却・潤滑効果の劇的な向上
加工点へ確実に到達した切削油が、工具とワークを効果的に冷却・潤滑します。また、高圧で噴射される液体が気化する際に熱を奪う効果(キャビテーション冷却)も期待できます。 - 切りくず排出の促進
高圧の噴流が、生成された切りくずを物理的に吹き飛ばし、工具への絡みつきや再切削を防ぎます。特に、ポケット加工や溝加工で威力を発揮します。 - 切りくずの分断効果
高圧の噴流が切りくずに衝突することで、切りくずを細かく分断し、より排出しやすい形状にする効果(チップブレーキング効果)も期待できます。
工具内部給油(スルークーラント)の絶大な効果
なぜ内部給油が最適か
工具内部給油(スルークーラント、センタースルー)は、工具(ドリル、エンドミルなど)やツールホルダーの内部に設けられた油穴(オイルホール)を通じて、切削油を工具の先端(切れ刃近傍)から直接噴射する方式です。
内部給油がもたらす効果
- ダイレクトな冷却・潤滑
遠心力や切りくずの影響を全く受けずに、最も熱が発生し、最も潤滑が必要な刃先に直接ピンポイントで切削油を供給できます。これは、他のどの供給方法よりも効率的で確実です。 - ミスト発生の抑制
切削油が工具の回転によって周囲にまき散らされる前に加工点に到達するため、外部供給に比べてオイルミストの発生を大幅に抑制でき、作業環境の改善に大きく貢献します。 - 切りくず排出能力の最大化
工具の先端から噴出する液流が、切りくずを工具のフルート(溝)に沿って後方へスムーズに押し出します。
機械や工具の仕様に合わせた最適な供給方法の選び方
最適な供給方法は、加工内容だけでなく、使用する機械や工具の仕様によって決まります。
1. 機械の仕様を確認する
お使いのマシニングセンタがスピンドルスルークーラント機能や高圧クーラントユニットに対応しているかを確認します。対応していない場合は、後付けが可能か、あるいは外部からの高圧供給ユニットの導入を検討します。
2. 工具の選定
内部給油方式を利用するには、オイルホール付きの専用工具が必要です。工具メーカーのカタログなどで、加工内容に適した内部給油工具を選定します。
3. 供給方法の組み合わせ
- 基本
高速加工においては、「高圧」かつ「内部給油」の組み合わせが、最も高い効果を発揮する理想的な供給方法と言えます。 - 次善策
内部給油が使用できない場合は、外部から高圧で供給します。その際、ノズルの数、形状、位置を工夫し、できるだけ加工点に油剤が集中するように調整します。 - 仕上げ加工など
それほど高い負荷がかからない高速仕上げ加工では、ミストクーラント(MQL)も選択肢となりますが、潤滑性と切りくず処理能力の限界を理解した上で適用する必要があります。
まとめると、高速加工における切削油供給は、高圧クーラントと工具内部給油という二つの強力な武器を、機械や工具の仕様、そして加工の目的に合わせて戦略的に選択・組み合わせることが、そのポテンシャルを最大限に引き出すための秘訣と言えるのです。
4. 高速加工時の熱対策と切削油の温度管理
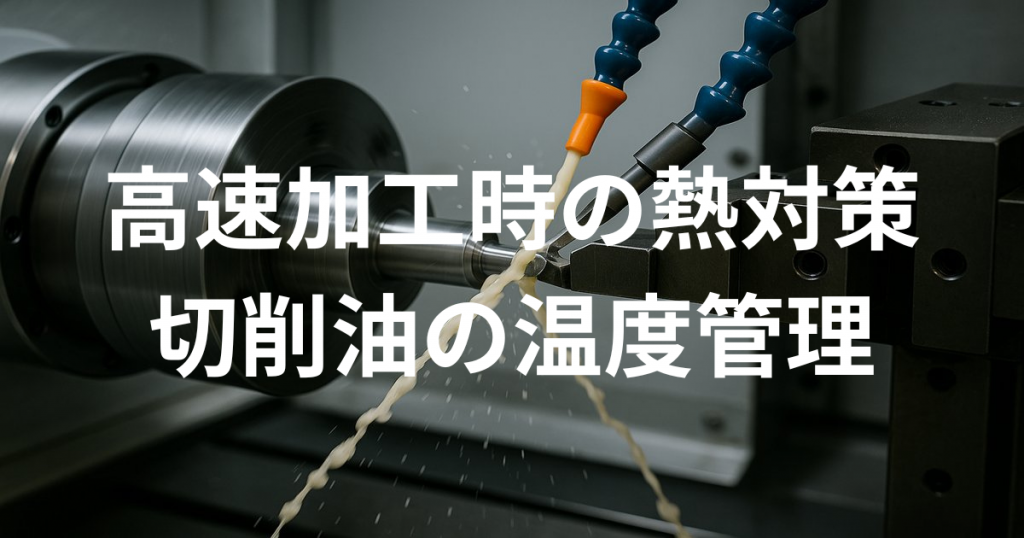
高速加工における熱対策の要は、発生した莫大な熱を切削油で効率的に除去すると同時に、熱を吸収して温度が上昇した切削油自体を低温で安定させることです。特に、クーラントチラーを導入して切削油の温度を積極的に管理することが、ワークの熱変形を防ぎ、工具寿命を延ばし、高精度な加工を長時間安定して実現するための最も直接的で効果的な手段となります。
高速加工では、その名の通り、極めて高い速度で金属を除去するため、単位時間あたりの発熱量が通常加工とは比較にならないほど増大します。この「熱」をいかに制するかが、高速加工の品質と安定性を左右する最大の課題であり、その中心的な役割を担うのが切削油です。
高速加工で発生する熱が加工精度や工具寿命に与える影響
加工精度への影響(熱変位)
発生した熱がワークピースに伝わると、ワークは熱膨張します。膨張した状態で加工されたワークは、加工後に冷却されて収縮するため、狙いの寸法よりも小さくなってしまうなどの寸法誤差(熱変位)が生じます。また、工作機械本体(主軸、ベッド、コラムなど)も熱影響を受けて変形し、機械全体の精度を狂わせる原因となります。長時間の連続加工では、この影響が蓄積し、加工開始時と終了時で寸法が大きくずれるといった問題が顕著になります。
工具寿命への影響
