【品質向上】切削油の清浄度管理入門|フィルタリングの基礎と実践テクニック
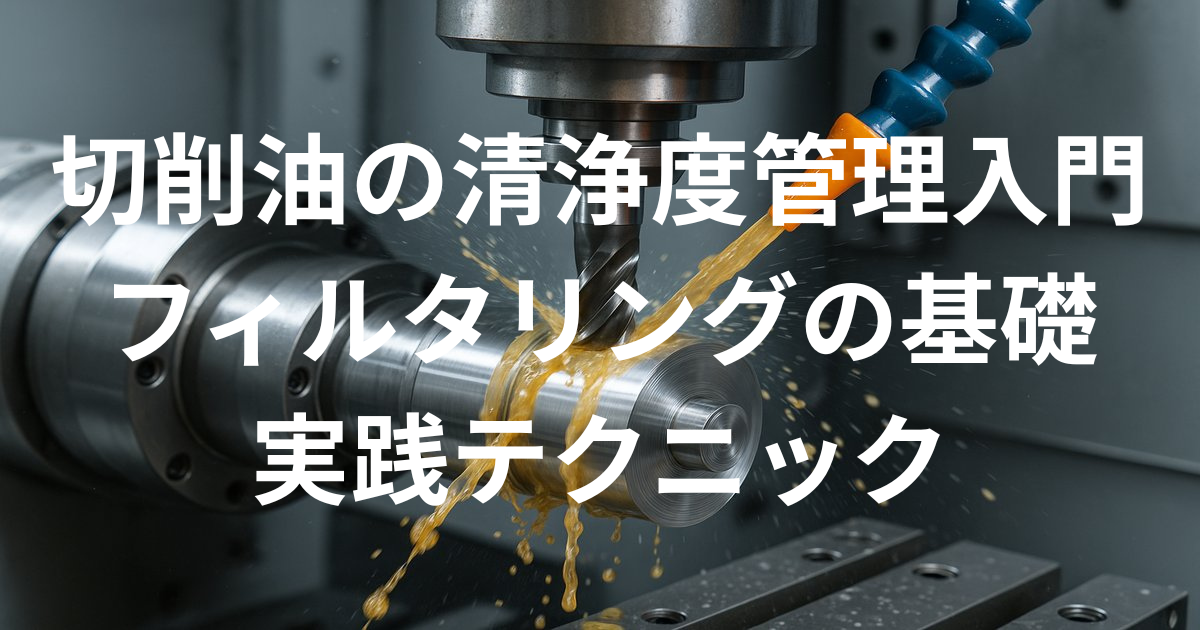
機械加工において、切削油は潤滑、冷却、切りくず排出といった重要な役割を担っています。しかし、その性能を最大限に発揮させるためには、切削油を常に「きれいな状態」、すなわち高い清浄度に保つことが不可欠です。「切削油がすぐに汚れてしまう」「フィルターは付けているけど、効果があるのか分からない」「清浄度が加工品質にどう影響するの?」…そんな疑問をお持ちの現場担当者の方も多いのではないでしょうか。
切削油の清浄度管理は、単に油剤をきれいに見せるためだけではありません。加工精度や面粗度の向上、工具寿命の延長、さらには機械トラブルの防止や油剤寿命の延長にも直結する、極めて重要な管理項目なのです。この記事では、切削油の清浄度管理の基本から、その核となるフィルタリング技術の種類と特徴、適切なフィルターの選び方、そしてさらに管理レベルを向上させるための実践的なテクニックまでを、分かりやすく解説します。
1. なぜ切削油の清浄度管理が重要なのか?

