【精密加工における切削油管理】ミクロン単位の高精度を実現する極意と実践法
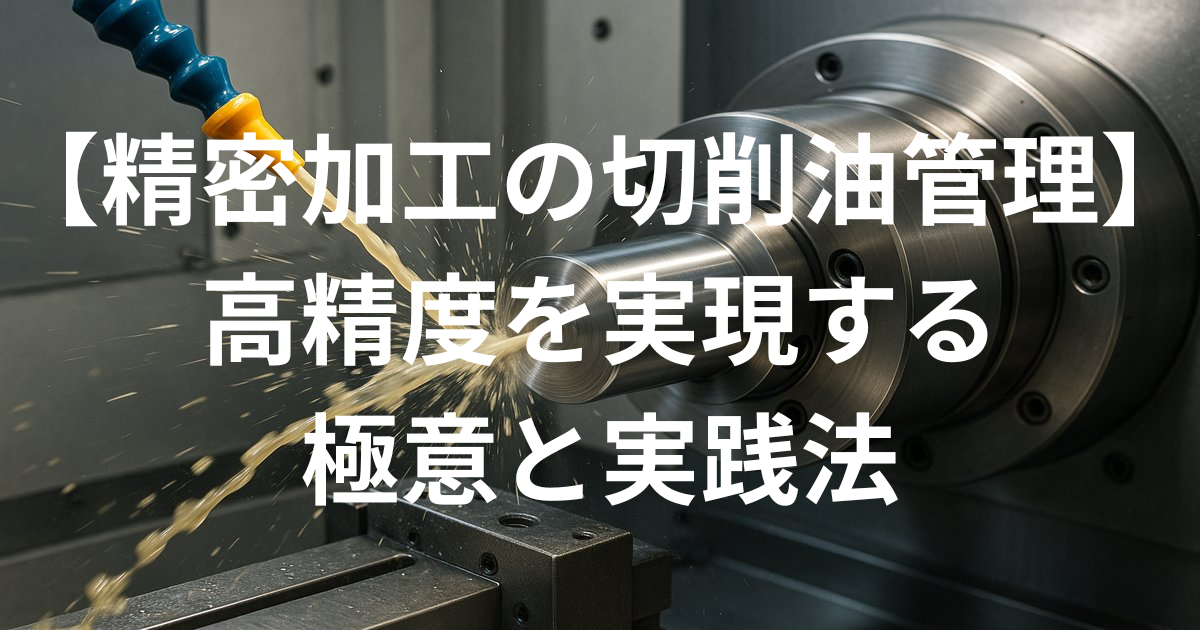
金型、光学部品、医療機器、半導体製造装置など、最先端の技術分野で求められるのは、もはや「良い品質」というレベルを超えた、ミクロン(1/1000mm)単位、時にはサブミクロン単位の「極限の精度」です。この超精密なものづくりを実現するため、工作機械の性能、工具の選定、加工環境の整備など、あらゆる要素に最高レベルの配慮が払われています。しかし、その中で、その成否を最終的に左右するにも関わらず、その真の重要性が見過ごされがちなのが切削油の管理です。
「なぜか寸法が安定しない」「仕上げ面のわずかな曇りや傷が解消できない」「高価な精密工具の寿命が思ったより短い」…これらの課題は、実は切削油の管理状態に起因しているケースが少なくありません。精密加工の世界では、切削油は単なる潤滑・冷却媒体ではなく、加工環境そのものをミクロン単位で制御する「超精密な機能流体」としての役割を担います。
この記事では、精密加工の成否を分ける「神髄」とも言える切削油管理に焦点を当て、その特殊な役割から、求められる高度な性能、具体的な選び方、そして徹底した管理の実践法まで、精密加工の品質と安定性を飛躍的に向上させるための「極意」を余すところなく解説いたします。
1. 精密加工における切削油の役割と要求される性能
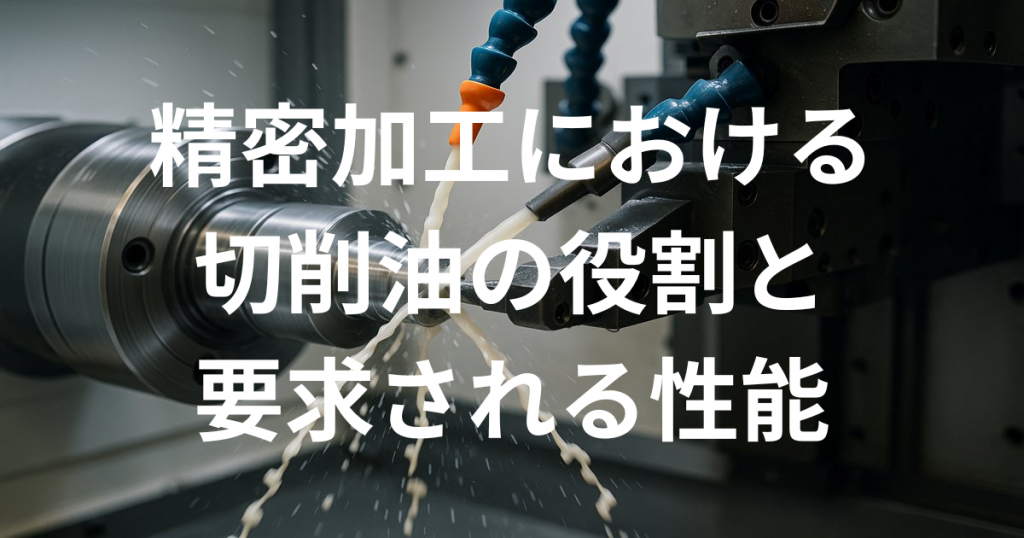
精密加工における切削油の役割は、単なる潤滑・冷却に留まりません。加工系全体の熱的・物理的バランスをμm単位で安定させるための「超精密な環境制御媒体」として機能することが求められます。わずかな温度変化やμm単位の異物が致命的な欠陥に繋がるため、切削油には極めて高度な性能が不可欠です。
極めて高い寸法精度、表面粗度、そして形状精度が要求される精密加工の世界では、切削油は一般的な切削加工とは比較にならないほど高度で繊細な役割を果たさなければなりません。
微細な潤滑作用
ナノレベルの表面創成
精密加工における仕上げ工程では、切り込み量は極めて小さく、ナノメートル(1nm = 1/1000μm)レベルの表面形状を創り出していきます。この領域では、工具の切れ刃とワーク表面の間に、極めて薄く、かつ強靭で均一な潤滑膜を形成し続けることが求められます。この「微細な潤滑」が不十分だと、加工面に微細なむしれや引きずり傷が発生し、要求される鏡面のような表面粗度は得られません。
精密な冷却作用
μm単位の熱変位制御
精密加工において、最大の敵の一つが「熱変位」です。加工中に発生するわずかな熱が、ワーク、工具、そして工作機械本体をμm単位で膨張・収縮させ、これが加工誤差として直接現れます。切削油には、この微細な熱の発生を抑制し、かつ発生した熱を速やかに、そして極めて安定した状態で除去し、加工系全体の温度を厳密に一定に保つ「精密な冷却」能力が不可欠です。