工具の切れ刃は、加工熱によって極めて高温の状態にさらされます。超硬工具といえども、その性能を発揮できる温度には限界があり、許容温度を超えると硬度が低下(軟化)し、塑性変形を起こしたり、酸化や拡散といった化学的な摩耗が急速に進行したりします。これにより、工具寿命は著しく短くなります。
切削油による効果的な熱対策の重要性
これらの熱問題を解決するために、切削油による効果的な熱対策が不可欠です。
- 高い冷却性能を持つ油剤の選定
前述の通り、冷却性に優れた水溶性切削油(ソリュブル型、シンセティック型)が基本となります。 - 十分な量の安定供給
大流量の切削油を加工点に供給し、発生した熱を間髪入れずに奪い去ります。 - しかし、これだけでは不十分な場合がある
長時間連続運転を行うと、クーラントタンク全体の液温が徐々に上昇していきます。液温が上昇した切削油では、もはや十分な冷却効果は期待できません。例えば、40℃の切削油と20℃の切削油では、加工点を冷却する能力に大きな差が出ます。
クーラントチラーによる切削油の温度管理の必要性
そこで重要になるのが、クーラントチラー(冷却装置)による積極的な温度管理です。クーラントチラーは、熱を吸収して温度が上昇した切削油を強制的に冷却し、タンク内の液温を常に一定に保つための装置です。
クーラントチラー導入のメリット
- 加工精度の安定化
切削油の温度を常に一定(例えば、室温と同じ、あるいは少し低い温度)に保つことで、ワークや機械の熱変位を最小限に抑え、長時間の連続加工でも安定した寸法精度を維持できます。 - 工具寿命の延長
常に冷却能力の高い状態の切削油を供給できるため、工具刃先の温度上昇を効果的に抑制し、工具寿命を延ばすことができます。 - 切削油の長寿命化
油温の上昇による酸化劣化を防ぎ、切削油自体の寿命も延ばすことができます。
適切な温度設定のポイント
- 目標温度
加工内容や要求精度、使用する機械によって異なりますが、一般的には室温と同等か、それよりわずかに低い温度に設定することが多いです。重要なのは、設定した温度を加工中常に維持し続けることです。 - 過度な冷却への注意
必要以上に温度を下げすぎると、エネルギーの無駄になるだけでなく、周囲の空気との温度差で機械や配管に結露が発生し、錆の原因となることもあるため注意が必要です。 - 温度制御精度
精密加工を行う場合は、温度制御精度の高い(例:±0.5℃や±0.1℃)インバータ制御式のチラーなどが推奨されます。
高速加工における熱問題は、加工精度と工具寿命に直結する最重要課題です。これを解決するためには、冷却性の高い切削油の選定と十分な供給に加え、クーラントチラーによる積極的な温度管理を行い、加工系全体の熱バランスを最適にコントロールすることが不可欠です。
5. 高速加工における加工精度と切削油管理のポイント

高速加工で高精度を実現するためには、これまで述べてきた熱対策に加え、微細な異物を排除する「清浄度管理」、加工点へ油剤を確実に届ける「安定供給」、そして加工中の微振動を抑制するための「適切な粘度選定」という、より高度な切削油管理を徹底することが不可欠です。これらが、最終的な加工品質を保証する土台となります。
高速加工の目的は、単に速く削ることだけではなく、「速く、かつ高精度に」削ることにあります。その高いレベルの要求に応えるためには、切削油の選定や供給方法だけでなく、日々の運用における総合的な管理が決定的に重要になります。
清浄度管理の重要性:微細な異物が品質を損なう
高速で回転する工具とワークの間では、切削油中に浮遊するμm(マイクロメートル)単位の微細な切りくずや異物ですら、加工面に高速で衝突し、スクラッチ傷や曇りといった面粗度悪化の原因となります。また、これらの異物は、工具の微細な切れ刃を摩耗させたり(アブレッシブ摩耗)、クーラント供給系のノズルや工具内部のオイルホールを詰まらせたりする原因ともなります。
- 対策
高速加工においては、加工で発生する微細な切りくずを効率的に除去できる、高性能なフィルターシステム(例:高精度カートリッジフィルター、サイクロンセパレーター、マグネットセパレーターと精密フィルターの組み合わせなど)の導入が重要です。また、混入油を除去するためのオイルスキマーの活用や、タンクの定期的な清掃も欠かせません。
安定した供給の重要性:油膜切れは許されない
高速加工中は、わずかな油剤供給の途切れや脈動も、潤滑・冷却の不安定に繋がり、加工品質のばらつきや工具のチッピングの原因となります。