切削油は、使用しているうちに様々な不純物が混入し、徐々に汚れていきます。この「汚れ」、つまり清浄度の低下が、加工プロセス全体に様々な悪影響を及ぼします。
不純物が引き起こす主な問題点
- 加工精度・面粗度の悪化
- 切削油中に浮遊する微細な切りくず、砥粒、機械摩耗粉などの硬い粒子が、加工中のワーク表面と工具の間に入り込み、スクラッチ傷や引きずり痕を発生させ、面粗度を悪化させます。
- これらの粒子が工具の切れ刃に付着すると、切れ味が低下し、むしれやバリの原因となります。
- 構成刃先の核となり、その不安定な生成・脱落が寸法精度のばらつきや面粗度不良を引き起こします。
- 工具寿命の低下
- 硬い粒子が工具刃先を物理的に削り取るアブレッシブ摩耗を促進し、工具寿命を大幅に縮めます。
- 微細な切りくずが工具のチップポケットに詰まったり、刃先に絡みついたりして、チッピング(微小欠損)や突発的な工具破損の原因となります。
- 機械の故障・トラブル
- フィルターが早期に目詰まりし、交換頻度が増加します。
- フィルターを通過した微細な粒子がクーラントポンプ内部に入り込み、ポンプの摩耗や損傷、焼き付きを引き起こします。
- クーラント供給配管やノズルが詰まり、加工点への適切なクーラント供給が妨げられ、冷却・潤滑不足を招きます。
- 機械の摺動面やボールねじなどに粒子が侵入し、摩耗を促進させ、機械精度の低下や故障の原因となります。
- センサー類(液面センサー、流量センサーなど)の誤作動を引き起こすことがあります。
- 切削油の劣化促進
- 金属粉(特に銅など)は、切削油の酸化を促進する触媒として作用し、油剤の劣化を早めます。
- 混入した異物は、バクテリアやカビなどの微生物の温床となり、腐敗や悪臭の原因となります。
- 粒子が切削油中の有効な添加剤(防錆剤、極圧剤など)を吸着し、その効果を低下させることがあります。
清浄度を維持することによるメリット
逆に、適切なフィルタリングなどによって切削油の清浄度を高く維持することで、以下のような大きなメリットが得られます。
- 品質向上
加工精度が安定し、要求される面粗度を達成しやすくなります。不良率の低減に繋がります。 - コスト削減
工具寿命が延長され、工具費と交換の手間が削減されます。機械の故障が減り、修理費用やダウンタイムロスが削減されます。切削油の劣化が抑制され、交換頻度が減り、油剤コストと廃液処理コストが削減されます。 - 安定生産
機械トラブルによる突発的な停止(チョコ停)が減少し、計画通りの生産が可能となり、工場全体の稼働率向上に貢献します。
このように、切削油の清浄度管理は、高品質な製品を効率的かつ低コストで生産するための、非常に重要な基盤となるのです。
2. 切削油中の主な不純物とその影響
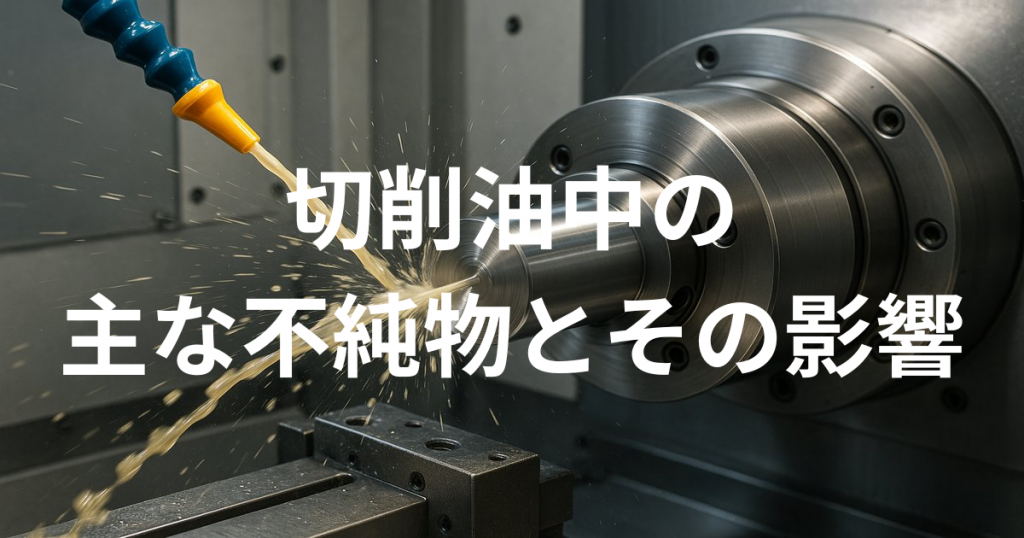
切削油を汚染する不純物には様々な種類があり、その発生原因も異なります。主な不純物とその影響を理解しておくことが、効果的な対策を講じる第一歩です。
切削油中の不純物
- 切りくず(チップ、切粉)
- 発生原因