徹底的な切りくず排出(洗浄作用)
微細な異物の完全排除
精密加工で発生する切りくずは、極めて微細な粒子状(スラッジ)です。これらの微細な粒子ですら、加工面に再付着したり、工具とワークの間に噛み込まれたりすると、致命的なスクラッチ傷の原因となります。切削油には、これらの微細な切りくずを発生と同時に加工点から完全に洗い流し、再循環させないための「徹底的な洗浄・排出」能力が求められます。
完璧な腐食防止作用
加工面の品質維持
精密に仕上げられた加工表面は、化学的にも非常に活性な状態です。わずかな錆や変色も、製品の性能や外観品質を損なう致命的な欠陥となります。切削油には、加工中および加工後のワーク表面を、腐食因子から完全に保護する「完璧な防錆」性能が要求されます。
このように、精密加工における切削油は、一般的な加工で求められる性能を、さらに数段高いレベルで、かつ極めて安定して発揮することが求められる、まさに「縁の下の最高技術」と言える存在なのです。
まとめると、精密加工における切削油は、加工現象をマクロな視点で支えるだけでなく、熱変位、微細な傷、化学変化といったミクロなレベルでの不安定要因を徹底的に排除する、極めて高度な役割を担っているのです。
2. 高精度加工に適した切削油の選び方(低粘度、高清浄度)
-1024x538.png)
高精度加工に適した切削油選びの極意は、「超低粘度」による優れた浸透性と洗浄性、そして加工精度を直接左右する「究極の高清浄度」を基本とします。さらに、特殊な添加剤によって、表面張力のコントロールといった微細領域での物理現象を最適化することが求められます。
精密加工の厳しい要求に応えるためには、切削油そのものにも特別な性能が求められます。ここでは、その選定における重要なポイントを解説します。
低粘度の有効性
なぜ低粘度が有利か
精密加工では、工具とワークのクリアランス(隙間)が極めて狭くなります。また、微細な切りくず(スラッジ)を効率よく除去する必要があります。
- 浸透性
粘度が低い(サラサラした)切削油は、毛細管現象により、このような微細な隙間にも迅速に浸透し、最も重要な切れ刃先端まで確実に到達して潤滑・冷却効果を発揮します。 - 洗浄性
低粘度油剤は流動性が高いため、微細なスラッジを加工点から速やかに洗い流し、砥石の目詰まり(研削加工の場合)や加工面への再付着を防ぎます。 - 抵抗の低減
粘性抵抗が小さいため、工具の回転や移動に対する抵抗が少なく、微細な加工における動力損失や不要な発熱を抑えることができます。
高清浄度の必要性
なぜ高清浄度が必要か
精密加工の仕上げ面では、数μmの異物ですら致命的なスクラッチ傷の原因となります。一般的な切削油には、製造過程や保管中に混入した微細な異物が含まれている可能性があります。
- 対策