- 対策
クーラントポンプの定期的な点検・メンテナンス、フィルターの目詰まり管理、配管からの漏れチェックなどを徹底し、常に安定した圧力と流量で切削油が供給される体制を維持します。液面レベルの管理も重要で、液面低下によるポンプのエア吸い込みなどを防ぐ必要があります。
微振動(チャター)を抑制するための切削油の粘度選定と機械剛性
高速加工では、加工システム全体のわずかな剛性不足が、びびり振動(チャター)と呼ばれる自励振動を引き起こしやすくなります。これは、加工面に周期的な模様(びびりマーク、チャターマーク)を残し、面粗度を著しく悪化させます。
- 切削油の粘度選定
切削油の粘度は、この微振動を抑制する「減衰性(ダンピング効果)」にも影響します。一般的に、ある程度の粘度を持つ切削油は、油膜のクッション効果により振動を吸収しやすい傾向があります。しかし、高速加工では冷却性や浸透性を高めるために低粘度油剤が有利とされます。したがって、びびり振動の抑制と、高速加工への適合性という二つの要素を両立できる、最適な粘度範囲の切削油を選定することが求められます。 - 機械剛性の重要性
びびり振動の最も根本的な原因は、工作機械本体、工具ホルダー、工具、ワークのクランプといった加工システム全体の剛性不足です。切削油による対策はあくまで補助的なものであり、びびりが頻発する場合は、工具の突き出し量を短くする、より剛性の高いホルダーを使用する、切削条件(切削幅、送り、回転数)を見直すといった、機械的な対策が不可欠です。
高速かつ高精度な加工を実現するためには、油剤選定や供給方法だけでなく、日々の運用における清浄度、温度、供給安定性といった地道な管理が決定的に重要になります。これらの総合的な管理体制が、マシニングセンタの性能を最大限に引き出し、安定した高品質な生産を可能にするのです。
まとめ
本記事では、高速加工において、そのメリットである「高効率」と、製品に求められる「高品質」を高いレベルで両立させるための、切削油の選び方、供給方法、そして管理のポイントについて、多角的な視点から詳しく解説してまいりました。
高速加工における切削油は、通常加工以上に、
- 発生する莫大な熱を的確に除去する「冷却性能」
- 高速回転下でも油膜切れを起こさない「潤滑性能」
- 作業環境と安全を守るための「低ミスト性」といった、より高度で特殊な性能が求められます。
そして、その性能を最大限に引き出すためには、「低粘度」で「耐熱性・酸化安定性」に優れた油剤を選定し、「高圧クーラント」や「工具内部給油」といった最適な供給方法を適用し、さらに「温度管理」「清浄度管理」といった日々の徹底した管理を行うことが不可欠です。
高速加工のポテンシャルは計り知れませんが、それを引き出すも殺すも、切削油の活用次第と言っても過言ではありません。この記事でご紹介した内容を参考に、ぜひ皆様の現場でも切削油の運用を見直し、より高い次元の生産性を実現してください。
もし、高速加工における切削油の選定や、現在発生しているトラブル(工具摩耗、加工精度不良、オイルミストなど)の解決にお困りでしたら、どうぞお気軽に私たちサンワケミカル株式会社にご相談ください。長年の経験と最新の技術に基づき、お客様の課題解決に貢献できる最適なソリューションをご提案させていただきます。
サンワケミカル株式会社は、長年の経験と技術に基づき、多種多様な切削油剤を開発・製造しております。お客様の加工条件やニーズに合わせた最適な製品をご提案いたしますので、切削油に関するご相談は、ぜひお気軽にお問い合わせください。
もし、この記事で紹介した対策を試しても問題が解決しない場合や、お使いの切削油に関するより詳細な情報、お客様の特定の加工に最適な油剤の選定についてご相談がありましたら、どうぞお気軽に私たちサンワケミカル株式会社までお問い合わせください。経験豊富な専門スタッフが、お客様の状況を詳しくお伺いし、最適なソリューションをご提案いたします。
サンワケミカル株式会社HP:http://sanwachemical.co.jp/
サンワケミカル株式会社お問い合わせ:http://sanwachemical.co.jp/contact/
サンワケミカル株式会社公式X:https://x.com/sanwachemical
今後も、金属加工の現場で役立つ情報を発信してまいりますので、サンワケミカル株式会社公式ブログにご期待ください。