被削材(ワーク)を切削・研削する過程で必ず発生します。材質(鉄、アルミ、ステンレス、鋳物など)や加工方法(旋削、フライス、穴あけ、研削など)、工具の種類によって、形状、大きさ、硬さが異なります。 - 影響
大きな切りくずはフィルターで比較的容易に除去できますが、微細なものはフィルターを通過しやすく、加工面への傷、工具摩耗、ポンプや配管の詰まり・摩耗の原因となります。特に鋳物や脆性材の加工では、微細な粉状の切りくずが多く発生します。
- 発生原因
- 砥粒(グラインディングスラッジ)
- 発生原因
研削加工で使用される砥石(砥粒と結合剤で構成)が摩耗・破砕して発生します。砥粒自体(アルミナ、炭化ケイ素、CBN、ダイヤモンドなど)は非常に硬い粒子です。 - 影響
極めて硬いため、工具や機械部品に対する摩耗性が非常に高く、深刻なダメージを与える可能性があります。加工面へのスクラッチ傷の主原因の一つです。
- 発生原因
- 機械摩耗粉
- 発生原因
工作機械の摺動面、ギア、ベアリングなどの摩耗によって発生する微細な金属粉です。 - 影響
硬い金属粒子であり、切りくずや砥粒と同様に、加工面への傷、工具摩耗、機械部品のさらなる摩耗を促進します。切削油の酸化触媒ともなり得ます。
- 発生原因
- 微生物(バクテリア、カビ、酵母)
- 発生原因
空気中、希釈水、作業者の手などから混入し、切削油中の有機成分や混入油、添加剤などを栄養源として、適度な温度(20~40℃程度)と水分(水溶性の場合)の条件下で増殖します。 - 影響
- 悪臭
特有の腐敗臭(ドブ臭、硫黄臭など)やカビ臭を発生させ、作業環境を悪化させます。 - pH低下
代謝物として酸を生成し、切削油のpHを低下させ、防錆性能を著しく損ないます。 - 性能低下
切削油の乳化状態を破壊したり、有効成分を分解したりして、潤滑性や冷却性を低下させます。 - フィルター目詰まり
増殖した微生物の塊や、それらが生成するネバネバした粘性物質(バイオフィルム、スライム)がフィルターを詰まらせます。 - 健康被害
皮膚炎やアレルギーの原因となることがあります。
- 悪臭
- 発生原因
- 混入油(浮上油、トランプオイル)
- 発生原因
工作機械の摺動面潤滑油、油圧作動油、スピンドル油、防錆油などが、シール不良やメンテナンス不足によりクーラントタンク内に漏れ出して混入します。 - 影響:
- 性能低下
切削油本来の冷却性や洗浄性を低下させます。乳化タイプの油剤では、乳化バランスを崩すことがあります。 - 微生物の栄養源
バクテリアやカビの格好の栄養源となり、腐敗を促進します。タンク液面に油膜を形成することで、酸素の供給を遮断し、嫌気性菌(悪臭の原因菌)の繁殖を助長します。 - 泡立ち助長
油剤の界面状態を変化させ、泡立ちの原因となることがあります。 - 油煙(オイルミスト)増加
加工時の熱で蒸発しやすくなり、オイルミストの発生量を増加させ、作業環境を悪化させます。
- 性能低下
- 発生原因
- その他の異物
- 発生原因
工場内のホコリ、空気中の砂塵、機械の塗装片、シール材やホースの破片、作業者が誤って落としたゴミ(ウエス片など)。 - 影響
フィルターやノズルの詰まり、ポンプへのダメージ、油剤性能の低下などを引き起こします。
- 発生原因