精密加工で使用する切削油は、納入前に高精度フィルターで精密ろ過処理が施された、極めて清浄度の高い製品を使用することが不可欠です。油剤メーカーに対して、納入時の清浄度レベル(NAS等級やISO等級など)を指定、あるいは保証してもらうことも重要です。
特殊な添加剤の役割
物理現象をミクロに制御
精密加工用切削油には、基本的な潤滑剤や極圧剤に加え、より高度な機能を発揮するための特殊な添加剤が配合されることがあります。
- 表面張力調整剤
切削油の表面張力をコントロールすることで、ワーク表面への「濡れ性」を向上させ、より均一で薄い油膜を形成したり、微細な気泡の発生を抑制したりします。これにより、潤滑・冷却の安定性が向上します。 - 特殊油性向上剤・摩擦調整剤
合成エステルや特殊ポリマーなど、極めて高い潤滑性を持ち、かつ熱安定性に優れた添加剤が、境界潤滑領域での摩擦を極限まで低減し、鏡面のような仕上げ面を実現するのに貢献します。
高精度加工用の切削油選定は、まず低粘度と高清浄度という大前提を満たすことが不可欠です。その上で、表面張力調整剤のような特殊添加剤を適切に活用することで、物理現象をミクロレベルで制御し、更なる精度向上を目指すことができます。サンワケミカルでは、これらの厳しい要求に応える精密加工専用油剤の開発・提供を行っております。
3. 精密加工のための切削油供給と温度管理の徹底
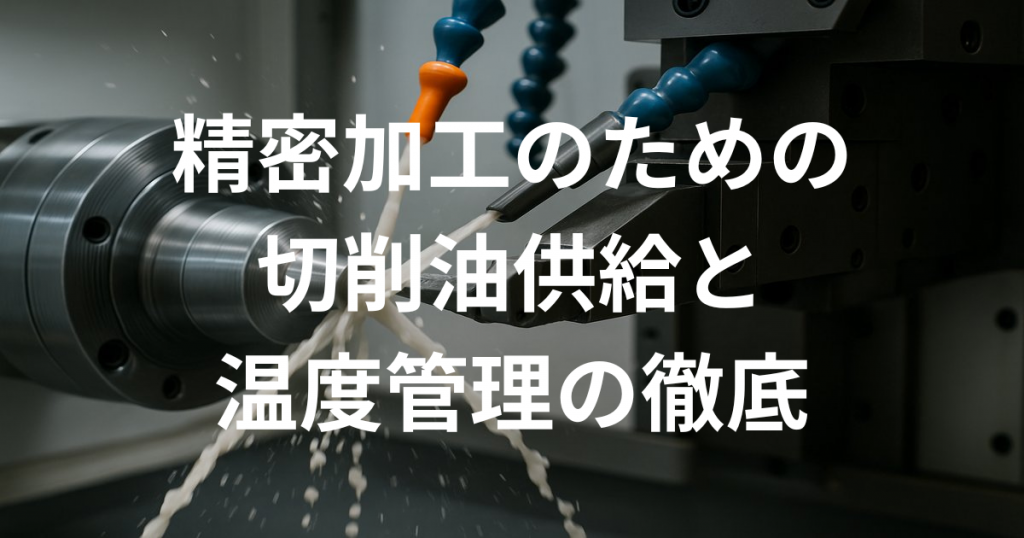
精密加工を成功させる供給・温度管理の鍵は、「必要な場所に、必要なだけを、正確に供給する技術」と、加工系全体の熱変位を完全に抑制する「厳密な温度管理」の二つです。これらは、高精度チラーや精密ノズル、MQL(微量給油)といった専用技術によって実現されます。
最高性能の精密加工用切削油を選定しても、その供給方法や温度管理が不適切であれば、宝の持ち腐れとなってしまいます。ここでは、切削油の効果を最大限に引き出すための、運用面での極意を解説します。
微細な加工点への正確な切削油供給方法
微量給油(MQL:Minimum Quantity Lubrication)
ごく微量の切削油を圧縮空気と混合してミスト状にし、加工点にピンポイントで供給する方法です。ウェット供給(かけ流し)による大量の液体の表面張力や粘性抵抗が、微細工具の挙動に悪影響を与えることを避けたい場合に特に有効です。ワークの熱影響が少なく、加工後の洗浄が容易というメリットもありますが、潤滑能力や切りくず排出能力には限界があるため、適用には加工内容の見極めが必要です。
精密ノズルの活用
ウェット供給を行う場合でも、ノズルの選定と配置が極めて重要です。
- ノズル形状
加工点の微細な領域に集中して供給できる極細ノズルや、均一な液膜を形成できるフラットノズルなどを、加工内容に応じて使い分けます。 - ノズル位置と角度
工具の回転やワーク形状による液の流れを計算し、最も効果的に冷却・潤滑・洗浄が行える位置と角度に、ミクロン単位で精密に調整します。複数のノズルを異なる角度から供給することも有効です。
厳密な切削油の温度管理の重要性
なぜ厳密な管理が必要か
前述の通り、精密加工における最大の敵は「熱変位」です。ワーク、工具、機械本体のわずかな温度変化(1℃の変化でも数μmの変位に繋がる)が、加工精度を直接的に狂わせます。したがって、加工系全体の温度を厳密に一定に保つことが絶対条件となります。
高精度チラーの利用
これを実現する最も効果的な手段が、高精度なクーラントチラー(冷却装置)の導入です。
- 目標とする制御精度
精密加工の現場では、切削油の温度を±0.5℃、あるいは±0.1℃といった極めて高い精度で制御できるインバータ式などの高性能チラーが使用されます。 - 設定温度
一般的には、恒温管理された室温と同等、あるいはわずかに低い温度に設定し、加工中常にその温度を維持し続けます。これにより、加工系全体の熱的平衡を保ち、熱変位を最小限に抑制します。 - 断熱対策
チラーの効果を最大化し、外部からの熱影響を遮断するために、クーラントタンクや配管に徹底した断熱対策を施すことも非常に重要です。
精密加工における切削油の運用は、MQLや精密ノズルによる的確な供給技術と、高精度チラーによる徹底した温度管理という両輪を回すことが不可欠です。これにより、加工点での物理的・熱的環境を理想的な状態に保ち、安定した高精度加工が可能になります。
4. 微細な切りくず、異物対策と高度な清浄度管理
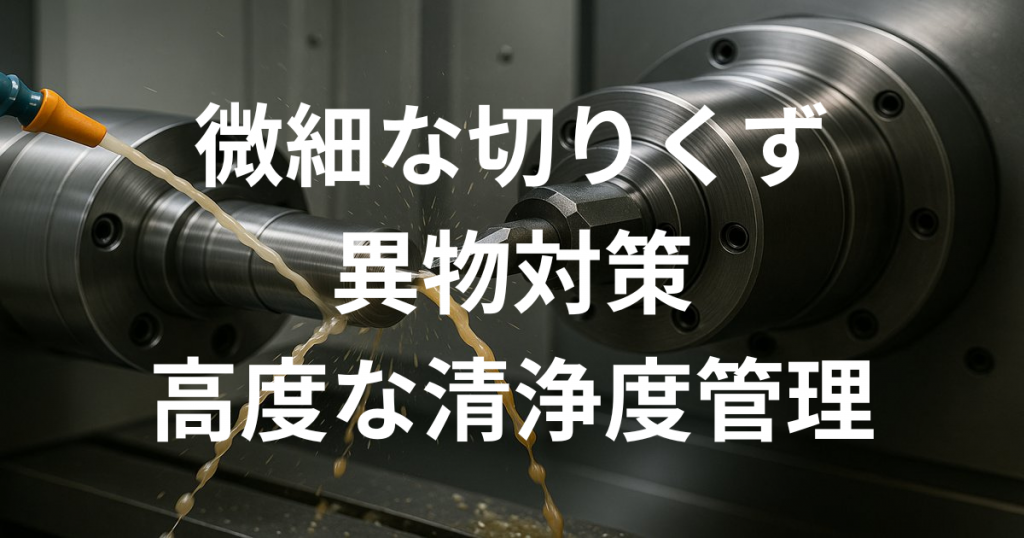
精密加工における清浄度管理は、単にフィルターを設置するだけでは不十分です。μmオーダー、時にはサブミクロン単位の微細な異物をシステム全体で徹底的に排除することが核心であり、高性能フィルターの多段活用、タンクの密閉化、そして定期的な油剤分析による予防保全が不可欠となります。
精密加工の品質は、使用する切削油の「清浄度」に直結すると言っても過言ではありません。ここでは、究極のクリーンさを維持するための具体的な対策について解説します。
精密加工で発生する微細な切りくずや外部からの異物混入を徹底的に防ぐ対策
高性能フィルターシステムの戦略的導入
1. 超精密ろ過の必要性
精密加工では、一般的な加工で使用されるフィルターでは捕捉できない、数μm以下の微細な切りくず(スラッジ)や摩耗粉が加工精度に悪影響を与えます。そのため、絶対ろ過精度で5μm以下、要求によっては1μmやサブミクロンレベルの粒子まで除去できる、高性能な精密フィルター(例:高精度カートリッジフィルター、メンブレンフィルターなど)の導入が必須です。
2. 多段ろ過の有効性