これらの不純物をいかに効率的に除去し、その混入をいかに防ぐかが、清浄度管理の鍵となります。
3. 【切削油】代表的なフィルターの種類と特徴
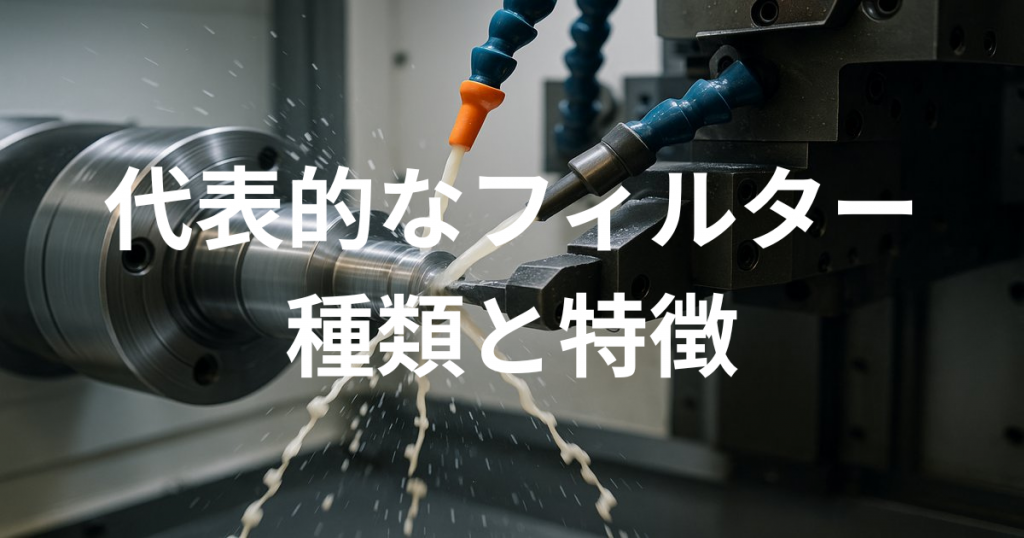
切削油中の固形不純物を除去するために、様々な種類のフィルター(ろ過装置)が用いられています。それぞれの原理と特徴を理解し、目的に合ったものを選ぶことが重要です。
種類 | ろ過原理 | 特徴 | 主な用途 | メリット | デメリット | メンテナンス |
ストレーナー/スクリーン | 網(メッシュ)による遮断 | 構造単純、安価、粗いろ過 | ポンプ保護、粗ゴミ除去 | 低コスト、低圧損 | 微細粒子は除去不可 | 定期清掃 |
メッシュフィルター (バッグ/カートリッジ) | フィルターメディア表面での捕捉 | ろ過精度(μm)多様、交換容易タイプ多い | 一般的な固形物除去 | 比較的安価、多くの種類から選べる | 捕捉容量小さい場合あり、目詰まりしやすい場合あり | 定期交換/清掃 |
カートリッジフィルター (デプスタイプ) | フィルターメディア内部での捕捉 | 高い捕捉容量、比較的長寿命、精密ろ過向け | 微細粒子除去、高精度加工、仕上げ加工 | 微細粒子除去能力高い、捕捉容量大きい | 比較的高価、交換が必要 | 定期交換 |
マグネットセパレーター | 磁力による吸着 | 鉄系粒子(磁性体)に効果大、消耗品少ない | 鋳鉄加工、鉄系研削加工 | 消耗品ほぼ不要、連続運転可能 | 非磁性体は除去不可 | 吸着物除去/清掃 |
遠心分離機 (サイクロン/セパレーター) | 遠心力による比重分離 | フィルターメディア不要、微細粒子除去可能、連続運転可能 | アルミ・鋳物加工、研削加工、油水分離も可能 | 消耗品不要、メンテナンス比較的容易 | 初期コスト高い、設置スペース必要、比重差小さい粒子は分離困難、電力消費 | スラッジ排出/清掃 |
ペーパーフィルター (ロール式など) | ろ紙による捕捉 | 高いろ過精度可能、自動供給タイプあり | 研削加工、精密加工 | 微細粒子除去能力高い、清浄度を安定させやすい | 消耗品(ろ紙)コスト、廃棄物発生、装置が大型化しやすい | ろ紙交換/スラッジ除去 |
真空ろ過装置 | 減圧によるろ紙ろ過 | 高いろ過効率、脱水効果も期待できる | 研削スラッジ除去 | 微細粒子を高効率で除去 | 装置コスト高い、設置スペース必要、メンテナンス | ろ紙交換/スラッジ除去 |
これらは代表的な例であり、他にも様々な原理や構造のフィルターが存在します。それぞれの特徴を理解することが、適切な選定の第一歩です。
4. フィルターの選び方と交換時期の目安
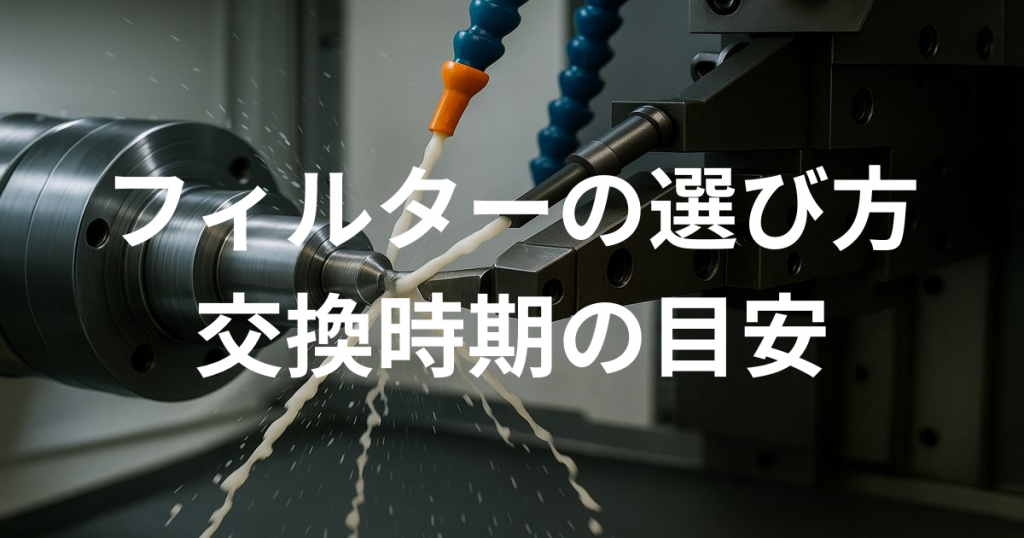
数あるフィルターの中から、自社の加工や要求品質に最適なものを選び、適切なタイミングでメンテナンス(交換・清掃)を行うことが、清浄度管理の効果を最大化する鍵となります。
フィルター選定のポイント
- 除去したい不純物の種類と大きさ
- 何を(切りくず、砥粒、摩耗粉など)、どのくらいの大きさ(μm:マイクロメートル)まで除去したいのかを明確にします。加工精度や面粗度の要求レベルから、必要なろ過精度(公称ろ過精度、絶対ろ過精度)を決定します。