比較的大きな異物を除去するプレフィルター(例:マグネットセパレーターや粗目のバッグフィルター)と、微細な粒子を除去するメインの精密フィルターを組み合わせる「多段ろ過」方式は、メインフィルターの負荷を軽減し、その寿命を延ばしつつ、効率的に高い清浄度を達成するために非常に有効です。
3. フィルターの適切なメンテナンス
どんなに高性能なフィルターも、目詰まりしては意味がありません。差圧計による管理を徹底し、最適なタイミングで計画的にエレメント交換や清掃を行うことが重要です。
汚染源を断つための環境対策
1. 密閉型タンクとクリーンエア供給
外部からのホコリや浮遊粒子の混入を防ぐため、クーラントタンクは可能な限り密閉構造とし、必要であればタンク内部をクリーンエアでわずかに陽圧に保つといった対策も有効です。
2. 油剤の補充・交換時の注意
新しい油剤を補充する際や、全量交換する際にも、クリーンな容器やポンプを使用し、異物が混入しないように細心の注意を払います。補充する新油自体も、使用前に精密ろ過することが望ましい場合もあります。
定期的な切削油の分析と交換の重要性
なぜ分析と交換が必要か
長期間使用するうちに、切削油はフィルターでは除去しきれない超微細な粒子や、溶解性の劣化生成物、化学変化による成分の変質など、目に見えないレベルで劣化が進行します。この劣化が、潤滑性能の低下や腐食性の増大などを引き起こし、加工精度に悪影響を与える可能性があります。
1. 定期的な油剤分析(コンタミネーションチェック)
パーティクルカウンターによる汚染度(清浄度レベル)の測定、顕微鏡による異物観察、含有水分量、全酸価、成分分析などを定期的に行い、切削油の健康状態を客観的なデータで把握します。
2. 計画的な交換
これらの分析結果に基づき、油剤の性能が許容限界に達する前に、計画的に全量交換を実施します。「まだ使えるだろう」という感覚的な判断ではなく、データに基づいた予防保全的な交換が、安定した品質を維持する鍵となります。
精密加工の品質は、切削油の清浄度に直結します。高性能フィルターの戦略的な導入と、タンク自体の汚染防止対策、そして油剤分析に基づいた計画的な交換という、包括的かつ徹底した清浄度管理体制を構築することが極めて重要です。
5. 精密加工におけるトラブルシューティングと切削油の関連性

精密加工で発生するトラブル(寸法不良、面粗度不良など)の多くは、切削油の管理状態(清浄度、温度、潤滑性)のわずかな変化に起因します。トラブルシューティングの鍵は、これらの管理状態を精密に分析し、現象の背後にある根本原因を特定して、油剤の選定や管理方法を最適化することにあります。
どれほど徹底した管理を行っていても、予期せぬトラブルが発生することはあります。ここでは、精密加工で起こりやすい代表的なトラブルと、切削油の観点からの原因分析・対策について解説します。
寸法不良(ばらつき、経時変化)と切削油の関連性
考えられる原因
- 温度管理の不備
切削油の温度が不安定で、ワークや機械の熱変位量が変動している。 - 潤滑性能のばらつき
切削油の濃度変化や劣化により潤滑性が不安定になり、切削抵抗が変動して工具のたわみ量などが変化する。 - 清浄度の低下
微細な異物が工具刃先に付着し、実質的な切削径が微小に変化する。
切削油からの対策
- 温度管理の再点検
チラーの設定と実際の油温の乖離、タンク内での温度ムラ、配管の断熱状態などを確認し、厳密な温度制御を徹底します。 - 濃度管理の徹底
自動濃度管理装置の導入や、手動での測定頻度を上げて、濃度を常に一定に保ちます。 - 清浄度管理の強化
フィルターのろ過精度を見直す、交換頻度を早める、あるいはより高性能なろ過システムを導入します。
面粗度不良(スクラッチ傷、曇り、むしれ)と切削油の関連性
考えられる原因
- 清浄度の低下
油剤中に浮遊するμm単位の硬質粒子が、加工面に微細なスクラッチ傷を付ける。 - 潤滑不足
潤滑膜が破れ、金属同士が微小に接触することで、加工面が曇ったり、むしれたりする。 - 切りくず排出不良
微細な切りくずが加工面に再付着したり、引きずられたりする。 - 化学的要因
油剤成分がワーク表面と反応し、シミや変色(曇り)の原因となる。
切削油からの対策
- 究極の清浄度追求
ろ過システムの抜本的な見直し(サブミクロンレベルのフィルター導入など)を検討します。 - 潤滑性能の高い油剤への変更
より低粘度で浸透性が高く、かつ特殊な油性向上剤が配合された精密加工専用油剤を試します。 - 供給方法の最適化
ノズルの位置や角度を再調整し、洗浄効果を高めます。 - 油剤と被削材の適合性再評価
ワーク材質に対して化学的に不活性な油剤を選定します。
工具摩耗の早期発生と切削油の関連性
考えられる原因
- 潤滑不足
切れ刃の摩耗が、想定よりも早く進行する。 - 冷却不足
切れ刃が高温になり、熱的な摩耗(酸化、拡散)が促進される。 - 清浄度の低下
油剤中の硬質粒子が、アブレッシブ摩耗(物理的な削り取り摩耗)を引き起こす。
切削油からの対策
- 潤滑・冷却バランスの最適化
現在の加工に対し、潤滑と冷却のどちらがより支配的かを見極め、それに合わせて油剤の特性(油性/水溶性、粘度、添加剤)を再選定します。 - 清浄度管理の強化
油剤中の摩耗性粒子を徹底的に除去します。 - 油剤の劣化診断
定期的な油剤分析により、潤滑添加剤の消耗や酸化劣化の進行度合いを確認し、性能が低下していれば交換します。
トラブルシューティング事例
ある精密部品メーカーでは、超硬工具による鏡面仕上げ加工で、原因不明の微細なスクラッチ傷に悩まされていました。切削油の管理は行っていましたが、サンワケミカルで油剤を分析したところ、1~3μmの微細なアルミナ系粒子(外部からの混入と推定)が多数検出されました。そこで、ろ過システムを従来の10μmから1μmの絶対ろ過精度を持つ高精度フィルターに変更し、油剤のタンクへの補充手順も見直したところ、スクラッチ傷が劇的に減少し、歩留まりが大幅に向上しました。