- 磁性体(鉄系)が主ならマグネットセパレーター、非磁性体(アルミ、砥粒など)ならカートリッジフィルターや遠心分離機などを検討します。
- 注意点
必要以上に細かいろ過精度を選ぶと、フィルターがすぐに目詰まりし、交換頻度が増えたり、圧力損失が大きくなったりして、かえってコスト増やトラブルの原因となることがあります。要求品質を満たす範囲で、適切な精度を選びましょう。
- 加工内容と被削材
- 切りくずの量や形状(例:鋳鉄の細かい粉、アルミの連続した切りくず)によって、フィルターの目詰まりしやすさや、適した除去方式(マグネット、遠心分離など)が変わります。
- 研削加工のように大量の微細粒子が発生する場合は、ペーパーフィルターや高精度カートリッジフィルター、遠心分離機などが適しています。
- クーラントの種類と流量
- 使用している切削油の種類(水溶性、不水溶性、粘度)に対応したフィルター材質や構造を選びます。
- 工作機械のクーラントポンプが供給する流量(L/min)に見合った、あるいはそれ以上の処理能力を持つフィルターを選定する必要があります。処理能力が不足すると、クーラント供給量が低下し、加工に悪影響が出ます。
- 設置スペースとコスト
- フィルター装置を設置するためのスペースが確保できるかを確認します。
- 初期導入コストだけでなく、消耗品(フィルターエレメント、ろ紙など)の費用や交換の手間、メンテナンス費用といったランニングコストも考慮して、総合的なコストパフォーマンスを評価します。
- フィルターの組み合わせ(多段ろ過)
- 粗いろ過(ストレーナー、マグネット)と精密ろ過(カートリッジ、ペーパー)など、複数のフィルターを組み合わせることで、それぞれのフィルターの負荷を軽減し、効率的に高い清浄度を得られる場合があります。
フィルター交換・清掃時期の目安
フィルターは、不純物を捕捉するにつれて目詰まりを起こし、その性能が低下します。適切な時期にメンテナンスを行うことが重要です。
- 差圧計による管理(推奨)
- フィルターの入口と出口の圧力差(差圧)を測定する差圧計(差圧ゲージ、差圧スイッチ)を設置し、差圧が予め設定した上限値(メーカー推奨値や経験値)に達したら、フィルターが目詰まりしたと判断し、交換または清掃を行います。これが最も確実で効率的な管理方法です。差圧の上昇を監視することで、交換時期を予測することも可能です。
- 定期交換・清掃
- 過去の運用実績やメーカーの推奨に基づき、「〇ヶ月ごと」「〇時間運転ごと」といった形で、定期的に交換または清掃を行う方法です。管理は容易ですが、加工負荷の変動などにより、最適なタイミングとずれる可能性があります。差圧管理と併用するのが理想的です。
- 目視確認
- フィルターエレメントの汚れ具合を目で見て判断する方法もありますが、内部の目詰まり具合は外観だけでは分かりにくいため、あくまで簡易的な目安と考えましょう。
交換・清掃を怠るリスク
目詰まりしたフィルターを放置すると、以下のような問題が発生します。
- 流量低下