精密加工におけるトラブルシューティングは、現象の背後にある切削油の清浄度、温度、潤滑性といった根本要因にまで遡って分析することが不可欠です。油剤の選定や管理方法の最適化が、多くの問題を解決する糸口となります。
まとめ
本記事では、ミクロン単位の究極の精度が求められる「精密加工」において、その加工の成否を分けると言っても過言ではない、切削油管理の極意と具体的な実践法について、多角的な視点から詳しく解説してまいりました。
精密加工における切削油は、一般的な加工で求められる役割を遥かに超え、
- 微細な潤滑によってナノレベルの表面を創り出し、
- 精密な冷却によってμm単位の熱変位を抑制し、
- 徹底的な切りくず排出と完璧な防錆によって加工品質を保護する、 という、極めて高度で繊細な役割を担っています。
この役割を最大限に発揮させるためには、「低粘度」と「高清浄度」を基本とした最適な油剤を選定し、MQLや精密ノズル、高精度チラーといった技術を駆使して供給方法と温度管理を徹底し、さらに高性能フィルターや定期的な分析を通じて究極の清浄度を維持し続けることが不可欠です。これらの高度な切削油管理を実践することで、精密加工における品質と歩留まりを飛躍的に向上させることが可能となります。
もし、現在挑戦されている精密加工で、解決の難しい品質課題(寸法ばらつき、面粗度不良など)や、トラブル(工具の早期摩おなど)にお悩みでしたら、ぜひ一度、私たちサンワケミカル株式会社にご相談ください。私たちは、精密加工の厳しい要求に応えるための高性能な切削油剤のご提案はもちろんのこと、お客様の加工環境全体を視野に入れた、最適な管理体制の構築まで、トータルでサポートさせていただきます。
サンワケミカル株式会社は、長年の経験と技術に基づき、多種多様な切削油剤を開発・製造しております。お客様の加工条件やニーズに合わせた最適な製品をご提案いたしますので、切削油に関するご相談は、ぜひお気軽にお問い合わせください。
もし、この記事で紹介した対策を試しても問題が解決しない場合や、お使いの切削油に関するより詳細な情報、お客様の特定の加工に最適な油剤の選定についてご相談がありましたら、どうぞお気軽に私たちサンワケミカル株式会社までお問い合わせください。経験豊富な専門スタッフが、お客様の状況を詳しくお伺いし、最適なソリューションをご提案いたします。
サンワケミカル株式会社HP:http://sanwachemical.co.jp/
サンワケミカル株式会社お問い合わせ:http://sanwachemical.co.jp/contact/
サンワケミカル株式会社公式X:https://x.com/sanwachemical
今後も、金属加工の現場で役立つ情報を発信してまいりますので、サンワケミカル株式会社公式ブログにご期待ください。