クーラント供給量が減少し、冷却・潤滑不足による加工不良や工具寿命低下を招きます。 - バイパス流の増加
フィルター内部の圧力が高まり、設計によってはフィルターを通らないバイパス流が増加し、汚れた油がそのまま循環してしまう可能性があります。 - フィルターの破損
過大な圧力により、フィルターエレメント自体が破損し、捕捉した不純物が下流へ流出してしまう危険性があります。
フィルターの選定や交換時期について不明な点があれば、機械メーカーやフィルターメーカー、そして私たち切削油メーカー(サンワケミカル株式会社)にご相談ください。お客様の状況に合わせたアドバイスを提供できます。
5. 清浄度管理のレベルアップ:その他の対策と最新技術
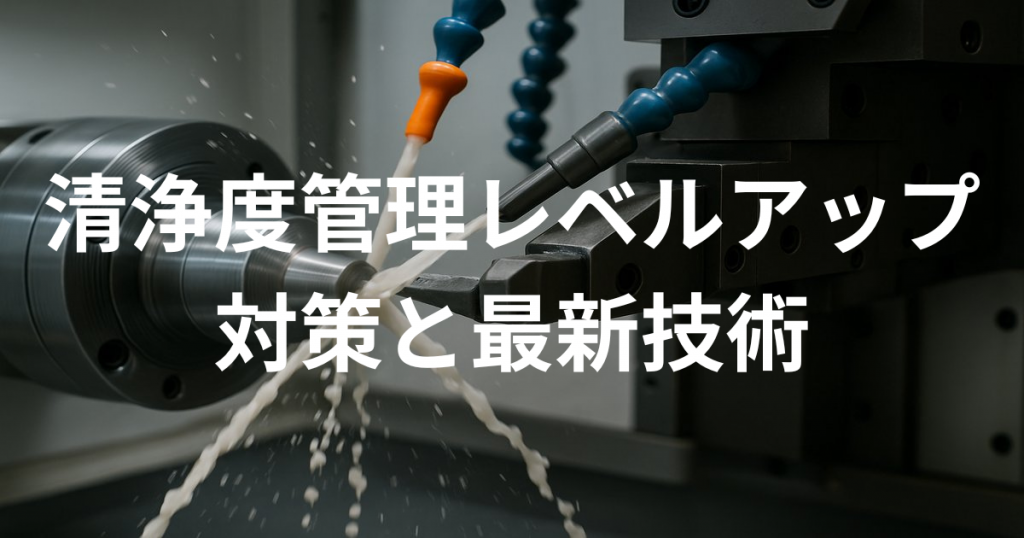
効果的なフィルタリングは清浄度管理の核ですが、それ以外にも様々な対策を組み合わせることで、さらに管理レベルを高めることができます。また、最新技術の動向にも注目してみましょう。
フィルター以外の清浄度維持対策
- オイルスキマーによる浮上油除去
- クーラントタンク液面に浮上する混入油(摺動面油など)は、油剤性能の低下や微生物繁殖の原因となります。オイルスキマー(ベルト式、ディスク式、フロート式など)を設置し、定期的に浮上油を除去することは、清浄度維持と腐敗防止に非常に効果的です。フィルターだけでは除去できない液体の不純物対策として重要です。
- 殺菌・防カビ処理による微生物抑制
- 微生物(バクテリア、カビ)の繁殖は、悪臭、pH低下、スライム生成によるフィルター目詰まりなど、多くの問題を引き起こします。根本対策は、タンク清掃と耐腐敗性の高い油剤の使用ですが、必要に応じて適切な殺菌剤・防カビ剤を使用することで、微生物の増殖を抑制し、清浄度を維持することができます。ただし、薬剤の選定・使用方法は必ずメーカーに相談し、適切な用法・用量を守ることが重要です。
- タンク構造・運用によるスラッジ対策
- クーラントタンクの形状を、スラッジが堆積しにくい(例:底面に傾斜をつける)、流れがよどまないように設計・改善します。
- タンク内に適切な隔壁(バッフルプレート)を設け、清浄な液と汚れた液のエリアを分離することも有効です。
- 定期的なタンク清掃は、フィルターでは除去しきれない沈殿スラッジを除去する上で不可欠です。
- クーラント液の冷却
- 液温を適正範囲(一般的に40℃以下)に保つことは、油剤の粘度変化を抑え、フィルタリング効率を安定させます。また、高温は微生物の繁殖を助長するため、冷却は腐敗防止にも繋がります。必要に応じてクーラントチラーの導入を検討します。
最新技術の動向(参考)
より高度な清浄度管理を目指すための技術も進化しています。
- 精密ろ過技術
半導体製造などで用いられるような、サブミクロン(1μm未満)レベルの超微細粒子を除去できる高性能フィルター(例:膜フィルター、中空糸膜フィルター)も、特定の精密加工分野で応用され始めています。 - 静電浄油技術
油中に電界をかけ、静電気の力で微細な汚染物質(金属粉、酸化劣化物、スラッジなど)を吸着・除去する技術。フィルターでは除去しきれない微細な汚染物質にも効果が期待されます。 - リアルタイム清浄度モニタリング
センサー技術とIoTを活用し、クーラント中の粒子数や汚染度(コンタミネーションレベル)をリアルタイムで連続的に監視するシステムが登場しています。これにより、フィルターの交換時期を最適化したり、異常を早期に検知したりすることが可能になります。
ステップアップの考え方
まずは、自社に必要な清浄度レベルを明確にし、基本的なフィルター管理(適切な選定、差圧管理、定期メンテナンス)を徹底することが第一歩です。その上で、浮上油の問題があればオイルスキマーを導入、微生物の問題があれば耐腐敗性油剤への変更や殺菌処理を検討、といった形で、課題に応じた対策を追加していきます。最新技術の導入は、さらなる品質向上や自動化、予知保全などを目指す段階で検討すると良いでしょう。
サンワケミカル株式会社では、お客様の切削油の汚染状況を分析し、現状の清浄度レベルを評価した上で、最適なフィルター選定や管理方法、さらには清浄度維持に貢献する切削油のご提案など、トータルなサポートを提供しています。
こちらからお気軽にお問い合わせください。
サンワケミカル株式会社お問い合わせ
http://sanwachemical.co.jp/contact/
まとめ
本記事では、切削油の清浄度管理の重要性から始まり、主な不純物の種類と影響、代表的なフィルターの種類と特徴、適切なフィルターの選び方と交換時期、そしてさらに管理レベルを高めるための対策や最新技術について解説しました。
切削油の清浄度管理は、「汚れたらきれいにする」という対症療法だけでなく、「いかに汚さないか」「いかに効率よく清浄度を維持するか」という予防的な視点が重要です。適切なフィルタリングシステムの選定と運用、そしてオイルスキマーやタンク管理といった周辺対策を組み合わせることで、常に切削油を最適な状態に保つことが可能になります。
清浄な切削油は、加工品質の向上、工具寿命の延長、機械トラブルの減少、そして油剤寿命の延長によるコスト削減と環境負荷低減に大きく貢献します。ぜひ、本記事を参考に、自社の清浄度管理体制を見直し、より高いレベルの品質と生産性を目指してください。
サンワケミカル株式会社は、長年の経験と技術に基づき、多種多様な切削油剤を開発・製造しております。お客様の加工条件やニーズに合わせた最適な製品をご提案いたしますので、切削油に関するご相談は、ぜひお気軽にお問い合わせください。
もし、この記事で紹介した対策を試しても問題が解決しない場合や、お使いの切削油に関するより詳細な情報、お客様の特定の加工に最適な油剤の選定についてご相談がありましたら、どうぞお気軽に私たちサンワケミカル株式会社までお問い合わせください。経験豊富な専門スタッフが、お客様の状況を詳しくお伺いし、最適なソリューションをご提案いたします。
サンワケミカル株式会社HP:http://sanwachemical.co.jp/
サンワケミカル株式会社お問い合わせ:http://sanwachemical.co.jp/contact/
サンワケミカル株式会社公式X:https://x.com/sanwachemical
今後も、金属加工の現場で役立つ情報を発信してまいりますので、サンワケミカル株式会社公式ブログにご期待ください。